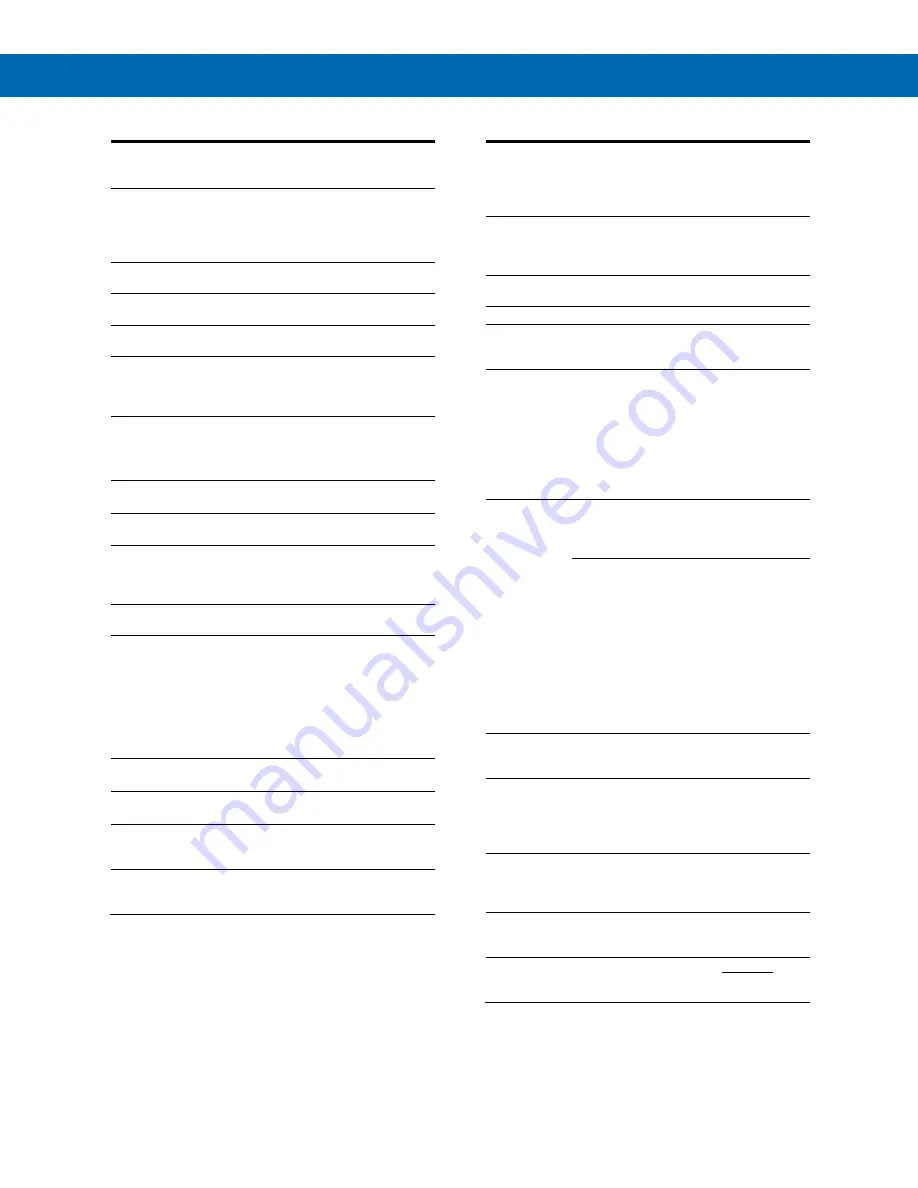
P
RO
V
U
™ PD6402 High Voltage & mV to Current Meter
Instruction Manual
9
High Voltage & mV Inputs
High Voltage
Input
One high voltage input (Channel V) 0-300 VDC
or VAC; Switch Selectable, Modbus PV
(Slave)
mV Input
One mV input (Channel A) 0-150 mV;
Switch Selectable, Modbus PV (Slave)
Factory Default: 0-100 mV input
corresponds to 0.000 to 0.100 display. User
may scale for different ranges.
