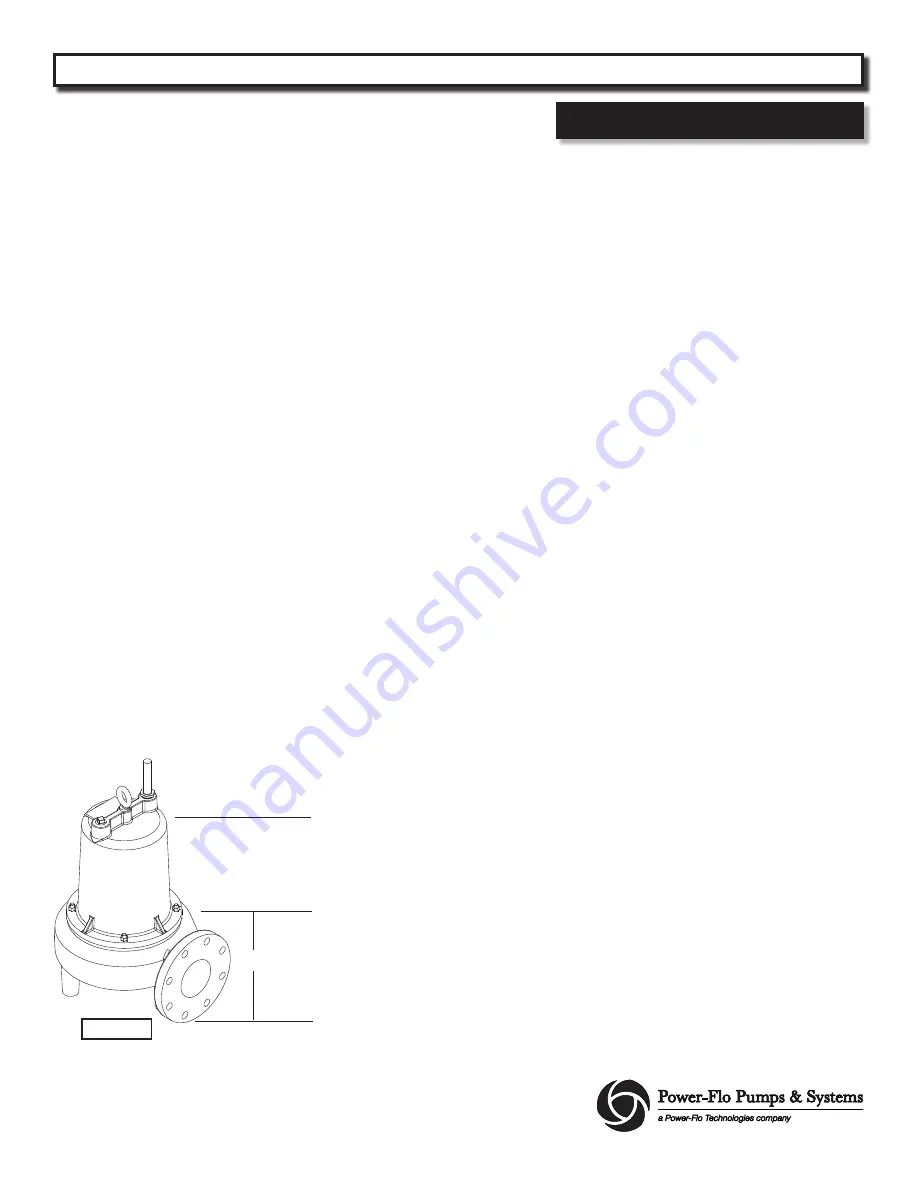
7
Power-Flo Pumps & Systems • 877-24PUMPS • www.powerflopumps.com
Receiving Inspection
Upon receiving the pump, it should be
inspected for damage or shortages.
If damage has occurred, file a claim
immediately with the company that
delivered the pump. If the manual is
removed from the packaging, do not
lose or misplace.
Storage
Any product that is stored for a period
longer than six (6) months from the
date of purchase should be bench
tested prior to installation. A bench
test consists of, checking the impeller
to assure it is free turning and a run
test to assure the motor (and switch
if provided) operate properly. Do not
pump out of liquid.
Controls
Manual models require a separate
approved pump control device or panel
for automatic operation. Be sure the
electrical specification of the control
selected properly match the electrical
specifications of the pump.
Submergence
The pump should always be operated in
the submerged condition. The minimum
sump liquid level should never be less than
above the pump’s volute (See Figure 1).
Installation
These pumps are recommended for
use in a sump, basin or lift station.
The sump, basin or lift station shall be
sealed and vented in accordance with
local plumbing codes.
This pump is
designed to pump sewage, effluent
or wastewater, nonexplosive and
noncorrosive liquids and shall NOT
be installed in locations classified as
hazardous in accordance with the
National Electrical Code (NEC) ANSI/
NFPA 70 or Canadian Electric Code
(CEC).
The pump should never be
installed in a trench, ditch, or hole with
a dirt bottom. The legs will sink into
the dirt and the suction will become
plugged.
The installation should be at a sufficient
depth to ensure that all plumbing is
below the frost line. If this is not feasible,
remove the check valve and size the
basin to accommodate the additional
backflow volume.
Pumps are most commonly installed
in simplex or duplex stations or basins
with a slide rail system, which allows
the pump(s) to be installed or removed
without requiring personnel to enter
the station, or resting on the basin floor.
Discharge Piping
Discharge piping should be as short
as possible and sized no smaller than
the pump discharge. Do not reduce
the discharge pipe size below that
which is provided on the pump. Both
a check valve and a shut-off valve are
recommended for each pump. The
check valve is used to prevent backflow
into the sump. The shut-off valve is
used to manually stop system flow
during pump servicing.
Liquid Level Controls
The level control(s) should be mounted
on the discharge piping, a cable rack
or float pole. The level control should
have adequate clearance so it cannot
hang up in it’s swing and that the pump
is completely submerged when the
level control is in the “Off” mode. By
adjusting the cord tether the control
level can be changed. One cycle of
operation should be observed, so that any
potential problems can be corrected.
It is recommended that the level control
float should be set to insure that the liquid
in the sump never drops below the top of
the motor housing or a minimum level of
10 inches above the basin floor.
Electrical Connections
Power cable:
The power cable mounted to the pump
must not be modified in any way except
for shortening to a specific application.
Any splice between the pump and the
control panel must be made in
accordance with the electric codes. It is
recommended that a junction box, if used,
be mounted outside the sump or be of
at a minimum Nema 4 construction if
located within the wet well. DO NOT USE
THE POWER CABLE TO LIFT PUMP.
Always rely upon a Certified Electrician
for installation.
Overload Protection:
Single Phase - The stator in-winding
overload protector used is referred to
as an inherent overheating protector
and operates on the combined effect
of temperature and current. This means
that the overload protector will trip out
and shut the pump off if the windings
become too hot, or the load current
passing through them becomes too high.
Figure 1
Receiving & Installation
Recommended
Submergence Level
Minimum
Submergence Level
11”
Bottom of Feet
PF4NC-SS
Non-Clog Pumps
Содержание PF4NC2824SS Series
Страница 6: ...6 Power Flo Pumps Systems 877 24PUMPS www powerflopumps com Performance PF4NC SS Non Clog Pumps...
Страница 21: ...21 Power Flo Pumps Systems 877 24PUMPS www powerflopumps com Notes PF4NC SS Non Clog Pumps...
Страница 22: ...22 Power Flo Pumps Systems 877 24PUMPS www powerflopumps com Notes PF4NC SS Non Clog Pumps...