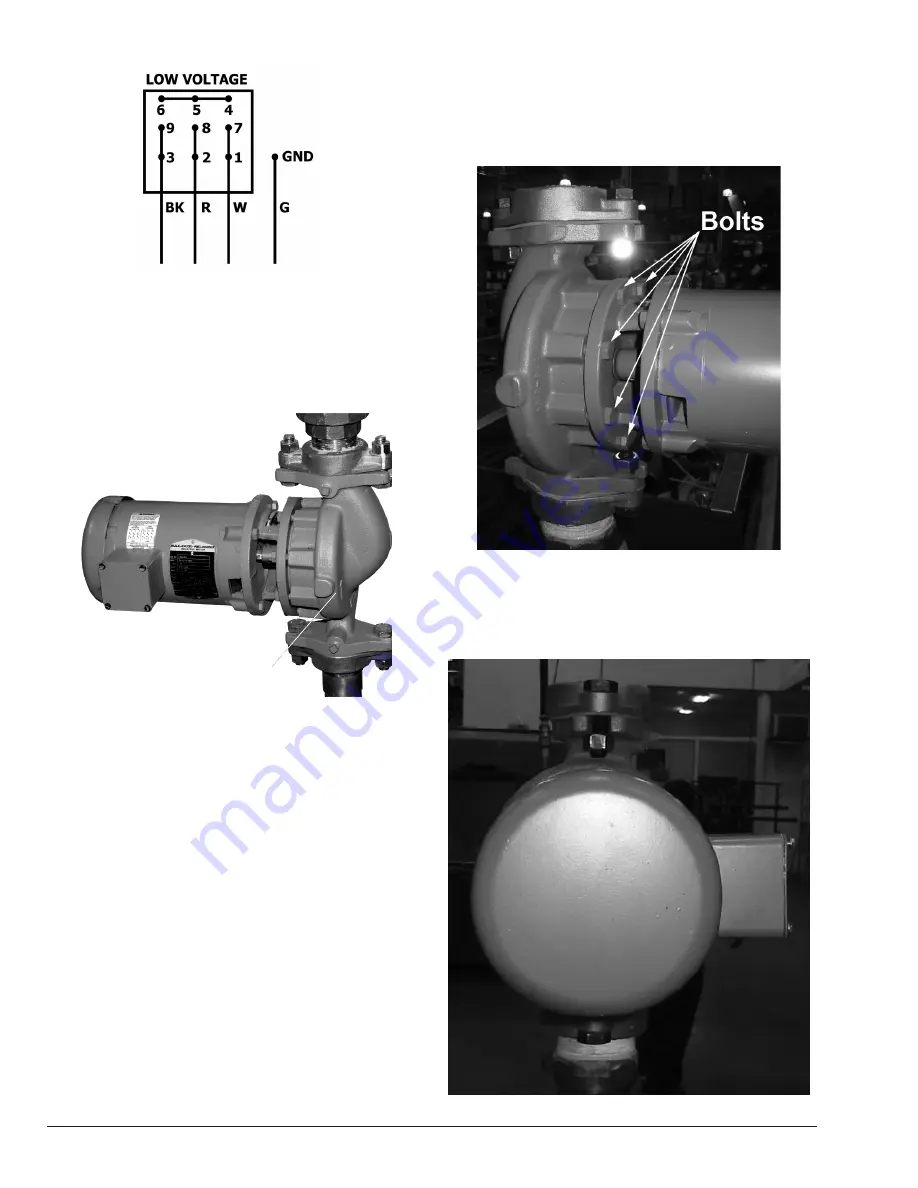
24
Figure 25. Cold Water Run Control Panel and Injector
Pump Wiring
11. Turn heater on to receive a “call-for-heat” and verify
the injector pump is rotating in the proper direction
(clockwise). The pump volute has an arrow cast into
the housing indicating the proper rotational direction.
See
Figure 26
.
DIRECTIONAL ARROW
Figure 26. Directional Arrow
12. If the pump is rotating in the proper direction, secure
the heater from installation.
13. If the pump is rotating incorrectly, turn off power and
swap ONLY two of the line voltage leads into the
pump (for example, swap the red and black leads).
Confirm that the pump now rotates in the proper
direction before proceeding.
14. Secure from installation.
Injection Pump Cover Installation
(Required for Outdoor Installation Only)
Before Starting
1. Turn off power to the unit at the circuit breaker.
2. Turn off gas supply.
3. Shut-off the water supply to the heater and, if
necessary, drain water from the system.
4. Allow heater to cool down before attempting work.
In order to install the pump cover, you will need to rotate the
pump body so that the electrical box is pointing downward,
as outlined in the following steps:
1. Loosen and remove the eight (8) 9/16" bolts holding
the pump body in place. See
Figure 27
.
Figure 27. Remove the eight bolts holding the pump body
in place
2. Remove the pump body then rotate it so that the
electrical box is pointing downward, ensuring not to
damage the seal. See
Figure 28
through
Figure 30
.
Figure 28. Remove the pump body
Содержание Raypak Delta Limited WH1-399B
Страница 14: ...14 Wiring Diagrams Cold Water Start ...
Страница 19: ...19 CWS CONTROL BOX ASSY SEE PAGE 16 FOR HEATER INTERFACE WIRING SEE PAGE 17 Wiring Diagram Multiple Boiler ...
Страница 29: ...29 Wiring Diagrams Cold Water Run SEE PAGE 17 ...
Страница 31: ...31 7 ILLUSTRATED PARTS LISTS Cold Water Start Manufactured from 2006 through current ...
Страница 32: ...32 1 M 8 M Cold Water Start ...
Страница 33: ...33 Cold Water Start Multiple Boiler Interlock ...
Страница 34: ...34 NOTE Sizing is specific to the application ...
Страница 36: ...36 9 M 4 M RAYTHERM MODELS 2100 4001 ONLY 1 H 5 M 6 M 7 M 8 M 10 M 12 M 11 M 4 M 2 M 1 M Cold Water Run ...
Страница 37: ...37 NOTE Sizing is specific to the application ...
Страница 38: ...38 NOTES ...
Страница 39: ...39 NOTES ...