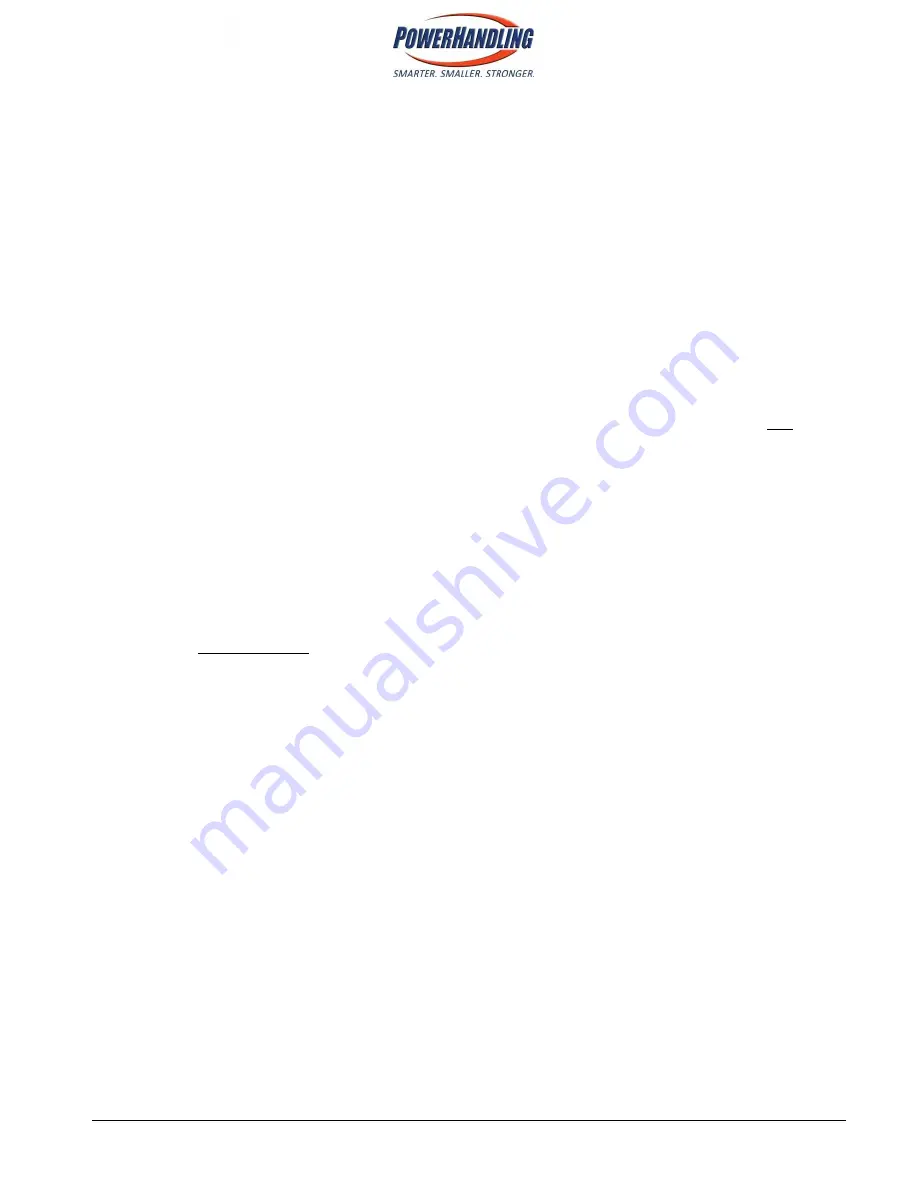
2. GRIP - The drive roller spins against the load instead of moving it
This is typically because of insufficient traction between the drive roller and the load being moved and
can occur for a number of reasons, including:
I.
On a brand new machine, there can be a problem with initial grip until the drive roller becomes
“worn in”. This is a temporary condition that can be reme
died quickly. The best way to wear in
the drive roller is to use it. It is important you wear in the roller on product that does not cause
slip
–
usually larger diameter loads. Using it on rolls or other product that does slip will heat up
the urethane surface due to friction and exacerbate the grip problem. After 10 minutes of
rolling a load back and forth it should be worn in enough to move loads without slipping.
II.
The geometry may be accentuating an existing traction problem. Reference the explanation in
the ‘General Overview’ section describing how too small of a diameter load results in less of the
inertial resistance of the load pushing downward (vertical) instead of backward (horizontal). A
small diameter can be moved if there is sufficient friction contact and a large diameter load can
be moved even with very little friction contact, but the combination of a small diameter
and
low
friction greatly increases the likelihood of slipping.
Generally, the load’s diameter should be
> 915mm (36
”).
III.
The drive roller has oil, grease or other low viscosity material embedded into or otherwise
making contact with it, reducing its ability to achieve a friction contact. As the drive roller makes
pressure contact with the support roller while the machine is operating, oil and/or grease may
be picked up from the floor and deposited onto the drive roller in which case the rollers will
need to be cleaned with an appropriate oil dissolving solvent or detergent.
IV.
To address low friction issues and reduce the impact of lubricants that end up interfering with
the rollers, the application of Borax (Hydrated Sodium borate
–
an inexpensive cleaning agent,
ref www.borax.com) to the drive roller can help. All new PowerRolls and replacement drive
rollers are sent out with Borax already applied.
Battery Pack Discharges Quickly
I.
If the current battery pack has been in service for quite some time, its effective capacity may be
depleted. All current battery technologies are such they lose a percentage of their total
effective capacity on each discharge/recharge cycle. In time, this reaches a point that the
battery pack’s life becomes
too short and it should be replaced. If two battery packs are being
used equally, this should result in both battery packs becoming ineffective around the same
time. If one pack is wearing out prematurely though, return the suspect pack to PowerHandling
for analysis.
II.
If the battery pack is relatively new and has undergone few discharge/recharge cycles, it is
possible it is a faulty battery pack. If this is the case, there will likely be problems during both the
charging and discharging of the battery pack. Contact your PowerHandling sales representative.
17 of 20
2020/
10