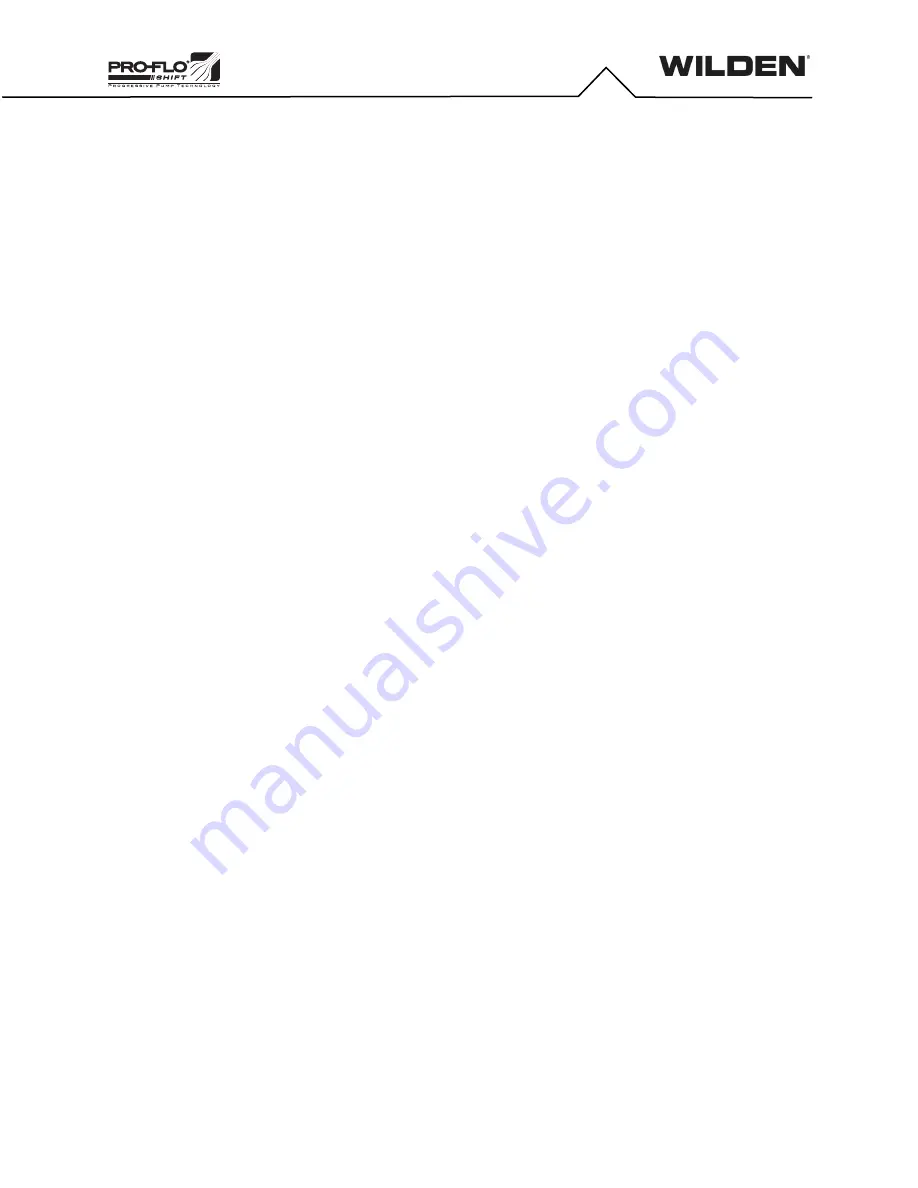
WIL-11430-E-05
13
PS400 Bolted Plastic
Troubleshooting
Pump will not run or runs slowly.
1.
Remove plug from pilot spool exhaust.
2.
Ensure that the air inlet pressure is at least 0.4 bar (5 psig)
above startup pressure and that the differential pressure (the
difference between air inlet and liquid discharge pressures) is
not less than 0.7 bar (10 psig).
3.
Check air inlet filter for debris (see “Suggested Installation,
Operation, Maintenance and Troubleshooting”).
4.
Check for extreme air leakage (blow by) that would indicate
worn seals/bores in the air valve, pilot spool and main shaft.
5.
Disassemble the pump and check for obstructions in the air
passageways or objects that would obstruct the movement of
internal parts.
6.
Check for sticking ball check valves.
a.
If material being pumped is not compatible with pump
elastomers, swelling may occur. Replace ball check
valves and seals with proper elastomers.
b.
Also, as the check valve balls wear out, they become
smaller and can become stuck in the seats. In this case,
replace balls and seats.
7.
Check for any broken inner piston that would cause the air
valve spool to be unable to shift.
Pump runs, but little or no product flows.
1.
Check for pump cavitation. Slow pump speed down to allow
thick material to flow into liquid chambers.
2.
Verify that vacuum required to lift liquid is not greater than the
vapor pressure of the material being pumped (cavitation).
3.
Check for sticking ball check valves.
a.
If material being pumped is not compatible with pump
elastomers, swelling may occur. Replace ball check
valves and seals with proper elastomers.
b.
Also, as the check valve balls wear out, they become
smaller and can become stuck in the seats. In this case,
replace balls and seats.
Pump air valve freezes.
1.
Check for excessive moisture in the compressed air.
a.
Either install a dryer or a hot air generator for compressed
air.
b.
Alternatively, you may use coalescing filter to remove the
water from the compressed air in some applications.
Air bubbles in pump discharge.
1.
Check for a ruptured diaphragm.
2.
Check tightness of outer pistons (see
“Disassembly/Reassembly”).
3.
Check tightness of fasteners and integrity of O-rings and seals,
especially at intake manifold.
4.
Ensure pipe connections are airtight.
Product comes out air exhaust.
1.
Check for a diaphragm rupture.
2.
Check the tightness of the outer pistons to the shaft.
SUGGESTED INSTALLATION, OPERATION, MAINTENANCE
AND TROUBLESHOOTING
Содержание WILDEN Pro-Flo SHIFT PS400
Страница 25: ...WIL 11430 E 05 25 PS400 Bolted Plastic NOTES...
Страница 26: ...WIL 11430 E 05 26 PS400 Bolted Plastic NOTES...
Страница 27: ...WIL 11430 E 05 27 PS400 Bolted Plastic NOTES...