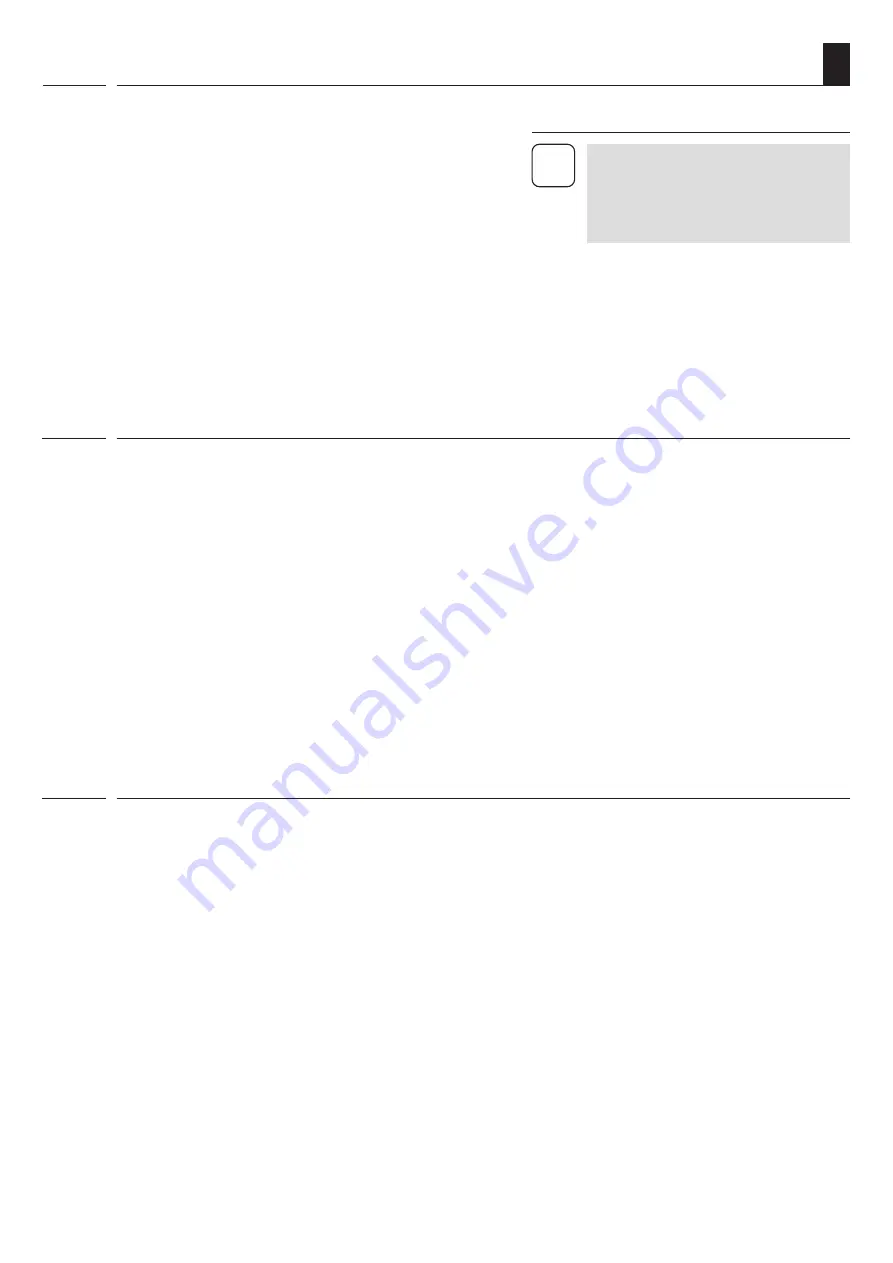
10
EN
6.2 Obstacle detection function
The tubular motor stops and automatically travels
briefly in the opposite direction (reversing), in the
event that the roller shutter hits an obstacle while
closing.
Requirements for correct obstacle detection:
The catch must be mounted with the freewheel
mechanism (see fig. 8, page 14), original fac-
tory settings.
The roller shutter must be mounted to the wind-
ing shaft with the ties or with the fixed shaft
connector.
The roller shutter must always run vertically, eas-
ily and freely in the guide rails of the window.
6.3 Function of the shutter length compensation
The shutter length compensation is active subse-
quent to the automatic learning process for the
upper end point. Afterwards, the tubular motor
no longer runs to the upper end stop in order to
protect the roller shutter.
For example, the ageing of roller shutters can
cause the automatically learned runs to be
changed over a period of time. In order to compen-
sate for this, the tubular motor periodically runs
automatically to the upper end stop (the cycle for
this is set at the factory).
The shutter length compensation operates
automatically during normal operation, so that
generally you will not notice it.
If one of the end points is manually se or if the
freewheel mechanism is deactivated, then the
shutter length compensation is
inactive
.
i
i
Information about multi-part systems
i
When using a tubular motor with ob-
stacle detection in multi-part systems
(several screens powered by a wind-
ing shaft), the obstacle detection may
respond late or not at all.
The following conditions must be observed and
followed if the catch has been mounted
without
the freewheel mechanism
, see page 14.
Conditions for the correct function of the mo-
tor if the catch has been mounted without the
freewheel mechanism:
The obstacle detection is not active.
Self-learning operation only possible
with rigid shaft connectors:
> The roller shutter must be mounted to the
winding shaft with rigid shaft connectors.
> The roller shutter must be fitted with stoppers
or an end-rail, see page 18.
End point setting when using ties:
> The lowest end point must be set manually.
6.4 Functions if the catch has been mounted without the freewheel mechanism
i