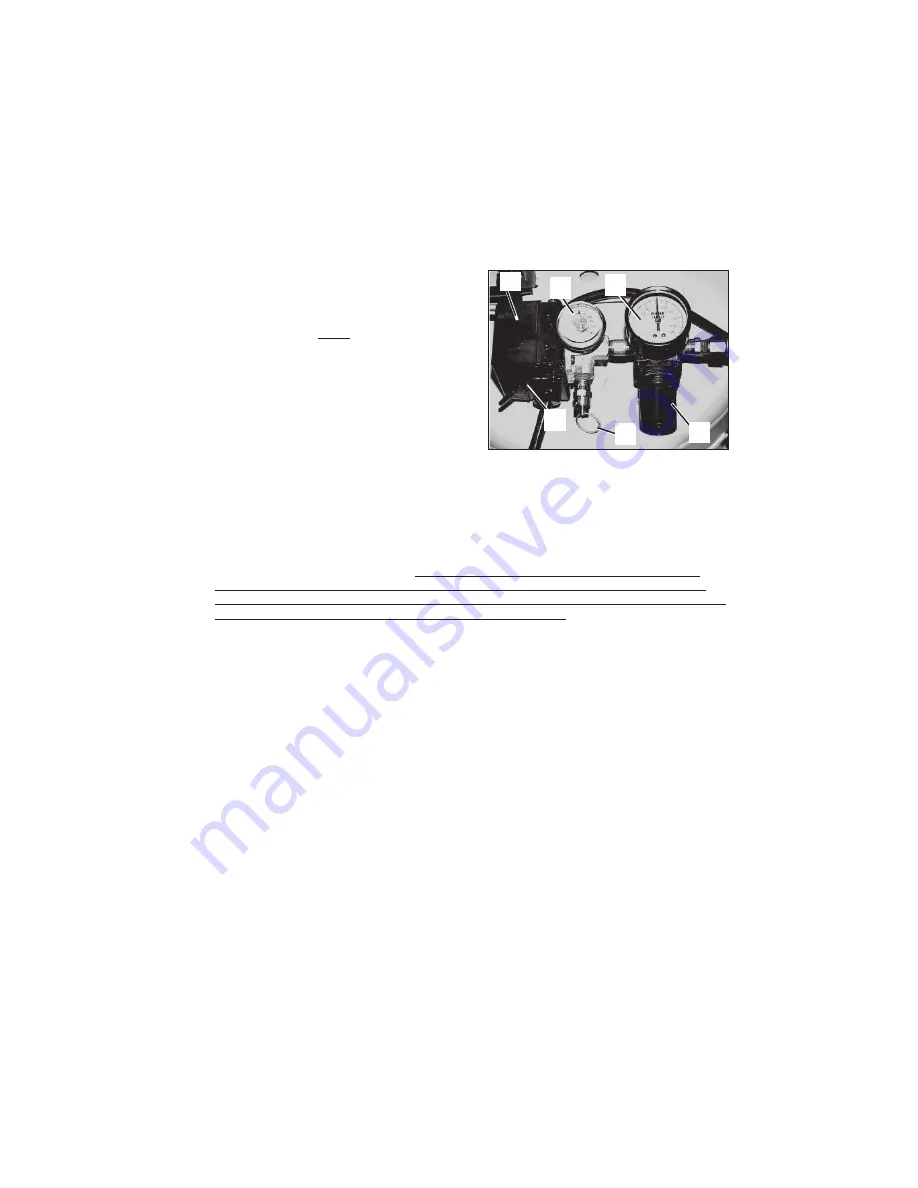
7-ENG
DESCRIPTION OF OPERATION
Drain Valve (not shown):
The drain valve is located at the base of the air tank and
is used to drain condensation at the end of each use.
Motor Thermal Overload Protector (not shown):
The electric motor has an
automatic thermal overload protector. If the motor overheats for any reason, the
thermal overload protector will shut off the motor. The motor must be allowed to
cool before restarting.
ON/AUTO - OFF Switch (A) Fig. 1:
Turn this switch ON to provide automatic
power to the pressure switch and OFF to remove power at the end of each use.
Air Intake Filter (not shown):
This filter is designed to clean air coming
into the
pump. This filter
must
always be clean and ventilation openings free from
obstructions. See "Maintenance".
Air Compressor Pump (not shown):
To compress air, the piston moves up and
down in the cylinder. On the downstroke, air is drawn in through the air intake
valves. The exhaust valve remains closed. On the upstroke of the piston, air is
compressed. The intake valves close and compressed air is forced out through the
exhaust valve, into the outlet tube, through the check valve and into the air tank.
Working air is not available until the compressor has raised the air tank pressure
above that required at the air outlet.
Check Valve (not shown):
When the air compressor is operating, the check valve
is “open”, allowing compressed air to enter the air tank. When the air compressor
reaches “cut-out” pressure, the check valve “closes”, allowing air pressure to
remain inside the air tank.
Pressure Release Valve (not shown):
The pressure release valve located on the
side of the pressure switch, is designed to automatically release compressed air
from the compressor head and the outlet tube when the air compressor reaches
“cut-out” pressure or is shut off. The pressure release valve allows the motor to
restart freely. When the motor stops running, air will be heard escaping from this
valve for a few seconds. No air should be heard leaking when the motor is running,
or continuous leaking after unit reaches cut-out pressure.
Pressure Switch (B) Fig. 1:
The pressure switch automatically starts the motor
when the air tank pressure drops below the factory set “cut-in” pressure. It stops
the motor when the air tank pressure reaches the factory set “cut-out” pressure.
Safety Valve (C) Fig. 1:
If the pressure switch does not shut off the air compressor
at its cut-out pressure setting, the safety valve will protect against high pressure by
“popping out” at its factory set pressure (slightly higher than the pressure switch
cut-out setting).
Outlet Pressure Gauge (D) Fig. 1:
The outlet pressure gauge indicates the air
pressure available at the outlet side of the regulator. This pressure is controlled by
the regulator and is always less than or equal to the tank pressure.
Tank Pressure Gauge (E) Fig. 1:
The tank pressure gauge indicates the reserve air
pressure in the tank.
Regulator (F) Fig. 1:
The air pressure coming from the air tank is controlled by the
regulator knob. Turn the knob clockwise to increase pressure and counterclockwise
to decrease pressure. To avoid minor readjustment after making a change in
pressure setting, always approach the desired pressure from a lower pressure.
When reducing from a higher to a lower setting, first reduce to some pressure less
than that desired, then bring up to the desired pressure. Depending on the air
requirements of each particular accessory, the outlet regulated air pressure may
have to be adjusted while you are operating the accessory.
Fig. 1
B
A
E
D
F
C
Содержание CPF23400P
Страница 17: ...17 ENG NOTES...