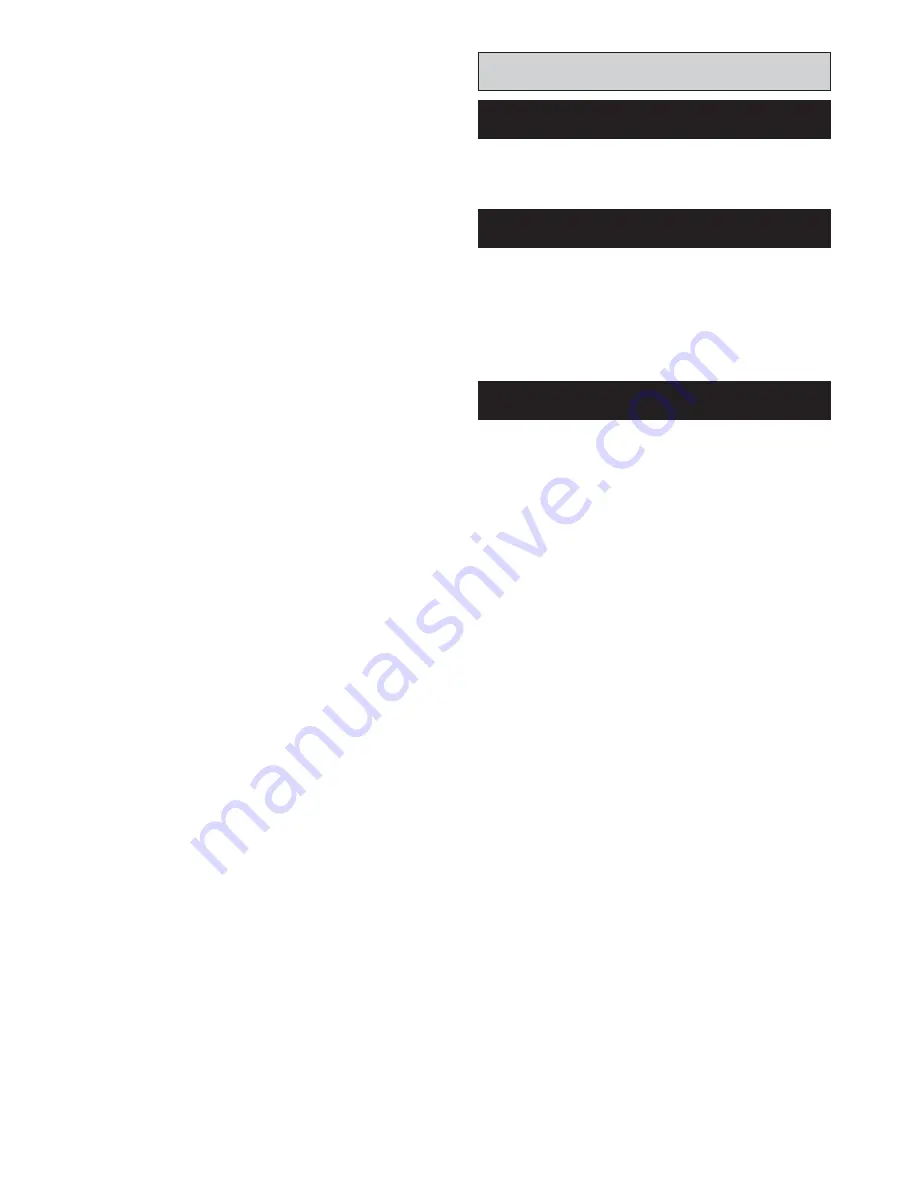
Cooker Burner
SEE FIG. 12
After checking the burner is level and that the oil is the
correct depth in the burner disconnect the oil feed pipe to
the burner and attach adaptor for measuring oil rates by
the DRIP FEED METHOD.
To make adjustments to the control it is necessary to
remove the electric top if fitted, and the name plate to
expose the adjusting screws. Do not remove the pre-
punched knockouts in the name plate.
