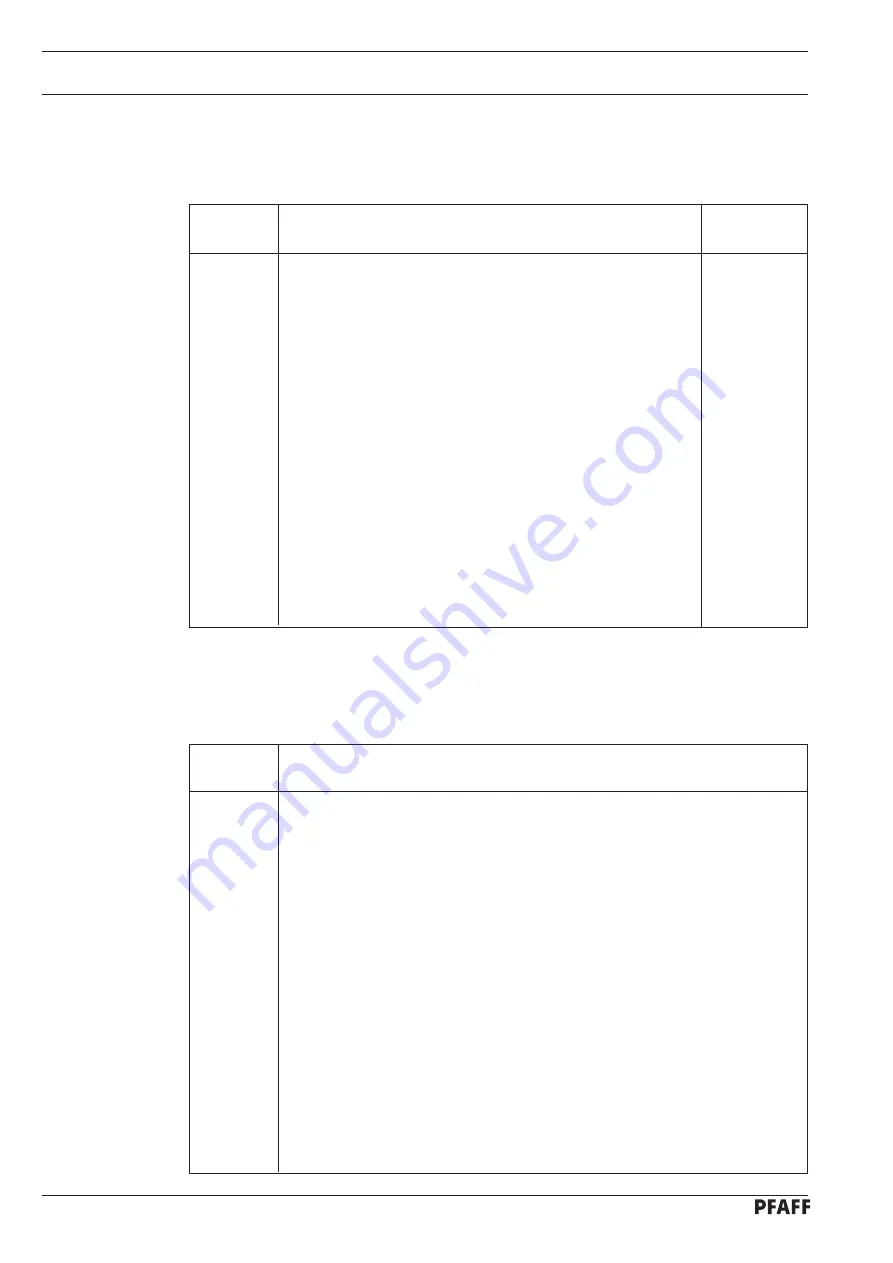
14 - 19
Control unit
14
.03.03
Table of outputs
Nodes A10/X300
OUT1
Y1.1
Loading table backwards
0
OUT2
Y1.2
Loading table forwards
1
OUT3
Y2
Suction on
2
OUT4
Y3
Needle strip down
3
OUT5
Y4
Pressure bar down
4
OUT6
Y5
Sewing foot up
5
OUT7
Y6
Thread tension on
6
OUT8
Y7
Thread trimmer on
7
OUT9
Y8
Air blast on
8
OUT10
Y9.1
Material clamp down (optional)
9
OUT11
Y9.2
Material clamp up (optional)
10
OUT12
OUT1
Programmable output 1
11
OUT13
OUT 2
Programmable output 2
12
OUT14
13
OUT15
14
OUT16
15
14
.03.04
Table of inputs
Nodes A10/X400
Input
Denomination
IN1
IN1
programmable input 1
IN2
IN2
programmable input 2
IN3
E1.1
loading table back
IN4
E1.2
loading table forward
IN5
E1.3
loading table at centre (pushed back)
IN6
E5
sewing foot raised
IN7
SMXNULL
zero position SMX
IN8
SMYNULL
zero position SMY
IN9
SMTNULL
zero position SM material take-over (depth)
IN10
THERR
needle thread error
IN11
FKEY
key for secured functions
IN12
SMXLIMIT
impermissible position for SMX
IN13
E10
Bobbin flap closed
IN14
E11
U-bar attached
IN15
IN16
Output
Denomination
Index
number
Содержание 3586-2/02
Страница 4: ......
Страница 10: ...1 5 Safety...
Страница 22: ...Control elements 7 5...
Страница 34: ...Preparation 9 7...
Страница 88: ...11 48 Input...
Страница 90: ......
Страница 126: ...13 30 Adjustment...
Страница 149: ...15 3 91 191 431 95 Version 21 05 02 Mains supply 230 V...
Страница 150: ...15 4 Axle drives Version 21 05 02 91 191 431 95...
Страница 151: ...15 5 91 191 431 95 Version 21 05 02 Sewing drive...
Страница 152: ...15 6 Circuit diagram outputs Version 21 05 02 91 191 431 95...
Страница 153: ...15 7 91 191 431 95 Version 21 05 02 Circuit diagram inputs...
Страница 154: ...15 8 Circuit diagram A20 A26 A30 A50 Version 21 05 02 91 191 431 95...
Страница 155: ...15 9 91 191 431 95 Version 21 05 02 Circuit diagram A21 A23...