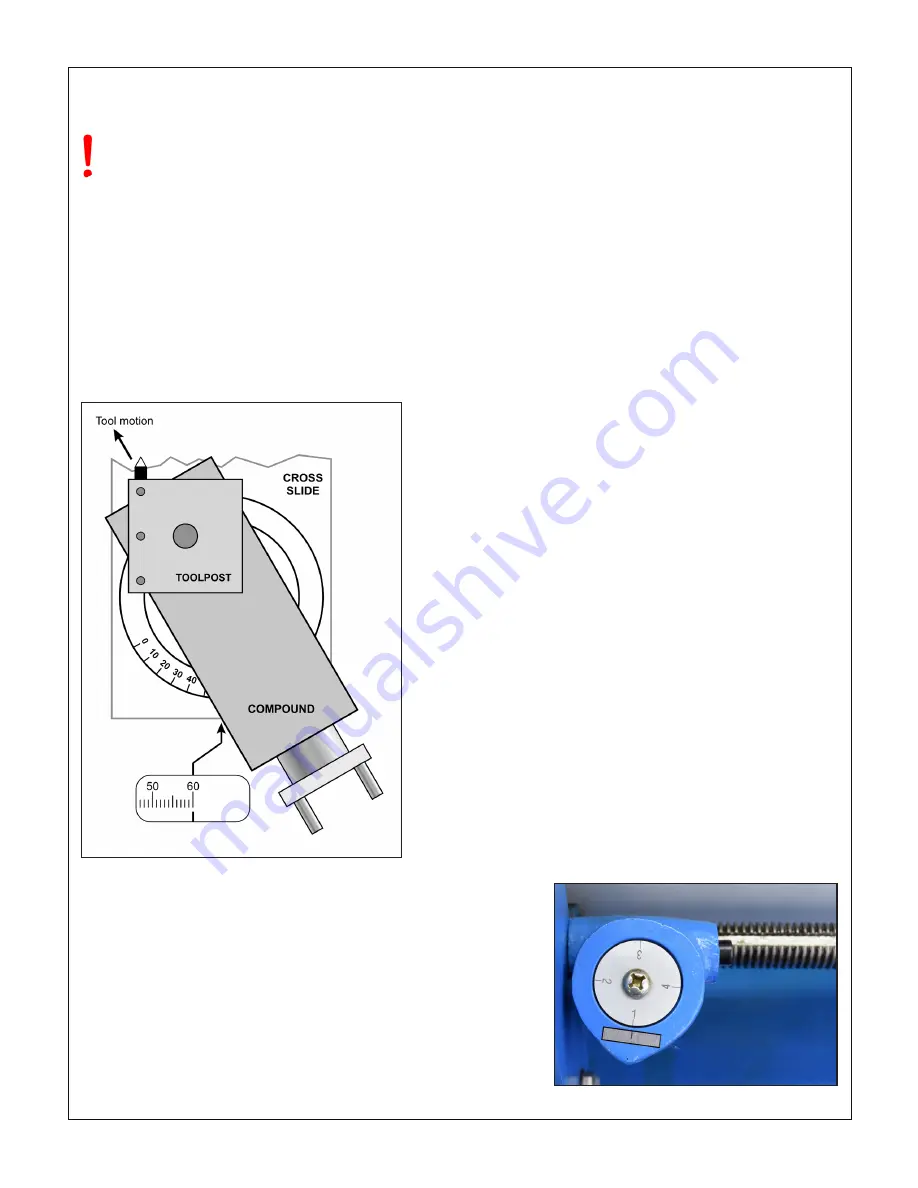
17
PM-1030V v5 2020-10
Copyright © 2020 Quality Machine Tools, LLC
COMPOUND SETUP FOR THREAD CUTTING
Thread cutting on the lathe is unlike most other turning oper-
ations, for two reasons: 1. The cutting tool must be precisely
ground with an included angle of 60 degrees for most Amer-
ican and metric threads, and; 2. It is preferable to feed the
tool into the workpiece at an angle so it cuts mostly on the left
flank of the thread, Figure 3-18. The correct angle relative to
the cross-slide (zero degrees) is debatable — should it be 29,
29-1/2 or 30 degrees? Many machinists prefer 29 degrees be-
cause it holds the cutting tool marginally clear of the right flank
of the thread, close enough for cleanup of the flank while at the
same time avoiding appreciable rubbing.
Figure 3-23
Setting the compound for 30
o
infeed
THREAD CUTTING
A key fact to remember ...
For metric threads the half-nut in the apron must
remain engaged throughout the entire process.
CUTTING PROCEDURE FOR TPI THREADS
This procedure assumes that a single point thread cutting tool
will be used, and that the worm wheel on the threading dial
assembly properly engages the leadscrew, Figure 3-x.
The threading dial cannot used for metric threads! The
split-nut on the apron must not be disengaged until the
threading operation is completed.
For metric and UNC/UNF threads the tool is ground to 60
o
(in-
cluded angle). It is installed so that its flanks are exactly 30
o
either side of the cross axis, ideally with the compound offset
as Figure 3-23. Single-point threads are cut in as many as
10 successive passes, sometimes more, each shaving a little
more material off the workpiece.
To make the first thread-cutting pass the leadscrew is run at
the selected setting (tables on following two pages), and the
saddle is moved by hand to set the cutting tool at the start-
ing point of the thread. With the tool just grazing the work-
piece, the half-nut lever (Figure 3-19) is lowered to engage
the leadscrew. This can be done at any point,
provided
the
split-nut remains engaged throughout the
entire multi-pass
thread cutting process
.
When the first pass is completed, the tool is backed out clear
the workpiece (using the cross-slide), and the spindle is re-
versed to bring the saddle back to the starting point. The cross-
slide is returned to its former setting, then the tool is advanced
a few thousandths by the compound for the next pass. Each
successive pass is done in the same way, each with a slightly
increased infeed setting of the compound.
Many users working on U.S. threads save time by disengaging
the split-nut at the end of each cutting pass, reversing the sad-
dle quickly by hand, then re-engaging, usually by reference to
the threading dial, Figure 3-24.
For most TPI numbers every engagement,
including the first
,
must at the point where a
specific
line
on the threading dial
comes into alignment with the datum mark. If not, the second
and subsequent passes will be out of sync. In some cases,
see the “visualization” Figure 3-26, there is a choice of lines for
re-engagement, but in every case the process calls for careful
timing.
[NOTE: Disengagement and re-engagement of the split-
nut is not applicable to metric threads — leave the split-
nut engaged throughout the entire process]
Typical depths of cut per pass vary from an initial 0.005” or so,
to as little as 0.001”, even less. A finishing pass or two with
increments of only 0.0005” — or none at all, to deal with the
spring-back effect, can make all the difference between a too-
tight thread and one that runs perfectly.
Assuming that the compound is set over at between 29 and
30 degrees, the total depth of cut is approximately 0.69 times
the thread pitch, P (this equates to a straight-in thread depth of
0.6 times P). There may be a need for a few thousandths more
in-feed than 0.69P, almost certainly not less.
Figure 3-25
Threading dial (US threads only)