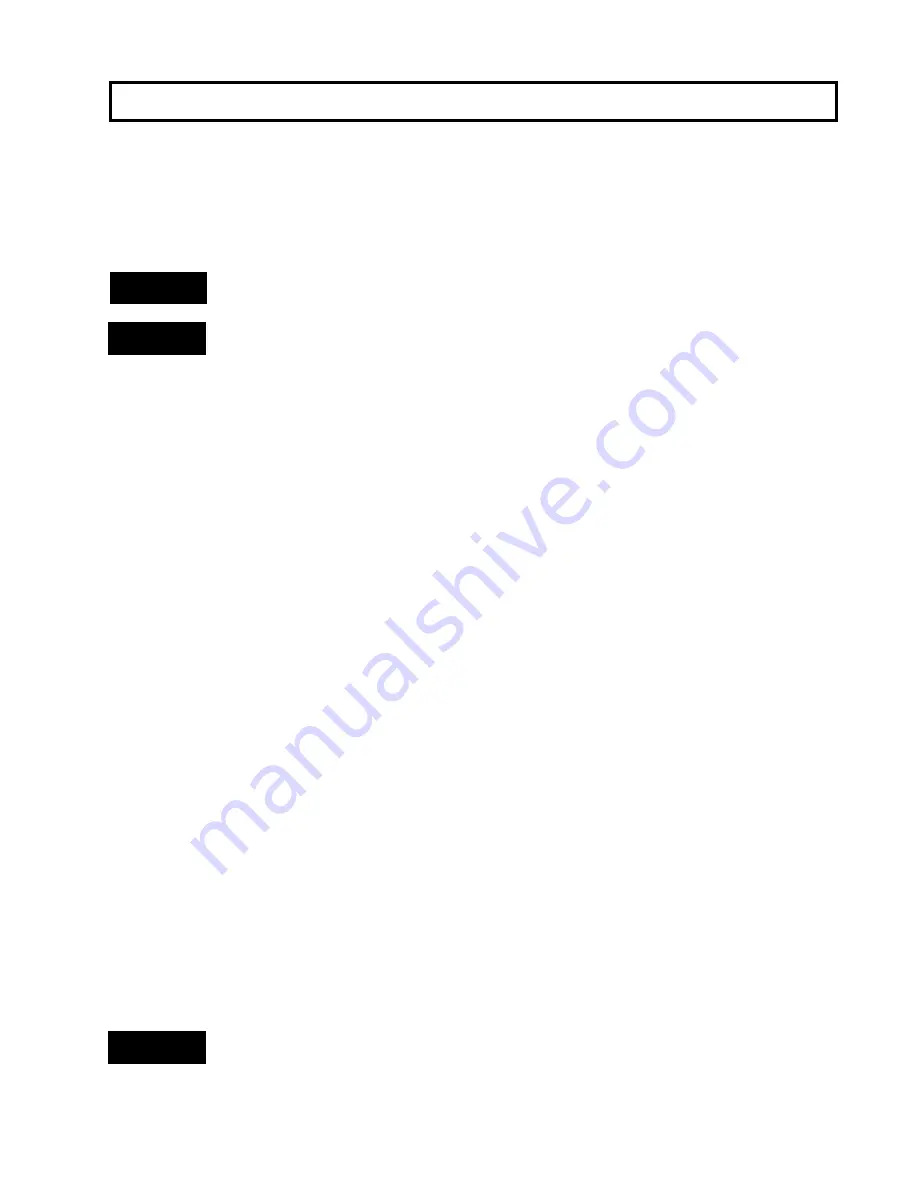
SECTION C: COMBUSTION AND VENTILATION AIR
COMBUSTION AND VENTILATION AIR (Indoor Units)
The boiler must be supplied with sufficient quantities of non-contaminated air to support proper combustion and equipment
ventilation. Combustion air can be supplied via conventional venting, where combustion air is drawn from the area immedi-
ately surrounding the boiler, or via direct vent, where combustion air is drawn directly from outside. All installations must
comply with the requirements of NFGC for U.S., CAN/CGA B 149.1 and .2 for Canada, and all local codes.
