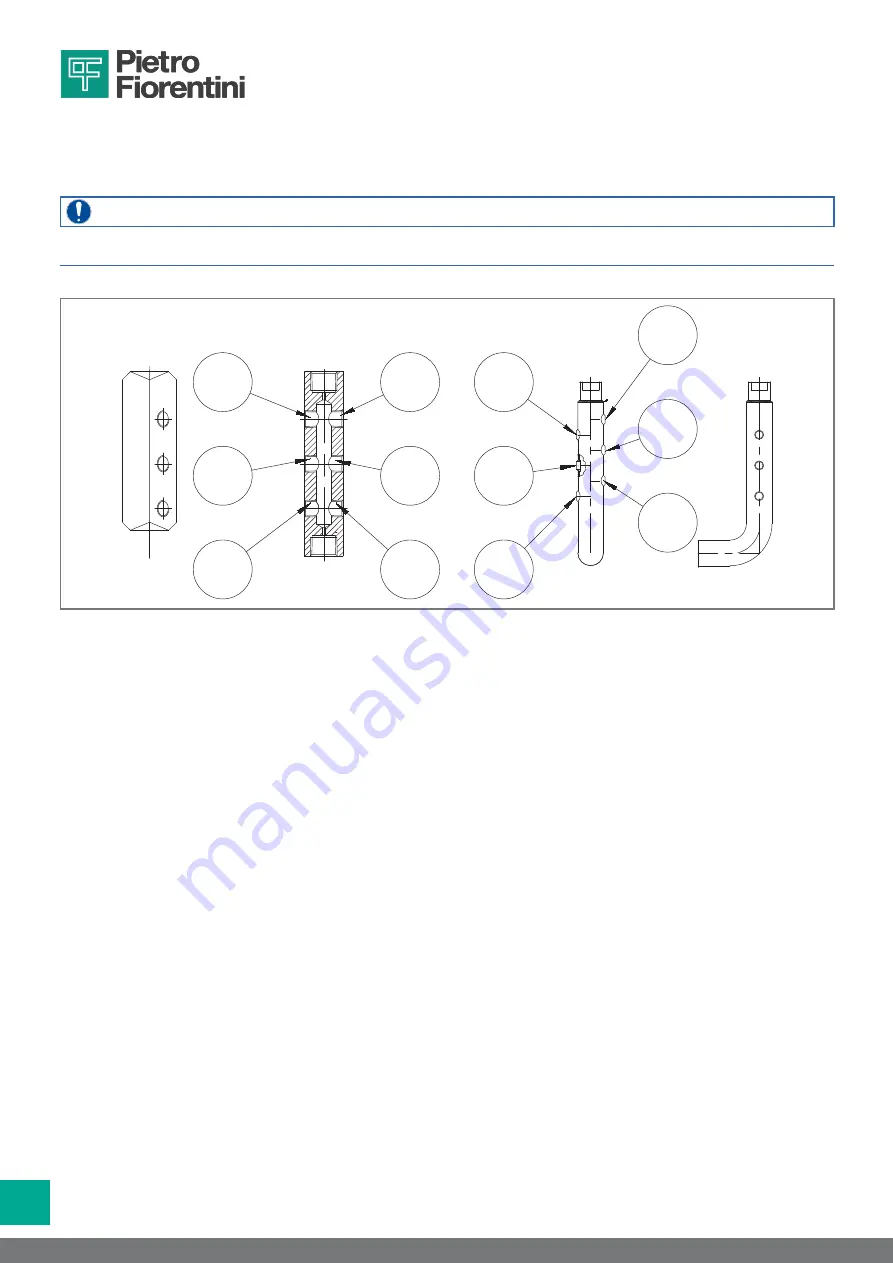
54
HBC 975
EN
Use, maintenance and warning manual
SLAM-SHUT VALVE
|
INSTALLATION
|
REV. 00
If there is a multiple sensing line (see fig. 6.10), provide equipment connections as shown below:
• 3 and 4 to the pilot sensing lines if any;
• 5 and 6 to the sensing lines of the LINE OFF 2.0 pressure switch.
NOTE!
If there is a multiple sensing line, it is not recommended to place shut-off valves on sensing lines.
In any case, follow the regulations in force in the place of installation and use of the equipment.
5
3
1
2
4
6
5
3
1
2
4
6
Fig. 6.10.
Equipment connections
6.6 - POST-INSTALLATION AND PRE-COMMISSIONING CHECKS
Before commissioning, it must be ensured that all connections are:
• properly secured/tightened to prevent any leakage during commissioning;
• connected correctly.
Содержание HBC 975
Страница 1: ...HBC 975 EN Revision 00 Edition 09 2021 Slam shut valve USE MAINTENANCE AND WARNING MANUAL ...
Страница 2: ...2 HBC 975 EN Use maintenance and warning manual SLAM SHUT VALVE INTRODUCTION REV 00 ...
Страница 4: ...4 HBC 975 EN Use maintenance and warning manual SLAM SHUT VALVE INTRODUCTION REV 00 ...
Страница 10: ...10 HBC 975 EN Use maintenance and warning manual SLAM SHUT VALVE INTRODUCTION REV 00 ...
Страница 18: ...18 HBC 975 EN Use maintenance and warning manual SLAM SHUT VALVE GENERAL INFORMATION REV 00 ...
Страница 33: ...33 HBC 975 Use maintenance and warning manual SLAM SHUT VALVE DESCRIPTION AND OPERATION REV 00 EN ...
Страница 36: ...36 HBC 975 EN Use maintenance and warning manual SLAM SHUT VALVE DESCRIPTION AND OPERATION REV 00 ...
Страница 46: ...46 HBC 975 EN Use maintenance and warning manual SLAM SHUT VALVE TRANSPORT AND HANDLING REV 00 ...
Страница 63: ...63 HBC 975 Use maintenance and warning manual SLAM SHUT VALVE COMMISSIONING REV 00 EN ...
Страница 70: ...70 HBC 975 EN Use maintenance and warning manual SLAM SHUT VALVE COMMISSIONING REV 00 ...
Страница 85: ...85 HBC 975 Use maintenance and warning manual SLAM SHUT VALVE MAINTENANCE AND FUNCTIONAL CHECKS REV 00 EN ...
Страница 88: ...88 HBC 975 EN Use maintenance and warning manual SLAM SHUT VALVE MAINTENANCE AND FUNCTIONAL CHECKS REV 00 ...
Страница 142: ...142 HBC 975 EN Use maintenance and warning manual SLAM SHUT VALVE MAINTENANCE AND FUNCTIONAL CHECKS REV 00 ...
Страница 148: ...148 HBC 975 EN Use maintenance and warning manual SLAM SHUT VALVES TROUBLESHOOTING REV 00 ...
Страница 152: ...152 HBC 975 EN Use maintenance and warning manual SLAM SHUT VALVE RECOMMENDED SPARE PARTS REV 00 ...
Страница 156: ......