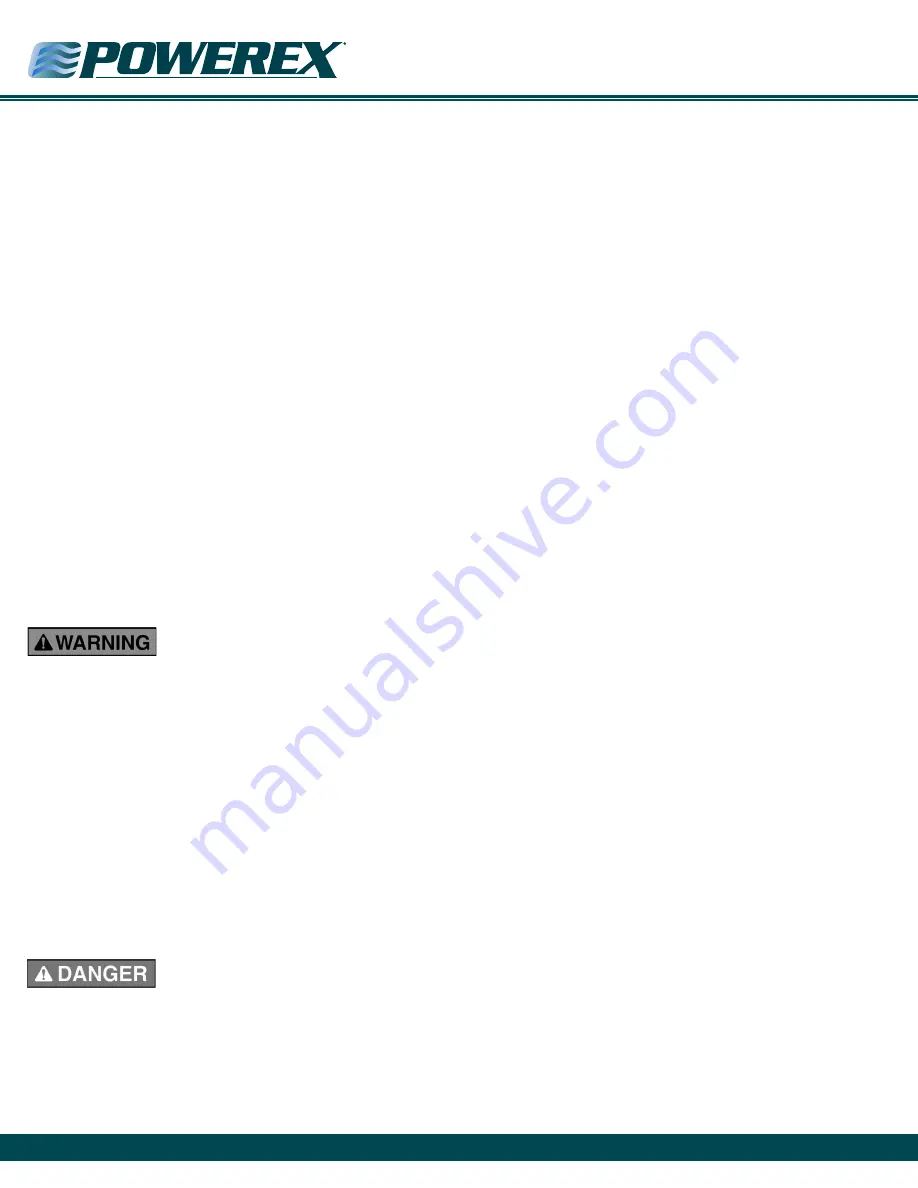
Scroll Medical & Laboratory Compressed Air Systems
Powerex
•
150 Production Drive
•
Harrison, OH 45030
•
USA
P 1.888.769.7979
•
F 513.367.3125
•
www.powerexinc.com
IN907800AV
•
08/2018
Page 3 of 40
The compressed air is then carried to the after cooler. During after
cooling, condensation is formed and captured in the condensate trap
downstream from the after cooler. The condensate trap collection
bowl is piped to an automatic drain system. The liquid formed is
condensed atmospheric water vapor and it may be allowable to
drain into your local sewer system. Check local regulations for actual
requirements.
