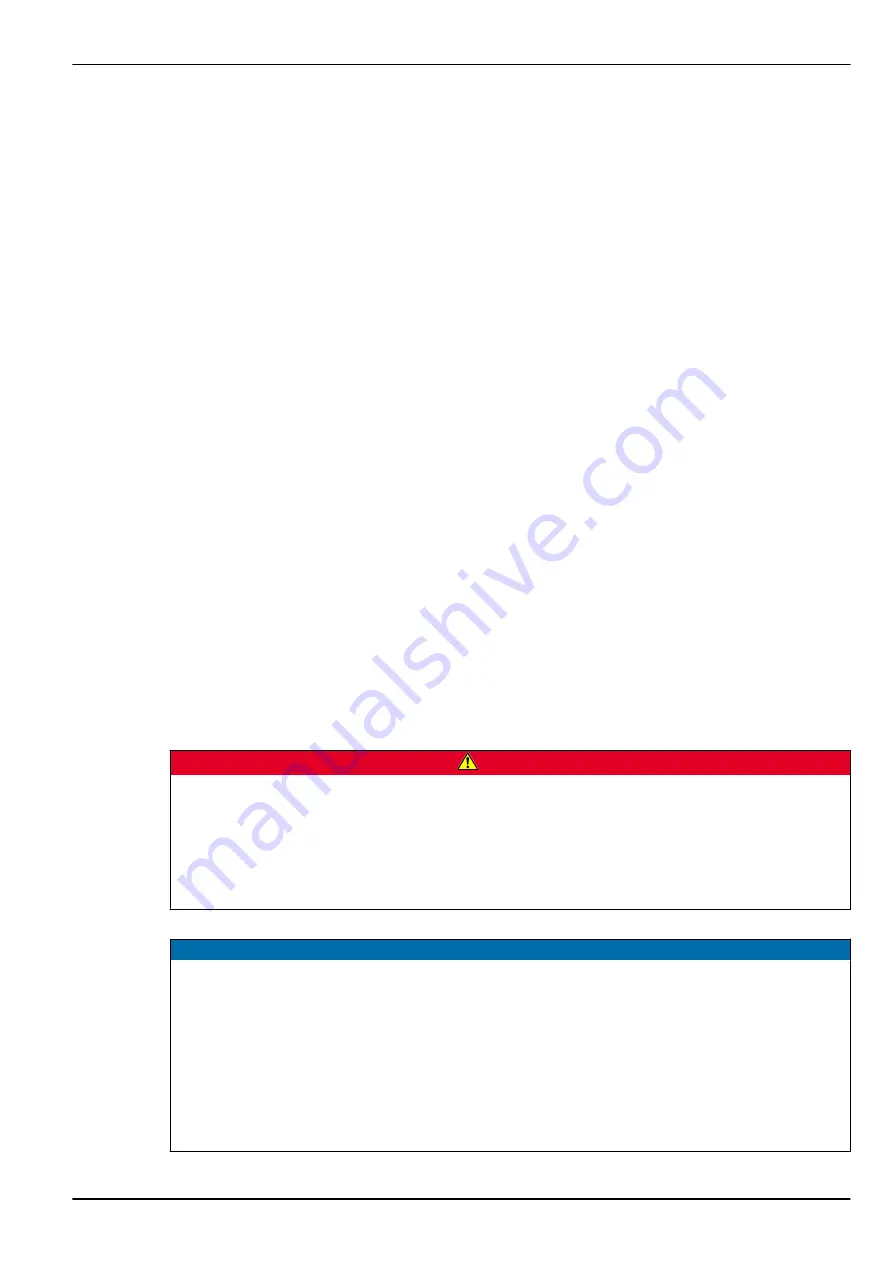
6.3
Tractor requirements
To ensure a safe and correct use of the machine, the tractor must meet the necessary mechanical,
hydraulic, and electrical requirements.
•
Tractor engine power: at least 180 HP
•
Hydraulic pressure: 180 bar
•
Oil volume: 35 l/min for conveyor belt drive
•
Coupling types:
○
Ball-type coupling device 80 ISO 24347
○
Hitch towing eye ISO 20019
•
Admissible static load: 3,000 kg, bottom hitching
•
1 double-acting control unit for the conveyor belt drive
•
1 double-acting control unit for the hopper cover (optional equipment)
•
1 single-acting control unit for the limited and full border spreading system TELIMAT
(optional equipment equipment)
•
1 double-acting control unit for the spreading width limiter GSE 60 (optional equipment)
•
Universal drive shaft connection:
○
1 3/8 inches, 6-part, 750 rpm or
○
1 3/4 inches, 20-part, 750 rpm
•
Hydraulic connectors as per ISO 15657
•
Operating voltage: 12 V, must also be ensured for multiple actuators
•
ISOBUS connection according to ISO 11 783
•
7-pin socket for the lighting system
•
Connections for the pneumatic brake system DIN ISO 1728 (control line and supply line)
6.4
Mounting the universal drive shaft on the machine
DANGER!
Danger of pulling in on the rotating universal drive shaft
Installing and removing the universal drive shaft while the motor is running may cause serious
injuries (crushing, pulling into the rotating shaft).
u
Turn the tractor engine off and remove the ignition key.
u
Make sure that the universal drive shaft cover is in good condition.
NOTICE!
Material damage due to an unsuitable universal drive shaft
The machine is equipped with a universal drive shaft that is designed according to the device and
performance.
The use of incorrectly dimensioned or inadmissible drive shafts, for instance without guard or
suspension chain, may cause personal injury or lead to damage to the tractor and/or the machine.
u
Use only universal drive shafts approved by the manufacturer.
u
Follow the directions in the operator’s manual of the universal drive shaft manufacturer.
6. Commissioning
AXENT 90.1
5903360
45
Содержание AXENT 90.1
Страница 119: ...12 Appendix 12 Appendix AXENT 90 1 5903360 119...
Страница 126: ......