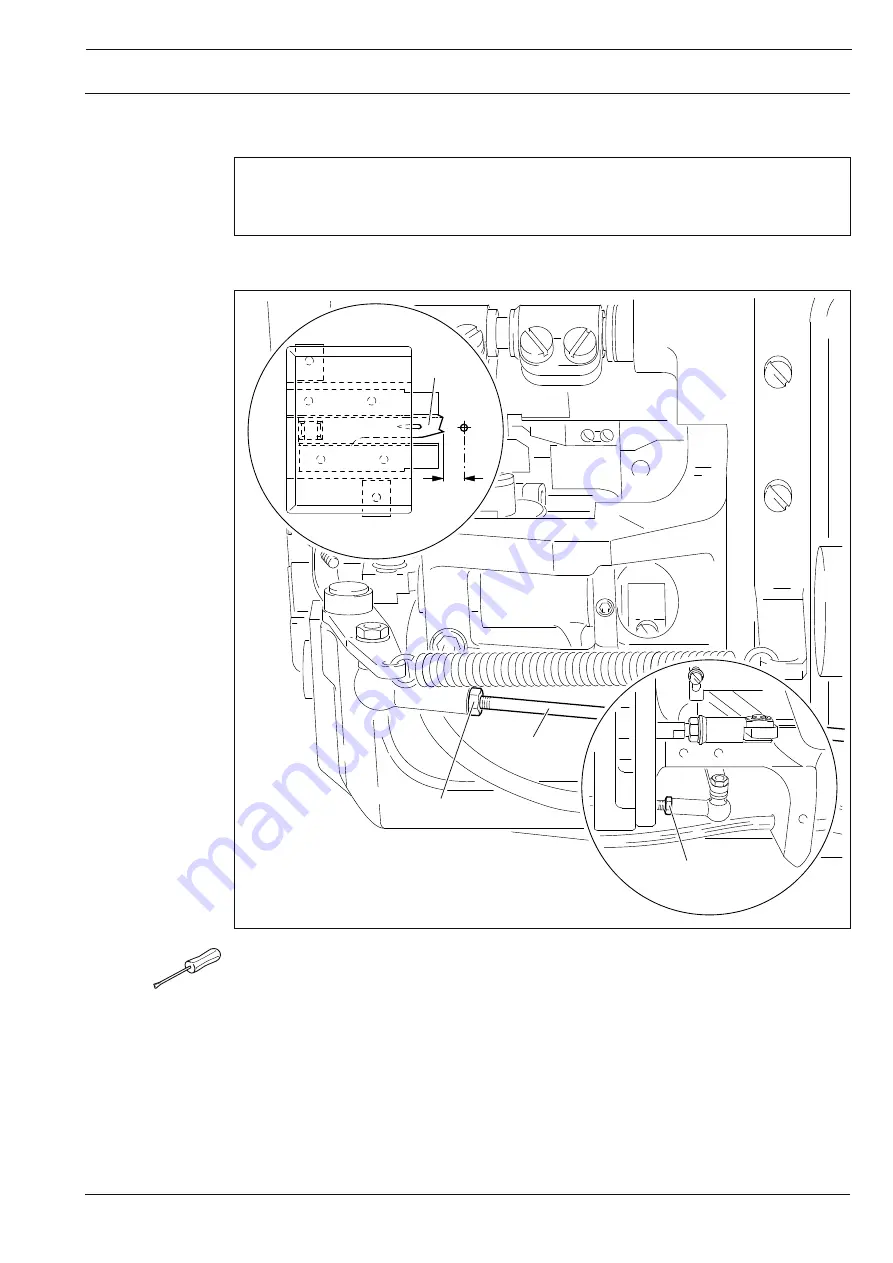
Adjustment
13 - 38
Fig. 13 - 35
4
7 mm
2
1
3
13
.06.03
Thread catcher position with respect to needle
Requirement
With the thread trimmer in its resting position, the point of the thread catcher
4
must be at a
distance of
7 mm
to the center of the needle.
●
Bring the thread trimmer into its resting position.
●
Turn connecting rod
1
(nut
2
, nut
3
with left-hand thread) according to the
requirement
.
Содержание 3801-11/071
Страница 19: ...Controls 7 4 7 07 Reverse feed control lever To sew condensed stitches press lever 1 down Fig 7 08 1 ...
Страница 122: ...15 3 Circuit diagrams Version 01 09 05 91 191 495 95 Page 1 ...
Страница 123: ...15 4 91 191 495 95 Page 2 Version 01 09 05 Circuit diagrams ...
Страница 124: ...15 5 Circuit diagrams Version 01 09 05 91 191 495 95 Page 3 ...
Страница 125: ...15 6 91 191 495 95 Page 4 Version 01 09 05 Circuit diagrams ...