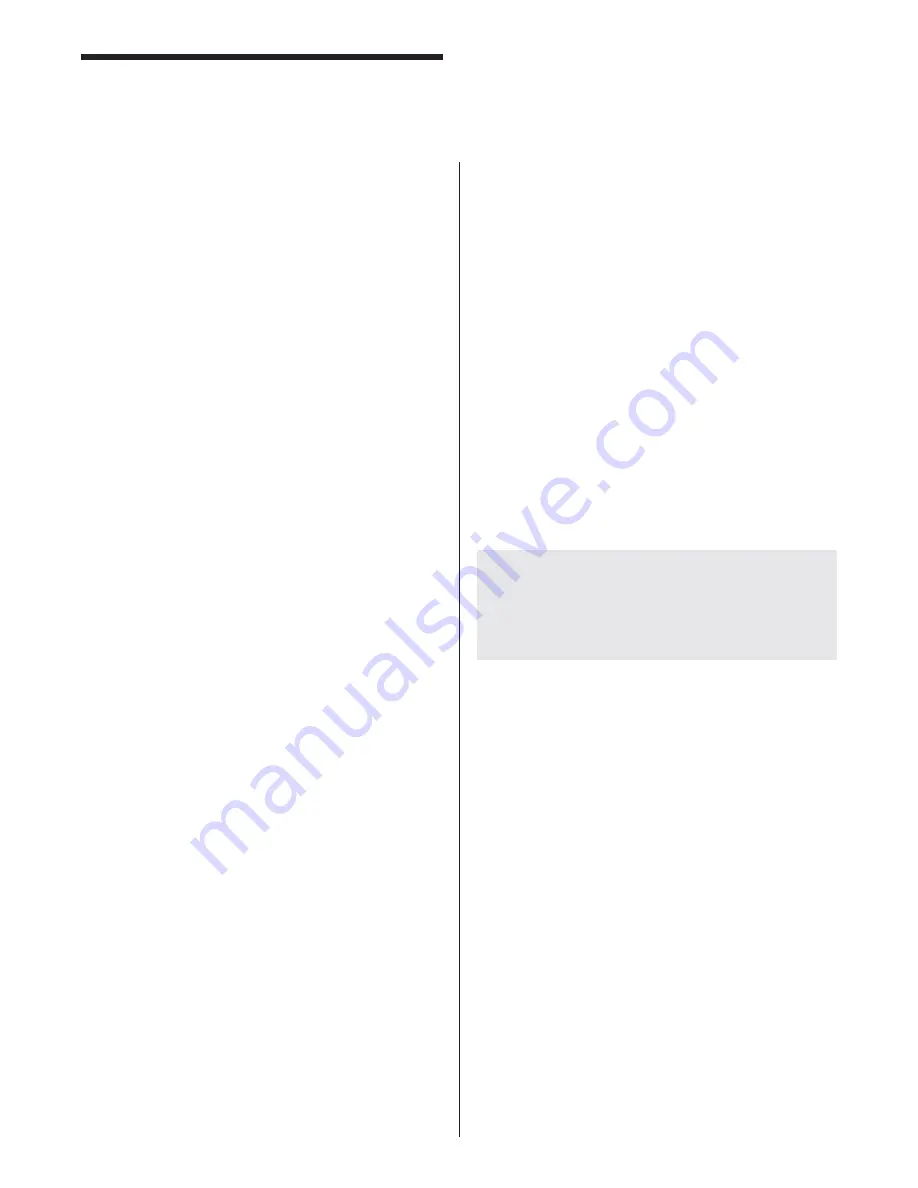
18
Determining the Stop Time of Your Press to Find
Your Safety Distance
ANSI Standard B11.19-1990 E5.6
E5.6.1
When using a time-based brake monitor it
becomes necessary to measure the stopping time at both
the end of the cycle (top stop) and during the closing
portion of the machine cycle (90º from top stop test).
a. If the stop time is greater than the time measured
during the closing cycle, set the brake monitor to
this time plus the variance factor.
b. If the stopping time measured at the end of the
machine cycle is less than the closing stop time,
there are two methods of setting the brake monitor
and calculating the safety distance:
1. Set the brake monitor at the end of cycle time (top
stop) plus the variance factor* and use the closing
time plus the variance factor for calculating the
safety distance. This method will allow the safety
device to be located closer to the hazardous area
but may cause nuisance tripping of the brake
monitor if the machine tool stops during the closing
portion of the machine cycle.
