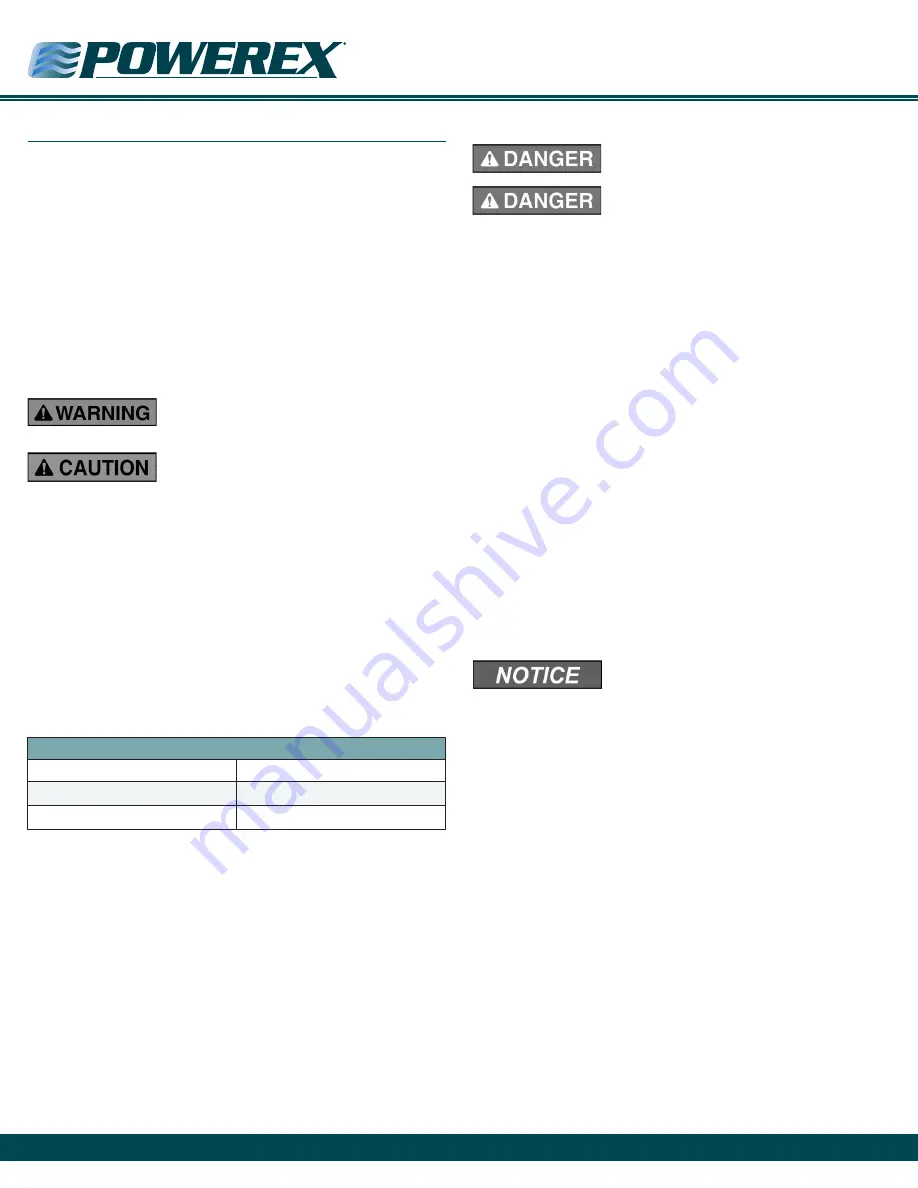
Scroll Medical & Laboratory Compressed Air Systems
Powerex
•
150 Production Drive
•
Harrison, OH 45030
•
USA
P 1.888.769.7979
•
F 513.367.3125
•
www.powerexinc.com
IN907800AV
•
08/2018
Page 4 of 40
Wiring
Lock out and tag out the electrical supply before
servicing the equipment.
requirements.
Electrical shock hazard. Make sure the system
is grounded in accordance with NEC and local
All electrical hook-ups must be performed by a qualified electrician.
Installations must be in accordance with local and national electric
codes. Make sure power supply conductors are sized adequately for
full system demand.
Use solder-less terminals to connect the electrical power source.
Piping
General Guidelines
Refer to the general product manual.
1.
Make sure the piping is lined up without being strained or
twisted when assembling the piping for the system.
2.
Appropriate expansion loops or bends should be installed at
the system to avoid stresses caused by changes in hot and cold
conditions.
3.
Piping supports should be anchored separately from the
system to reduce noise and vibration.
4.
Never use any piping smaller than the system outlet connection.
5. Use flexible hose to connect the outlet of the system to the
piping so that the vibration of the system does not transfer to
the piping.
water going into the pumps will damage the pumps and void the warranty.
The intake filters supplied by Powerex will not
stop ingestion of liquid water by the pumps. Liquid
Remote Intake Piping
Use a flexible connector to join the facility piping to the system
single point intake.
Size the remote intake piping to minimize pressure loss due to flow
friction. Use the following guidelines to determine the minimum pipe
size. Larger size piping will reduce losses.
A compressor system intake must be located to comply with
applicable regulations and should be arranged to provide the cleanest
air possible for compression. Follow all requirements of NFPA 99 for
location and materials.
In addition, the inlet system must be designed to avoid pressure
drop or creating a significant vacuum on the intake side of the pumps
and to avoid any condensation formed by cooling of humid intake
air from reaching the pumps. A drip leg, or multiple drip legs may
be necessary. Drain the drip legs frequently to prevent water from
reaching the pumps. Water will damage the pump and void the
warranty.
To determine the minimum required pipe size for a compressor
system intake, calculate the equivalent straight length of the run.
Installation
Frames or Tank Mount Structure
Powerex designed the system to bear the weight and stress of
the compressor pumps, controls, and receiver tank. When lifting
the system, use the designated fork lift slots or rig straps to lift the
main system skid. Do not attempt to lift the system using individual
component lifting hooks and eyes. Piping may need to be supported
to avoid damaging the supplied flex connectors for intake and exhaust.
Operation at High Altitudes
Compressor pumps are sensitive to reduced atmospheric pressure
encountered as altitude increases. Powerex will adjust the operating
set points to compensate for altitude if the original order is designated
for high altitude and the expected conditions provided to us.
Disconnect, tag and lockout power before
attempting to install, service, relocate or perform
any maintenance.
Do not lift or move unit without appropriately rated
equipment. Be sure the unit is securely attached to
lifting device used. Do not lift unit by holding onto tubes or coolers. Do not
use pumps to lift other attached equipment.
Installation Site
1.
The compressor system must be located in a clean, well lit and
well-ventilated area.
2.
The area should be free of excessive dust, toxic or flammable
gases and moisture.
3. Never install the system where the surrounding temperature is
higher than 104°F or where humidity is high.
4.
Clearance must allow for safe, effective inspection and
maintenance.
MINIMUM CLEARANCES
Above
24 inches
Other sides
24 inches
Control Panel side
36 inches
5. If necessary, use metal shims or leveling pads to level the
system. Never use wood to shim the unit.
Ventilation
1.
If the oil-less compressor system is located in a totally enclosed
room, an exhaust fan with access to outside air make up air
must be installed. Room temperature must remain below
104°F. Circulation must be sufficient to prevent local hot spots.
2. Never restrict the cooling fan exhaust air. Maintain a minimum
of 24 in. of clearance around the entire unit (36 in. is preferred).
3. Never locate the compressor where hot exhaust air from other
heat generating units may be pulled into the system.