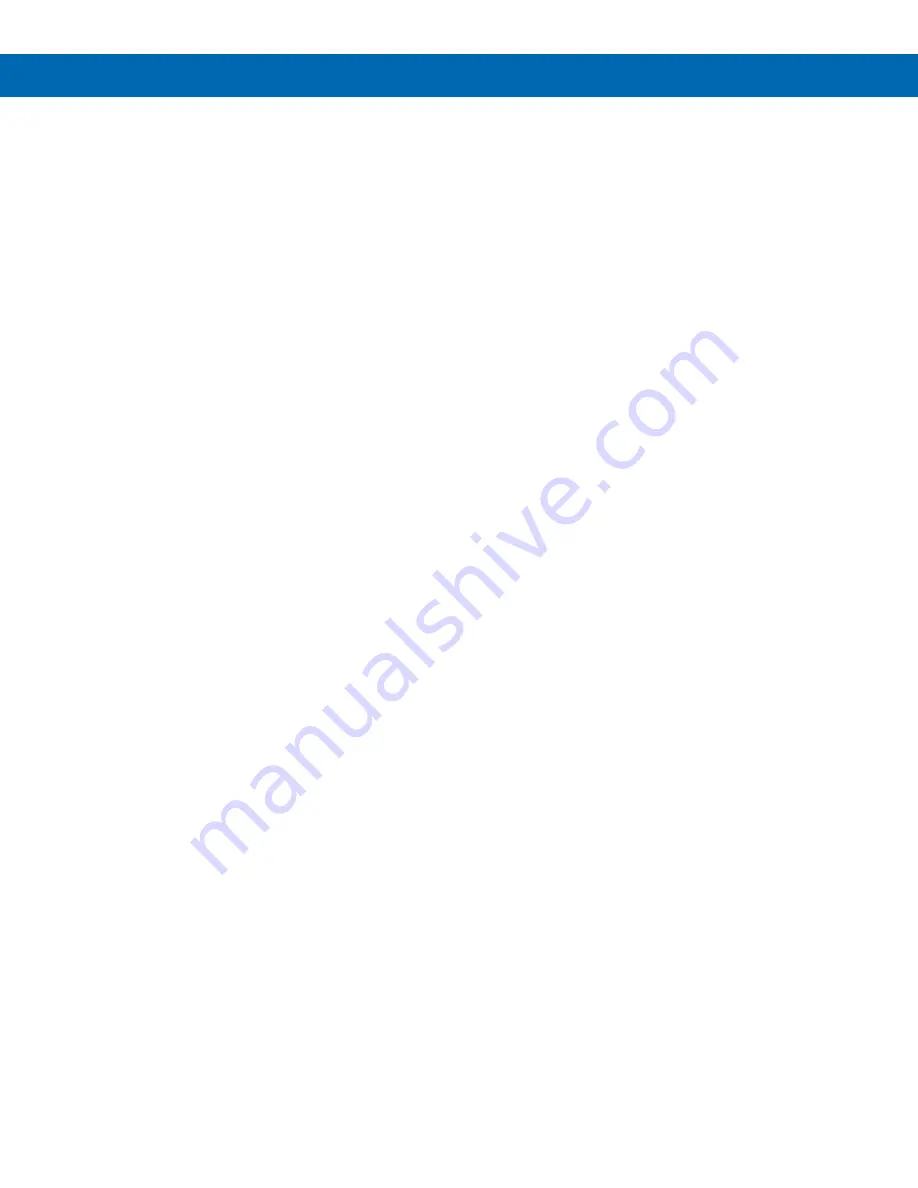
SuperNova PD500 PID Process & Temperature Controllers
Instruction Manual
6
Introduction
The SuperNova PD500 Series of PID Process & Temperature Controllers is a complete line of PID and on/off
controllers. Available in popular 1/4, 1/8, and 1/16 DIN sizes, and with a shallow depth behind panel of only 2.5"
(63 mm) it is easy to fit into almost any panel, product, or enclosure.
Voltage, current (with external resistor), and direct temperature thermocouple and RTD inputs make it an excellent
choice for any control application requiring easy to change, visible set points.
This modern line of controllers shows the process variable (PV), set value (SV), and manipulated value (output
level%, MV) on a striking reverse polarity LCD screen. Indicators for units (
˚
C,
˚
F,%, or none)
Auto and manual control modes can be easily changed by holding two buttons, and this is indicated on the front panel
to make it easy for operators to know how to use this feature.
Main control outputs can be 4-20 mA (SCR), voltage pulse (SSR), or relay outputs. A secondary relay control output
is standard, which allow for one or two direction SV control (
i.e.,
heating and cooling).
Additional outputs may include two SPST alarm relays and a 4-20 mA retransmit output. Other options include a
secondary 4-20 mA input to remotely control the set point, and RS-485 for Modbus communication.
A mini-USB port may be used for a direct PC connection to run the SuperNova software for monitoring, programming,
and data logging. This USB port is located on the rear behind the panel for PD510 1/16 DIN models, and on the front
behind a rubber tab on PD520 and PD530 1/8 and 1/4 DIN models.
Abbreviations
The following abbreviations are used throughout this manual.
General Controller Term Descriptions
Abbreviation
Full Meaning
PV
Process value
SV
Set value
MV
Manipulated value (Output value %)
AT
Auto-tuning
REM
Remote set value
RET
Retransmission 4-20 mA output
SUB1
SUB1 output (alarm relay 1)
SUB2
SUB2 output (alarm relay 2)
LBA
Loop break alarm
EU
Engineering unit
EUS
Engineering unit, total span
Range and Scale Descriptions
FR.L
Full Range Low: The temperature range is defined according to the thermocouple or RTD type selected.
The minimum temperature value of this range is referred to as the FR.L (full range, low).
Example: For a type K thermocouple, the FR.L is -200 °C.
FR.H
Full Range High: The temperature range is defined according to the thermocouple or RTD type
selected. The maximum temperature value of this range is referred to as the FR.H (full range, high).
Example: For a type K thermocouple, the FR.H is 1370 °C.
SL.L
Scale Limit Low: The scale range is used when the input is a process signal, voltage or current (with an
external sense resistor). The minimum scale value of the process input is referred to as the SL.L. This
value may be changed with the SL-L parameter to scale the process input to the desired engineering
unit.
Example: For a 1 to 5 VDC input, the default SL.L is -1999. To represent an input value of 0 to 100%,
the SL-L parameter would be changed to 0, making the SL.L 0.
SL.H
Scale Limit High: The scale range is used when the input is a process signal, a voltage or current (with
an external sense resistor). The maximum scale value of the process input is referred to as the SL.H.
This value may be changed with the SL-H parameter to scale the process input to the desired
engineering unit.
Example: For a 1 to 5 VDC input, the default SL.H is 9999. To represent an input value of 0 to 100%,
the SL-H parameter would be changed to 100, making the SL.H 100.