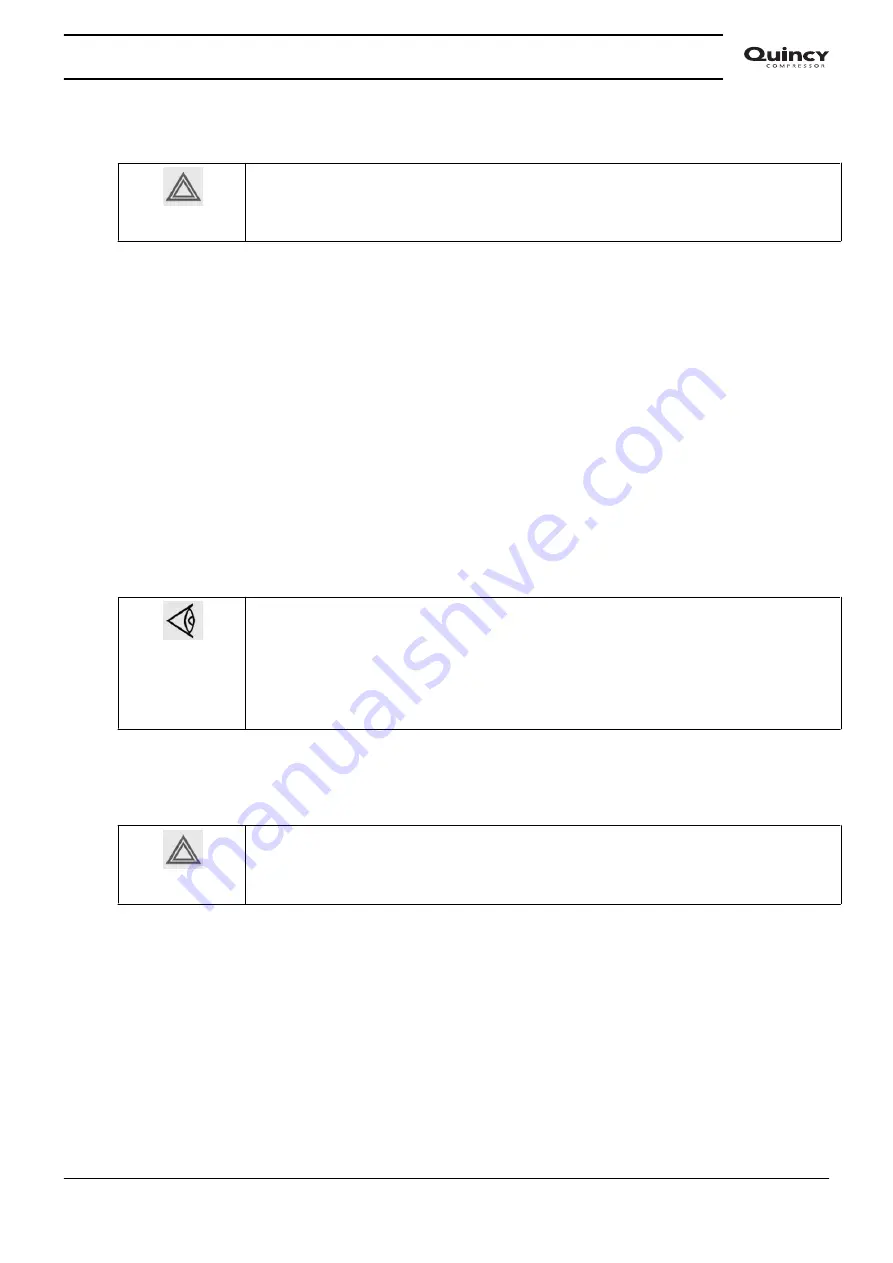
1.3
Safety precautions during operation
All responsibility for any damage or injury resulting from neglecting these precautions, or
non-observance of the normal caution and care required for installation, operation,
maintenance and repair, even if not expressly stated, will be disclaimed by the
manufacturer.
1. Persons switching on remotely controlled machines shall take adequate precautions to
ensure that there is no one checking or working on the machine. To this end, a suitable
notice shall be affixed to the remote start equipment.
2. Never operate the device in the presence of flammable or toxic fumes, vapours or particles.
3. Never operate the device below or in excess of its limit ratings.
4. Do not operate the device when there are flammable or toxic fumes, vapors or particles.
5. Keep all bodywork doors and panels closed during operation. The doors may be opened for
short periods only, e.g. to carry out routine checks.
6. People staying in environments or rooms where the sound pressure level reaches or
exceeds 90 dB(A) shall wear ear protectors.
7. Periodically check that:
• All guards and fasteners are in place and tight
• All hoses and/or pipes are in good condition, secure and not rubbing
• There are no leaks
• All electrical leads are secure and in good order
8. Never remove or tamper with the safety devices.
Also consult following safety precautions:
Safety precautions during installation
and
Safety precautions during maintenance
These precautions apply to electrical devices.
For precautions applying to the connected equipment consult the relevant instruction
book.
Some precautions are general and cover several machine types and equipment; hence
some statements may not apply to your machine.
1.4
Safety precautions during maintenance or repair
All responsibility for any damage or injury resulting from neglecting these precautions, or
non observance of the normal caution and care required for installation, operation,
maintenance and repair, even if not expressly stated, will be disclaimed by the
manufacturer.
1. Use only the correct tools for maintenance and repair work.
2. Use only genuine spare parts.
3. A warning sign bearing a legend such as "Work in progress - do not start" shall be attached
to the starting equipment, including all remote start equipment.
4. Persons switching on remotely controlled machines shall take adequate precautions to
ensure that there is no one checking or working on the machine. To this end, a suitable
notice shall be affixed to the remote start equipment.
5. Never use flammable solvents or carbon tetrachloride for cleaning parts. Take safety
precautions against toxic vapors of cleaning liquids.
6. Scrupulously observe cleanliness during maintenance and repair. Keep dirt away by
covering the parts and exposed openings with a clean cloth, paper or tape.
Instruction book
2920 7195 00
5
Содержание QAF 6-1500
Страница 1: ...Quincy Compressed air filters QAF QCF QMF QPF QWS 6 1500 Instruction book...
Страница 2: ......
Страница 5: ...5 6 DIMENSIONS AND WEIGHT 25 Instruction book 2920 7195 00 3...
Страница 33: ......
Страница 34: ...Performance You Demand Reliability You Trust www quincycompressor com...