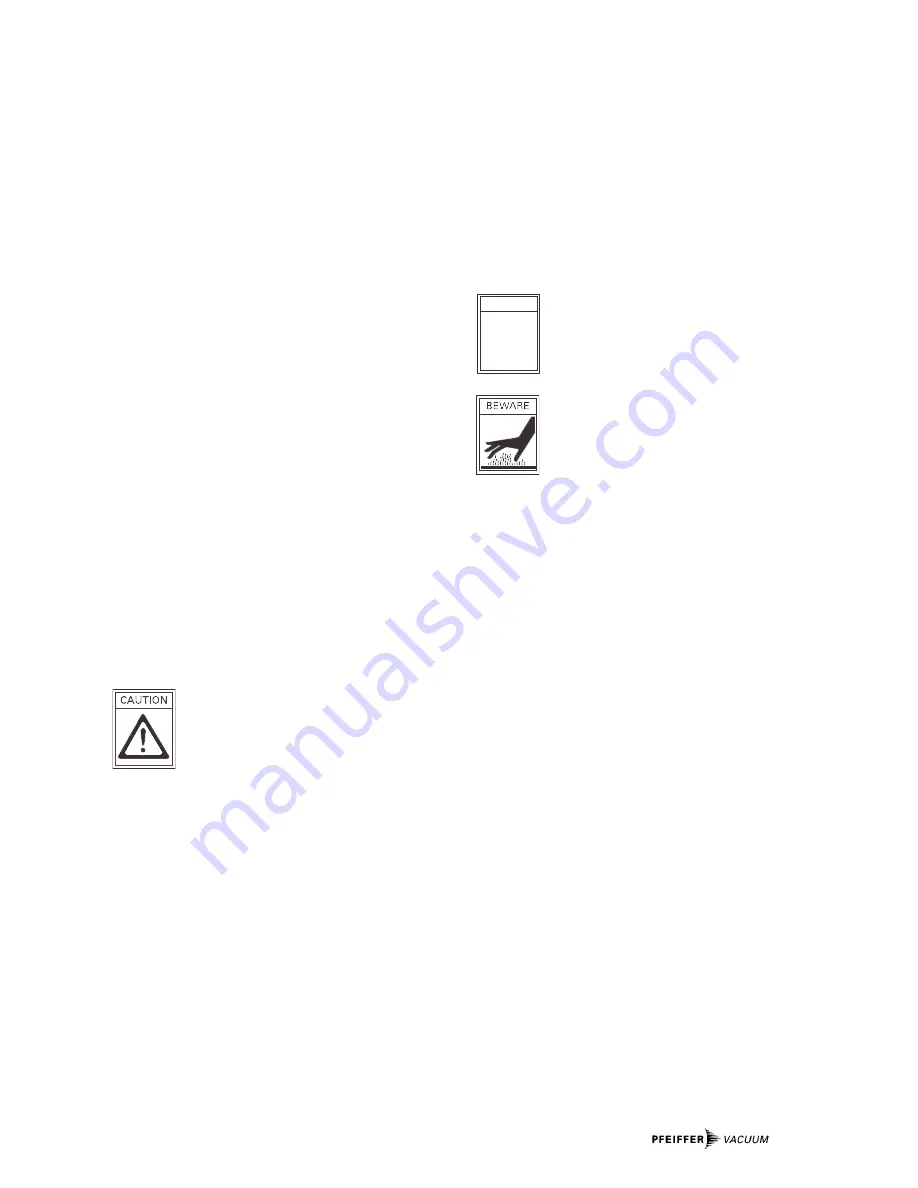
7
3.4. Connecting The Cooling Unit
The Turbopumps TMH 262/TMU 262 must be water or air
cooled.
Air cooling may only be used where the ambient temperature
is < 35 °C.
Use and installation:
– For water cooling please refer to Operating Instructions
PM 800 546 BN.
– For air cooling please refer to Operating Instructions
PM 800 543 BN.
3.5. Connecting The Venting Valve
The venting valve (accessory) provides automatic venting in
the event of a power failure and switching off.
Fitting the venting valve
➡
Unscrew the venting screw from the venting connection of
the turbopump.
➡
Screw in venting valve with seal (USIT ring) on hexagonal
SW 14.
Electrical connection
Electrical connection
➡
Plug control lead into the connection ”Out 2” of the
TCS 010 or in accordance with the connections diagram
(please see Section 3.13.).
For Details please refer to Operating Instructions for the
Connection Box TCS 010, PT 800 045 BN.
The venting mode of the venting valve is selected via the DCU
or Serial Interface RS 485.
The maximum pressure at the venting valve is
1.5 bar absolute.
Please refer to Operating Instructions PM 800 507 BN for
details on Venting Valve TVV 005.
3.6. Connecting The Casing Heating Unit
In order to accelerate attainment of final pressures,
turbopumps and vacuum chambers can be heated.
Baking out is only practical on pumps with stainless steel
casings (TMU pumps). On account of their aluminium casings,
the temperatures attainable on TMH pumps are not high
enough.
Heating duration is dependent on the level of contamination
and the required final pressure but should be at least four
hours.
Where casing heating is involved the turbopump
must be water cooled.
High temperatures are generated when
turbopumps are heated.
There is a danger of injury from coming into
contact with hot parts even after the casing hea-
ting has been switched off.
Heating sleeve and the pump casing should be thermally
insulated during the installation. During the heating phase be
careful not to come into contact with the heating sleeve or
the pump casing.
Casing heating control is effected via the TCS 010 (please
refer to Operating Instructions PT 800 045 BN for the TCS 010)
or in accordance with the connections diagram (please see
Section 3.13.).
For details regarding the casing heating and its installation
please refer to Operating Instructions PM 800 542 BN.
☞
PLEASE NOTE