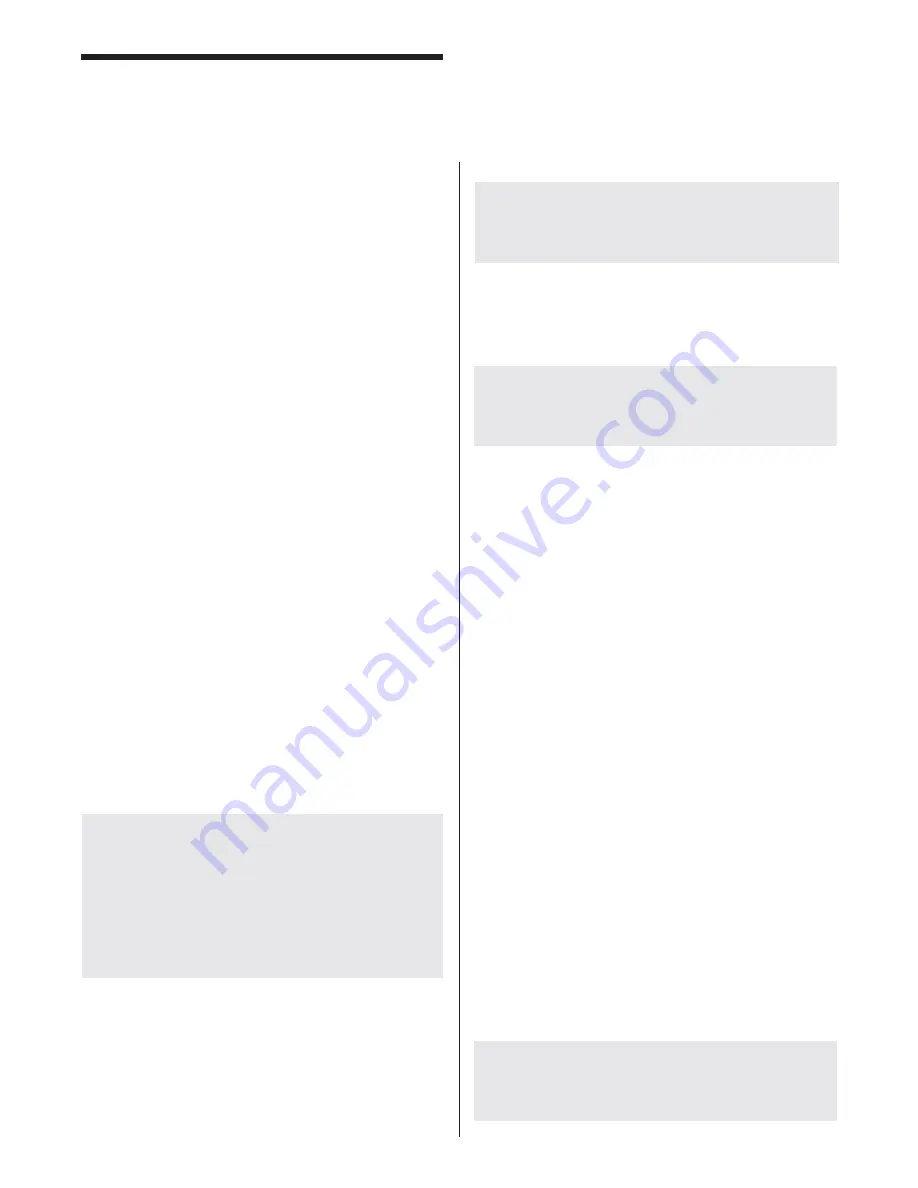
16
To program a die sensor, you must
fi
rst understand the
fi
ve types of sensor windows that we use.
1.
Momentary Inputs
- The die input must see a
change of state from the sensor somewhere within
the programmed window. The change can be open
to closed or closed to open and may occur multiple
times within the same window. No change of state
within the window will cause the PressCam 8 to
fault.
2.
Maintain N.O. Inputs
- The die input must not
see a change of state from the sensor from the
beginning of the window through the end of the
window. The signal must also be open. If a signal
is received from the sensor while in the window,
the PressCam 8 will fault.
3.
Maintain N.C. Inputs
- The die input must not
see a change of state from the sensor from the
beginning of the window through the end of the
window. This signal must also be closed. If no
signal is received from the sensor while in the
window, the PressCam 8 will fault.
4.
Static N.O. Inputs
- This type of input is typically
used for Buckle Detection. Being static means
that it should never see a signal from the sensor
anytime. If a signal is seen, the PressCam 8 will
fault. This type of input works 360° of the press
rotation.
5.
Static N.C. Inputs
- This type of input is typically
used for End of Stock detection. Being static
means that it should see a signal from the sensor
at all times. If a signal is not seen, the PressCam
8 will fault. This type of input works 360° of the
press rotation.
NOTE: Because a “Maintained” die input does
not check outside its window, you may wish to
run the same die sensor to a second die input
and set it to check either for a “Momentary” or for
an opposite “Maintained” state during some other
portion of the cycle (i.e., Die #1 Maintained N.C.
180 to 270, Die #2 Maintained N.O. 50 to 120,
both Die #1 and #2 inputs tied together).
How to Program a Die Input
NOTE: The Screen does not update if you are
currently changing a Begin or End angle. New
or changed information is stored in nonvolatile
memory as soon as the entire value is entered.
The status of all sensor inputs is indicated in the upper
right-hand corner of the display. An asterisk beside a
die input indicates that the input is receiving a signal
from the sensor.
NOTE: When in PROG mode, all die-input sensors
are active and working, however, the press will not
stop due to a die fault. All input faults are bypassed
in the PROG mode.
To program a Die Input, ensure that the unit is in PROG
mode.
With the unit in PROG mode,
1. Highlight the Die Input Sensor you want to
program.
2. Press the Knob to highlight the Sensor “TYPE.”
3. If you wish to select a different “TYPE,” press the
Knob again then rotate the Knob to select.
4.Rotate the knob over to TS and select the die fault
stop type (see paragraph below)
5. Rotate the Knob over to the Begin / End
fi
elds and
program in an angle (not used by Static types).
You must move the cursor back to the Sensor Name
fi
eld in order to update the memory with the new sensor
values.
How To Turn Off a Die Input:
Select Momentary and
0° for both open/close angles.
Die Fault TS type:
Select whether you want a Die
input sensor fault to E-Stop (select E) or Top Stop
(select T) the machine. Use the “Enter” key to toggle
between E or T modes. The Default is to E-Stop the
machine, but you may have a need to
fi
nish the cur-
rent cycle should a particular die input fault out. (i.e.
The parts counter Die #7)
WARNING:
The Top Stop / E-Stop feature is only
available on 31-053R7 boards running Software Ver
3.0 or better. Earlier boards/software only E-Stop
on Die Faults.
Function Description
Содержание PressCam 8
Страница 1: ...PressCam 8 Installation Operations Manual ...
Страница 2: ...Rev 5 0 ...
Страница 14: ...6 Internal Wiring Diagram 28 101 System Installation ...
Страница 15: ...7 Control Box Dimensions 28 102 System Installation ...
Страница 16: ...8 Panel Cut Out Dimensions 28 103 System Installation ...
Страница 17: ...9 Control Panel Dimensions 28 104 System Installation ...
Страница 18: ...10 System Installation External Wiring Diagram 28 105 ...
Страница 19: ...11 System Installation I O Board Dimensions 28 106 ...
Страница 44: ...36 Tonnage Load Monitor optional Installation T400 Installation ...