The compressor pumps are driven by three phase electric motors
acting through vee belt drives. The belts are carefully engineered
and selected for durability and reliability. When the vee belts run,
especially in the first few hundered hours of operation, dust is
generated as the profile of the belt wears in to match the grooves in
the drive and driven sheaves. The dust is normal and will not cause
any operating problems. If the belts are not slipping, no adjustement
of tension is necessary. If tension adjustement or belt replacement
does become necessary, the motor mount is designed to act as a slide
base tensioning systems and detailed instructions are provided in this
manual.
After the condensate trap, a check valve and a ball valve is installed
in each branch of the compressor system. This valve allows an unused
branch to be closed off from the system. If the valve is utilized to allow
service to be performed, a locking cover must be installed to meet
Lock out Tag out requirements. A relief valve is installed upstream
of the ball valve, so that if the ball valve is closed and the pump is
started, the relief valve will open and prevent catastrophic pressure
rise and damage. The relief valve is not intended to allow continuous
operation of the pump with the ball valve closed.
Compressed air systems contain electrical energy.
Remove and lock out all energy sources from the
system if any maintenance is being performed where the energy may
cause the pump or motor to operate.
Compressed air is collected and piped to the air receiver. The air
receiver has a bypass valve manifold installed for use if necessary. The
air receiver has an anti-corrosion lining. Each air receiver has an ASME
safety relief valve to prevent system pressure from exceeding the
design capability of the vessel. A mechanical pressure gauge allows
visual verification of the system pressure. Condensation that forms
after the after cooler will collect in the receiver. An automatic tank
drain is installed along with a manual drain valve to remove the liquid.
Since the compressors are oilless, the liquid formed is condensed
atmospheric water vapor and it may be allowable to drain into your
local sewer system. Check local regulations for actual requirements.
A transparent tube is installed in the lower section of the air receiver
to allow visual verification that the condensate is being removed from
the vessel.
Risk of Injury or death. Do not modify the air
receiver or the ASME safety relief valve. Do not
obstruct or restrict the outlet of the ASME safety relief valve. Do not
operate the system at pressures higher than the rated pressure. Do not
perform any work on the receiver or connected components while energy
(compressed air) is present.
Compressed air from the receiver is routed to the dryer section
where duplex desiccant dryers remove water vapor to the specified
dew point of the system. A desiccant dryer uses chemical reactions
with water vapor and the surface of the desiccant material to hold
water molecules when compressed air is flowing through the bed.
The bed is then regenerated using some of the dry air in the “purge”
mode at low pressure to reverse the chemical reaction. The dryer
controls automatically cycle the beds to extract moisture from the
compressed air. Each branch of the duplex desiccant dryer system is
equipped with isolation valves so that one dryer can be online and
in use while the other is idle. Each branch has filters and pressure
regulators as needed. Dryer inlet filtration includes mechanical
cyclonic water droplet separation as well as coalescing filters. Dryer
outlet filtration prevents any desiccant dust from leaving the system.
After the dryers, the compressed air is connected to dew point and
CO monitors. (CO monitor is optional for laboratory systems). The
monitors take a small amount of sample air. The dew point monitor
works with the dryer controls to minimize the amount of purge air
used to regenerate the desiccant beds. The Dew Point and CO monitor
go into alarm mode if allowable parameters are exceeded.
Controls
The disconnects and protection devices in the Powerex control
system are for the motor branch circuits, accessory supply circuits and
for the control circuit only. The controls on the Powerex Laboratory
Open Scroll System do not include a service disconnect and circuit
protection for the supply circuit. Selection and installation of these
items must be provided in compliance to local and national codes in
accordance with each facility’s need.
The PLC automatically alternates the lead designation and brings
on lag pumps as needed, equalizing run time on the pumps in the
system. The touch screen HMI (Human Machine Interface) panel on
the front allows operation and monitoring of the system. The touch
screen provides the user with displays showing the operating status
and allows the user to access features of the control system. The
control panel also allows communication using the BACnet® protocol.
The control panel includes Hand-Off-Auto selector switches for
each pump so that a pump can be held on (or off). This can be useful
if maintenance or diagnostic procedures are being performed.
The transformer is sized for the loads imposed by the Powerex
factory controls and should not be utilized for any other purpose.
Premium control panels utilize a backup transformer with a reserve
transformer in use alarm.
Local alarms are provided for low pressure and general fault
conditions. The general fault alarm includes high temperature,
reserve transformer in use, motor overload and reserve pump in use
(when specified). The wiring connection point for the alarms is on the
terminal strip in the control panel box, with good conditions being
contacts closed. (If a wire connection is lost, the result is an alarm.)