ACTUATING PIN ADJUSTMENT (IF ELECTRIC TOP IS
FITTED)
.
1. Turn the regulating knob to the LOW fire position.
2. Press lightly on the actuating pin and check to see if it
is possible to move the pin up and down.
3. The limit screw should be adjusted, so that the
movement is just eliminated.
CAUTION: Do not over adjust the limit screw as excessive
low fire flow rates will occur when the electric head is de-
activated.
ADJUSTING THE HIGH FIRE FLOW RATES
- 13cc/min to 13.5cc/min
1. Turn the regulating knob to the high fire position to
expose the adjustment screw.
NOTE: ALLOW 7 MINUTES FOR THE FLOW TO
STABILISE BEFORE TAKING THE RATE. IF THE RATE
IS INCORRECT THEN ALLOW 2 MINUTES BETWEEN
RE-SETTING AND THE NEXT RATE.
2. Rotate the adjusting screw anti-clockwise, to increase
and clockwise to decrease the flow rates.
NOTE: The adjusting screw is highly sensitive and should
only be adjusted in small increments.
ADJUSTING THE LOW FIRE RATES
-4.75cc/min but no lower than 4.5cc/min
1. Turn the regulating knob to low fire position to expose
the low fire adjustment screw.
NOTE: ALLOW 7 MINUTES FOR THE FLOW TO
STABILISE BEFORE TAKING THE RATE. IF THE RATE
IS INCORRECT THEN ALLOW 2 MINUTES BETWEEN
RE-SETTING AND THE NEXT RATE.
2. Rotate the adjusting screw anti-clockwise, to increase
and clockwise to decrease the flow rates.
3. After adjustment it may be necessary to re-adjust the
low fire limit screw. Check the actuating pin for movement.
4. Re-fit name plate and electric top if applicable.
Checks to ensure electrical safety should be carried out
by a competent person.
The whole of the system should be thoroughly flushed out
with cold water without the pump in position. Ensure that
all valves are open.
With the pump fitted, the system should be filled and air
locks cleared. Vent all heat emitters and check for water
soundness.
SEE FIG. 13
Check that:-
1. The boiler system is full of water and all valves are fully
open.
2. Any room thermostat is
ON
.
3. Any programmer or time switch is set at continuous
heating.
4. Ensure the electricity supply is
ON
, that the pump is
running.
5.
Lighting Sequence
(i) Set the boiler thermostat knob
H
to a thermostat
setting of 80°C (180°F) whereupon the airfan unit will
become operative, the ignition glo-coil
K
will start to heat
up.
(ii) After 1 minute, the pilot oil solenoid will energise and
allow pilot oil supply to the boiler burner. Entry and rate of
pilot oil flow is dependent on a small static head of oil from
the constant level oil valve.
Reduction or loss of this head, will result in pilot oil
starvation e.g. low constant oil valve location or
conversant, high burner pot location.
(iii)The pilot oil supply will ignite within 30 seconds of oil
flow, and be recognised by the thermocouple, which
switched the pilot solenoid and glo-coil
OFF
, and switches
the main oil flow solenoid
ON
. The boiler will fire and run.
(iv)The activated boiler thermostat isolates power from
the main oil solenoid, to interrupt the oil supply, but the fan
remains energised on an overrun period time of about 5
minutes depending on the length of
ON
time boiler cycle.
This enables all the oil in the burner to be burned and also
the cooling of the flame sensor, which then isolates power
from the fan, ready for the next cycle call. With the call for
hot water, the boiler thermostat re-activates, and the
complete cycle starts again.
(v) Allow the boiler burner to operate for 2 to 3 cycles,
then during a boiler
ON
period, proceed with the following
checks:-
12
WATER CIRCULATION SYSTEM
LIGHTING THE BOILER BURNER
ELECTRICAL INSTALLATION
COMMISSIONING AND TESTING