Channels
Channel A, Channel V, Channel P (Math
Channel for Apparent Power)
AC/DC
Selection
Switch selectable for AC or DC inputs.
Channels A and V share AC/DC selection.
Apparent
Power Math
Apparent power P calculated as
P = ((A * V) + C) * F
Programmable
Constants
Constant C (Adder): -99.999 to 999.999,
default: 0.000
Constant F (Factor): 0.001 to 999.999,
default: 1.000
Accuracy
mV DC: 0.03% Full Scale ±1 count,
mV AC: 0.1% Full Scale ±1 count,
VDC: 0.05% Full Scale ±1 count,
VAC: 0.15% Full Scale ±1 count
Temperature
Drift
0.005% of calibrated span/
C max from
-40 to 65
C ambient
Multi-Point
Linearization
2 to 32 points for Channel A and V
Low-Value
Cutoff
0.1 to 999,999 (0 disables cutoff function).
Point below at which the display always
shows zero. Independent for Channel A
and V.
Decimal Point
Up to five decimal places or none:
d.ddddd
,
d.dddd
,
d.ddd
,
d.dd
,
d.d
, or
dddddd
Calibration
Range
Input
Channel
Input Range
Minimum Span
Input 1 & Input 2
A
± 0-150 mV DC
0-150 mV AC
± 0.5 mV DC
1 mV AC
V
± 0-300 VDC
0-300 VAC
± 0.1 VDC
0.3 VAC
An error message will appear if the input 1
and input 2 signals are too close together.
Input
Impedance
Voltage Input: Greater than 3 M
Current Input: 50 - 100
Input
Overload
Voltage input protected up to 500 VDC
mV current input protected up to 10 VDC
F4 Digital
Input
Contacts
3.3 VDC on contact. Connect normally
open contacts across F4 to COM.
F4 Digital
Input
Logic Levels
Logic High: 3 to 5 VDC
Logic Low: 0 to 1.25 VDC
Relays
Rating
2 or 4 SPDT (Form C) internal and/or
4 SPST (Form A) external; rated 3 A
@ 30 VDC and 125/250 VAC resistive
load; 1/14 HP (
≈
50 W) @ 125/250 VAC for
inductive loads
Noise
Suppression
Noise suppression is recommended for
each relay contact switching inductive
loads; see
Loads on
Relay
Assignment
Each relay independently assigned to
Ch-A, Ch-V, CH-P, or Modbus
input
Deadband
0-100% of span, user programmable
High or Low
Alarm
User may program any alarm for high or
low trip point. Unused alarm LEDs and
relays may be disabled (turn off).
Relay
Operation
•
Automatic (non-latching) and/or
manual reset
•
Latching (requires manual
acknowledge) with or without clear
•
Pump alternation control (2-8 relays)
•
Sampling (based on set point and time)
•
Off (disable unused relays and enable
Interlock feature)
•
Manual on/off control mode
Relay Reset
User selectable via front panel button, F4
terminal at back of meter, external contact
closure on digital inputs, or through serial
communications.
1.
Automatic reset only (non-latching),
when the input passes the reset point.
2.
Aut manual reset at any time
(non-latching)
3.
Manual reset only, at any time
(latching)
4.
Manual reset only after alarm condition
has cleared (L)
Note: Front panel button, F4 terminal at
back of meter or digital input may be
assigned to acknowledge relays
programmed for manual reset.
Time Delay
0 to 999.9 seconds, on & off relay time
delays. Programmable and independent for
each relay
Fail-Safe
Operation
Programmable and independent for each
relay.
Note: Relay coil is energized in non-alarm
condition. In case of power failure, relay will
go to alarm state.
Break
Condition
Operation
Relay condition when sensor break
detected. Programmable independently for
each relay as On, Off, or Ignore (maintain
last condition).
Auto
Initialization
When power is applied to the meter, relays
will reflect the state of the input to the
meter.
Additional
Relays
An external module, model PDA1004, is
available to add 4 SPST 3 A relays to the
meter.