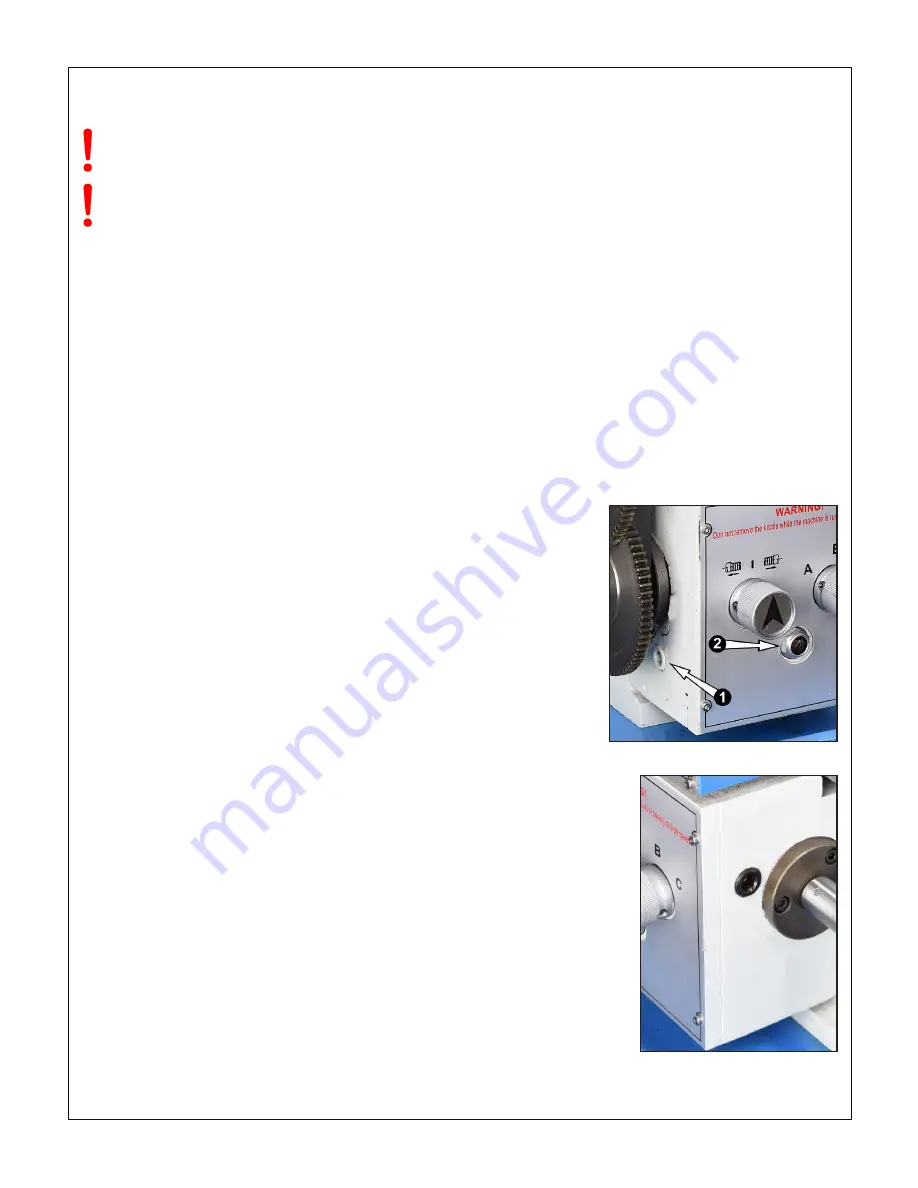
20
PM-1030V v5 2020-10
Copyright © 2020 Quality Machine Tools, LLC
Section 4 SERVICING THE LATHE
Disconnect power before any maintenance operation!
Remove all machining debris and foreign objects before lubricating ANYTHING! Use the
recommended lubricants or similar. Any oil is better than no oil – but only as a stop gap.
LUBRICATION — GEARBOX DRAIN & REFILL
Take time to prepare. A pint of oil is a lot to clean up!
GENERAL
Aside from abrasive particles and machining debris, lack of
proper lubrication is the main cause of premature wear. Ro-
tating parts are easy to lubricate, sliding parts are not. Gibs
are tightened for the best compromise between rigidity and
slideability, which means practically zero gap between the
ways. It is not obvious which are the bearing surfaces on the
various dovetail surfaces — some of the interfaces look like
bearing surfaces, but are simply narrow gaps.
Every few hours of operation: 1. Apply the recommended way-
oil with a dedicated short-bristle brush such as the type used
for applying flux; 2. Use a similar brush to apply oil or grease to
the leadscrews; 3. Apply oil to the ball oilers, see below.
The spindle runs on sealed, pre-lubricated roller bearings re-
quiring no routine attention.
Recommended lubricants
Gearboxes:
75W80 gear oil. Approximate quantities required:
Gearbox
1 pint
Apron
1 pint
Ball oilers
: ISO 68 way oil, such as Mobil Vactra No. 2, or
equivalent.
Machine ways
(dovetails): ISO 68 way oil, such as Mobil
Vactra No. 2, or equivalent.
External change gears
: light general purpose grease, NLGI
No. 2, or equivalent.
Leadscrews
: ISO 68 way oil, such as Mobil Vactra No. 2, or
equivalent.
BALL OILERS
Use a pump-type oil can, pr
eferably with a flexible spout tipped
with a soft tube. The ID of the tip should be large enough
to seat on the oiler's brass flange, more than spanning the
spring-loaded steel ball. When the oil can tip is firmly pressed
onto the brass surface oil pressure must displace the ball, al-
lowing oil to flow into the bearing. Before oiling check that the
ball is not stuck – press it lightly with a probe.
Figure 4-2
Gearbox fill plug
Figure 4-1
Gearbox drain plug (1) & sight glass (2)
1. Run the lathe for a few minutes to warm the oil if neces-
sary.
2.
Remove the fill plug on the top surface of the headstock,
Figure 4-2.
3. Remove the external change gears if necessary for ac-
cess to the drain plug, Figure 4-1.
4. Place a drain pan under the drain plug.
5. Fold a sheet of card stock to make a Vee-shape drain
channel. Trim the Vee to seal against the gearbox.
6. With the drain channel in place, remove the drain plug.
7. Allow the oil to drain completely, then replace the drain
plug.
8. Attach a short length of 3/8" OD clear PVC tubing to a
small funnel.
9.
Insert the tube into the fill hole, then add just an ounce or
two of oil.
10.
When satisfied that the gearbox is oil-tight, add oil to the
halfway mark on the sight glass (about 1 pint).
11.
Replace the fill plug.