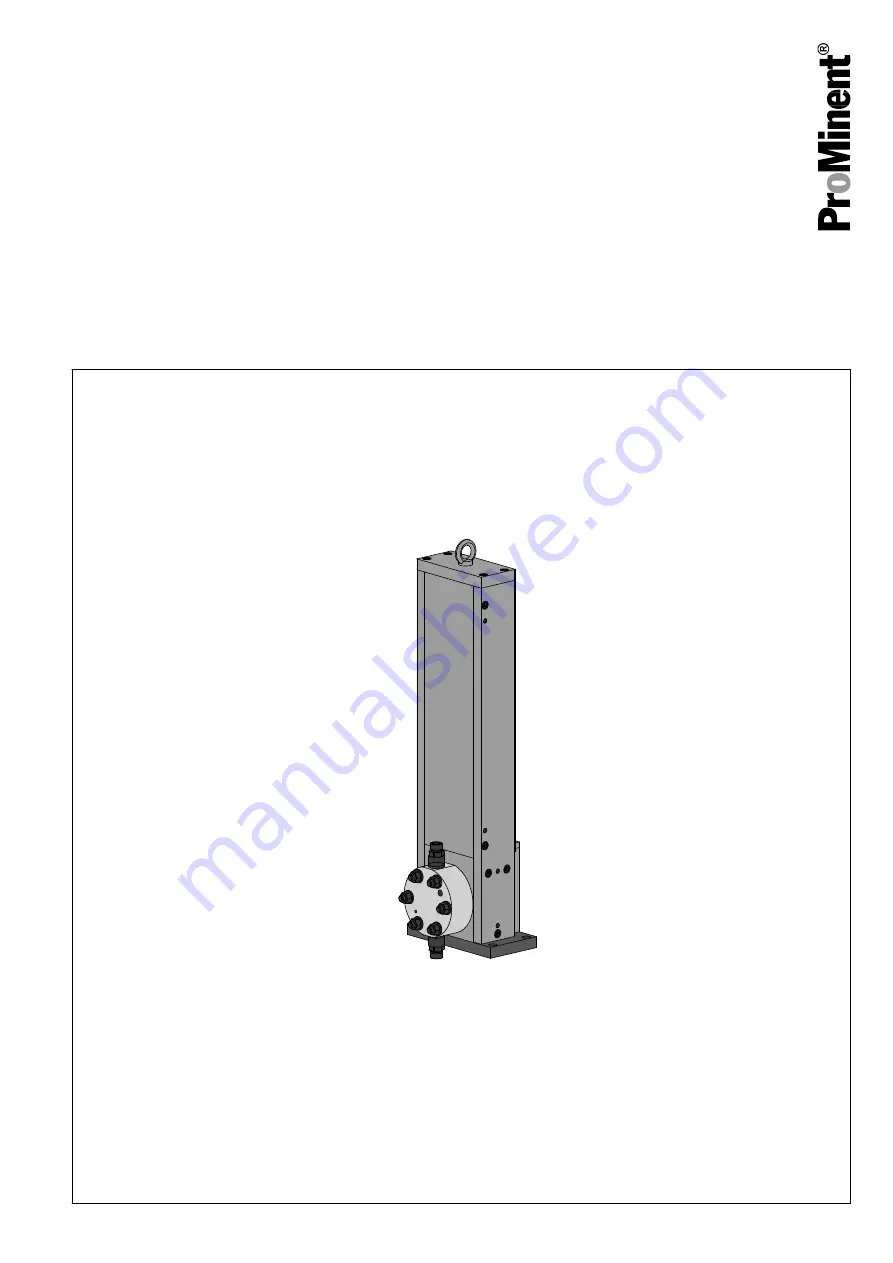
Metering pump
Evolution mikro, EMFa / EMHa
Operating instructions
These operating instructions form part of combined documentation and, as such, are only valid if used in conjunction with
the other documents.
Target group: trained, qualified personnel, unless otherwise required.
EN
Original operating instructions (2006/42/EC)
981089
Version: BA ORL 012 09/21 EN
Please carefully read these operating instructions before use. · Do not discard.
The operator shall be liable for any damage caused by installation or operating errors.
The latest version of the operating instructions are available on our homepage.
Содержание EMFa
Страница 67: ...11 14 Motor data Technical data 67...
Страница 68: ...Technical data 68...