2. Set the brake monitor to the closing cycle stop
time. When this is done, it is necessary to increase
the safety distance since the brake can now
deteriorate from its normal stop time at the end
of the machine cycle before the brake monitor will
detect an adverse deterioration.
The following formula may be used to determine the
stop time for calculating the safety distance:
Ts
= Tsa x Tsa / Tta
where:
Tsa = measured closing stop time (90º from top
stop test)
Tta = measured end of cycle (top stop) time
Ts = time used in the safety distance calculation
This method of setting the brake monitor forces the
safeguarding device to be located at a greater distance
from the hazardous area but eliminates the nuisance
tripping of the brake monitor if the machine tool is
stopped during the closing cycle.
E5.6.4
The following factors may affect stopping
performance of the machine tool: clutch air supply,
counter balance air supply, tooling weight or tonnage
requirements, machine cycle speed, brake wear, and
so forth. When the stopping time changes as a result of
these conditions, it may become necessary to change the
top stop limit switch position, readjust the brake monitor
or adjust the brake mechanism. If such readjustment
is made, care should be taken that the safety distance
used to locate the safeguarding device is recalculated
and, if necessary, the safeguarding should be relocated
to ensure safe operation of the machine tool.
The
variance factor
mentioned in the above ANSI
standard is a number to be determined by the
employer that allows for changes in the stopping time
due to factors listed above in E5.6.4.
Determining the WARN and FAIL Set Points
The Failure set point is the stop time value that you
have just determined above and will use in your safety
distance equation (this equation should be found in the
manual of all equipment used to activate or guard your
equipment). This value includes the variance factor
discussed above to allow for a certain amount of wear
in the brake before you have to change it. The larger
the failure set point, the further back your guarding
equipment will have to be from the pinch point.
NOTE: Do not set the failure set-point so large
as to allow the press to stop at the top but slide
forward down to the pinch point. Your press control
should have a position-based monitor to prevent
that situation from occurring.
For example:
If you calculate a stop time of 140msec, but
your press varies a little and you want to allow for brake
wear so you use a failure stop time of 230msec. The
variance factor is then 90msec. The 230msec should be
used as your press stop time in calculating your safety
distance. Set your warning set point at some value below
230msec to let you know that you are approaching the
failure point ahead of time.
Input Signal.
The brake/clutch signal should be tied to
Input Terminals 17 and 18 of the I/O Board. For example,
if you are running a 120VAC system, run a line parallel
from the brake/clutch signal back to the PressCam 8.
There should be 120VAC across Input Terminals 17 and
18 when the brake is released.
See Drawing #28-105 for External Wiring Diagram in
this section.
Function Description
Содержание PressCam 8
Страница 1: ...PressCam 8 Installation Operations Manual ...
Страница 2: ...Rev 5 0 ...
Страница 14: ...6 Internal Wiring Diagram 28 101 System Installation ...
Страница 15: ...7 Control Box Dimensions 28 102 System Installation ...
Страница 16: ...8 Panel Cut Out Dimensions 28 103 System Installation ...
Страница 17: ...9 Control Panel Dimensions 28 104 System Installation ...
Страница 18: ...10 System Installation External Wiring Diagram 28 105 ...
Страница 19: ...11 System Installation I O Board Dimensions 28 106 ...
Страница 44: ...36 Tonnage Load Monitor optional Installation T400 Installation ...