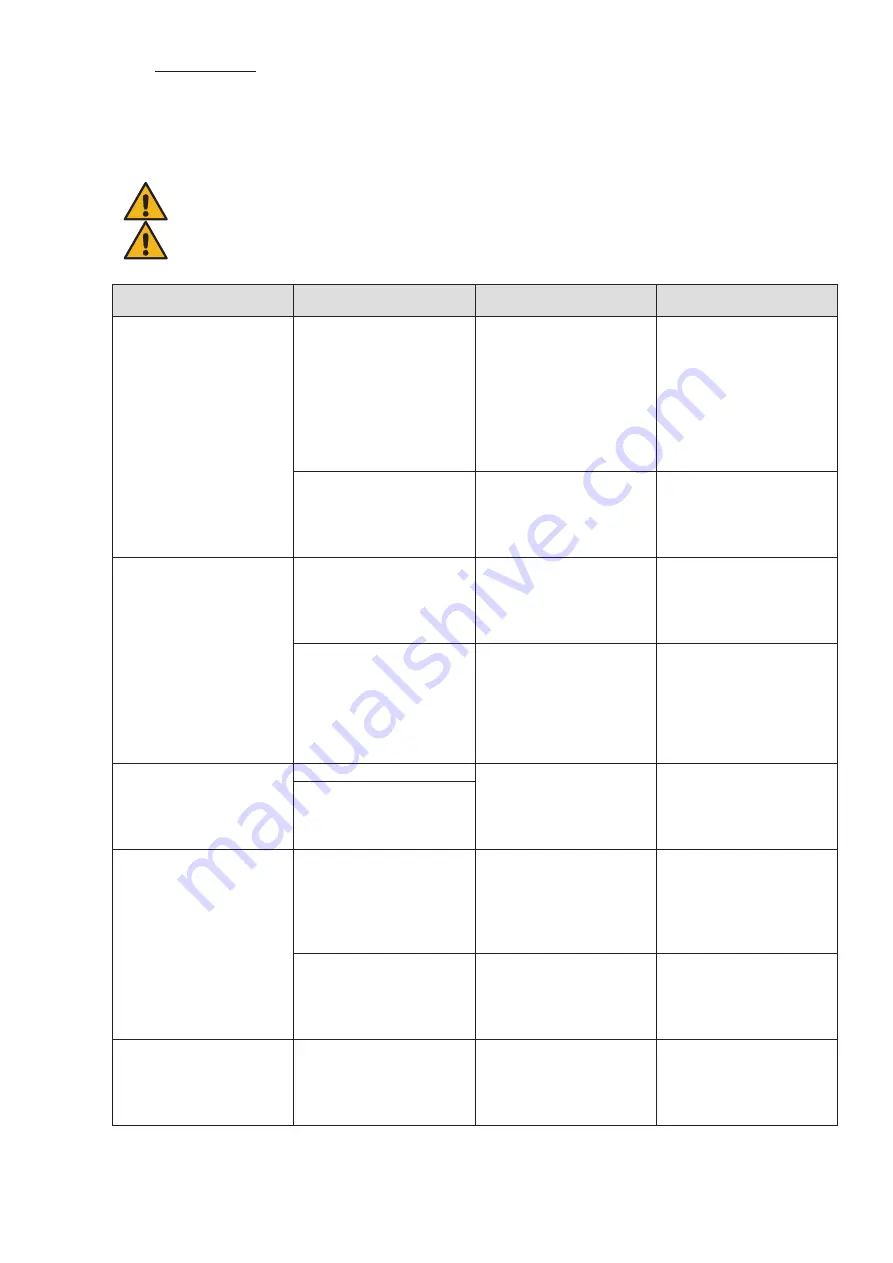
33
33
9
Malfunctions
Hoist trolley units last very long without malfunctions when maintenance is regularly preformed,
but malfunctions are is unavoidable. Below table shows malfunctions which might occur.
-
When a malfunction has been found it has to be reported immediately, to the
owner, who has to initiate repair work, which is to be carried out by competent
maintenance personnel.
-
All malfunctions and repairs must be written in a logbook.
-
Warning!
Repair work may only be performed when the equipment is out of
service.
-
Warning!
Parts must always be replaced when damage occurs that directly or
indirectly endangers the safety of the hoist.
Malfunction
Cause
Explanation
Remedy
The pawl makes a
proper clicking sound
but fails to lift the
load.
Worn friction plates.
When the hoist is
frequently used, the
friction plates will
wear. This results in
gaps between the
friction disk, bushing
and hand chain wheel
causing the brake to
slip.
Replace the friction
plates and bushing.
The braking surface is
dirty or oily causing
the load to slip.
The braking surface
shall be clean and free
of lubricants because it
is a dry-type brake.
Clean the braking
surface or if
necessary, replace the
brake and its
components.
The pawl cannot be
heard and fails to lift
the load.
The pawl has been
improperly assembled.
If the pawl is
assembled incorrectly,
it will not properly
mesh with the ratchet
disk.
Reassemble the pawl
and its components.
The pawl is not moving
smoothly.
Dirt has accumulated
on the grease of the
pawl and pawl shaft.
Movement will become
sluggish or the pawl
remains stuck in the
kicked out position.
Reassemble the pawl
and its components
and replace the
lubricant.
Excessive hand chain
force is needed to lift
the load. A squeaking
noise can possibly be
heard.
Worn gear teeth.
Dirt has accumulated
resulting in wear,
damage and improper
meshing of gears.
Replace the pinion,
gear, load gear, gear
case, side plate and
bearings.
Worn or damaged
bearing.
Jerky lowering or
excessive hand chain
force is needed to
lower the load.
The brake is too tight.
As a result of a shock
during operation or
because a load was
suspended for a long
period of time, the
brake tightened.
Free the brake forcibly
by jerking the hand
chain.
The brake is rusted.
The brake hasn’t be
cleaned correctly
during maintenance.
Clean the braking
surface or if
necessary, replace the
brake and its
components.
The hoist drops the
load immediately when
lowering is started.
The braking surface is
dirty or oily causing
the load to slip.
The braking surface
shall be clean and free
of lubricants because it
is a dry-type brake.
Clean the braking
surface or if
necessary, replace the
brake and its
components.
Содержание PKB Series
Страница 44: ...44 10 ton N100 16 ton N160 44 ...
Страница 45: ...45 20 ton N200 25 ton N250 45 ...