CAUTION:
Combustion air must not be contaminated by corrosive chemical fumes which can damage the boiler
and void the warranty. See appendix A.
NOTICE:
It is recommended that the intake vent be insulated to minimize sweating.
DIRECT VENT-INSTALLATON
If outside air is drawn through the intake pipe directly to the unit for combustion:
1.
Install combustion air direct vent in accordance with Section J-3 and Section J-4 of this manual.
2.
Provide adequate ventilation.
3.
In cold climates, and to mitigate potential freeze-up, Raypak highly recommends the installation of a motorized sealed
damper to prevent the circulation of cold air through the boiler during the non-operating hours.
CONVENTIONAL COMBUSTION AIR SUPPLY (FOR U.S. INSTALLATION ONLY)
(a)
All Air from Inside the Building
. The confined space shall be provided with two permanent openings communicating
directly with an additional room(s) of sufficient volume so that the combined volume of all spaces meets the criteria for an
unconfined space. The total input of all gas utilization equipment installed in the combined space shall be considered in
making this determination. Each opening shall have a minimum free area of 1 square inch per 1,000 Btu per hour (22 cm
2
per
kW) of the total input rating of all gas utilization equipment in the confined space, but not less than 100 square inches
(645 cm
2
). One opening shall commence within 12 inches (30 cm) of the top, and one opening shall commence within 12 inches
(30 cm) of the bottom, of the enclosure. The minimum dimension of air openings shall be not less than 3 inches (8 cm).
(b)
All Air from Outdoors.
The confined space shall communicate with the outdoors in accordance with methods 1 or 2. The
minimum dimension of air openings shall not be less than 3 in. (8cm). Where ducts are used, they shall be of the same cross-
sectional area as the free area of the openings to which they connect.
1. Two permanent openings, one commencing within 12in. (30cm) of the top, and one commencing within 12in. (30cm) of
the bottom, of the enclosure shall be provided. The openings shall communicate directly, or by ducts, with the outdoors or
spaces (crawl or attic) that freely communicate with the outdoors.
a. Where directly communicating with the outdoors or where communicating to the outdoors through vertical ducts,
each opening shall have a minimum free area of 1 sq in. per 4000 Btu per hr (5.5cm
2
per kW) of total input rating of all
equipment in the enclosure.
b. Where communicating with the outdoors through horizontal ducts, each opening shall have a minimum free area of 1
sq in. per 2000 Btu per hr (11 cm
2
per kW) of total input rating of all equipment in the enclosure.
2. One permanent opening, commencing within 12 in. (30cm) of the top of the enclosure, shall be permitted where the
equipment has clearances of at least 1 in. (2.5 cm) from the sides and back and 6 in. (16cm) from the front of the appliance. The
opening shall directly communicate with the outdoors or shall communicate through a vertical or horizontal duct to the
outdoors or spaces (crawl or attic) that freely communicate with the outdoors, and shall have a minimum free area of:
a. 1 sq in. per 3000 Btu per hr (7 cm2 per kW) of the total input rating of all equipment located in the enclosure, and
b. Not less than the sum of the areas of all vent connectors in the confined space.
11
WARNING:
Do not use one permanent opening method if the equipment room is under negative
pressure condition or the equipment is common vented with other gas-fired appliances.
Содержание 302-902
Страница 7: ...7 General Information ...
Страница 49: ...49 WIRE DIAGRAM MODEL 302 402 Reference Drawing Number M152462 Rev M H4 W1 ...
Страница 50: ...WIRE DIAGRAM MODEL 302 402 Reference Drawing Number M152470 Rev J H3 W3 50 ...
Страница 51: ...51 WIRE DIAGRAM MODEL 502 752 Reference Drawing Number M152464 Rev R H3 HW3 ...
Страница 52: ...WIRE DIAGRAM MODEL 902 Reference Drawing Number M152465 Rev P H3 W3 52 ...