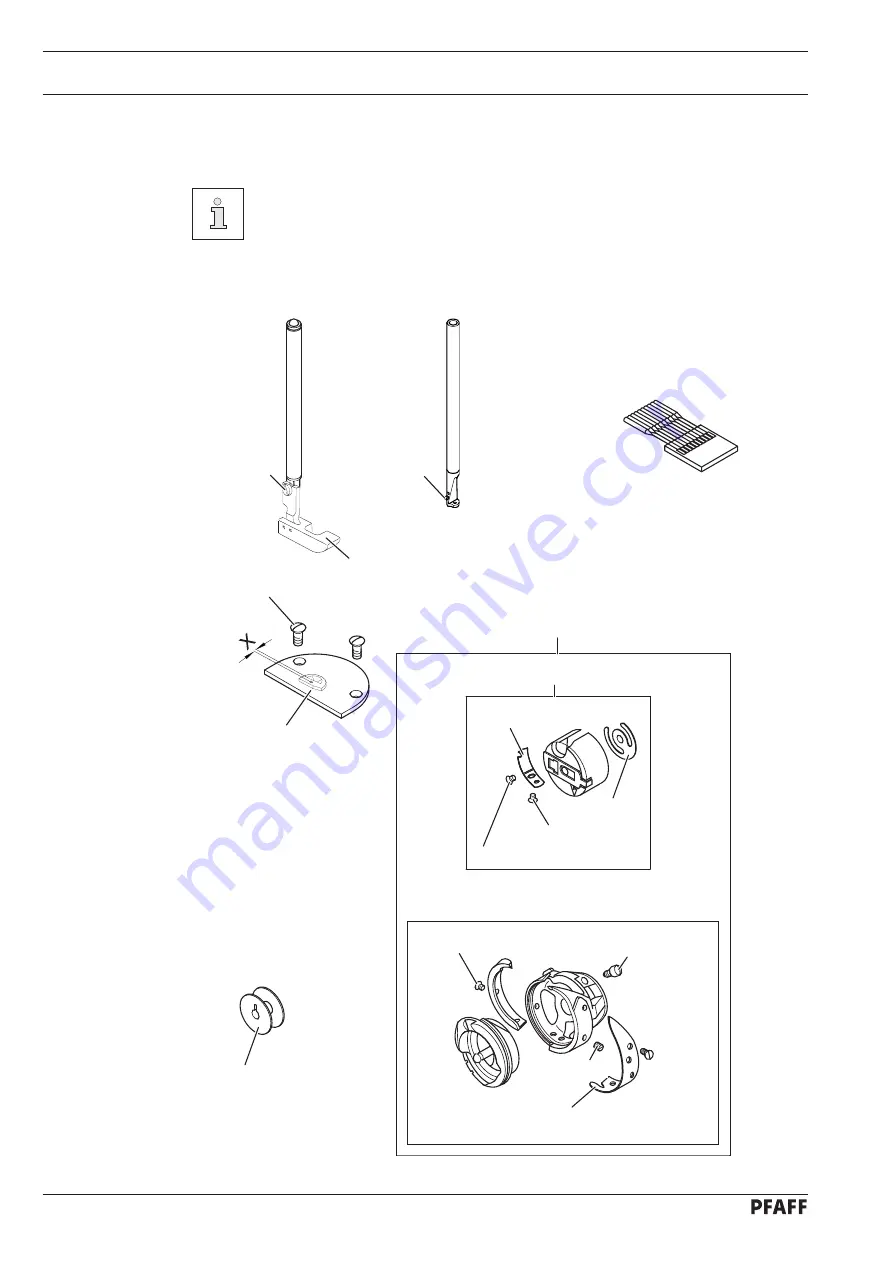
Wearing parts
98
13 Wearing
parts
This is a list of the most important wearing parts.
A detailed parts list for the complete machine is included with the accessories.
In case of loss, the parts list can be downloaded from the internet address
www.pfaff-industrial.de/pfaff/de/service/downloads
. As an alternative to
the internet download the parts lists can also be ordered in book form under
part no.
296-12-19 009.
134 KK
91-100 296-25(2x)
91-150 890-03/001(
X
= 3,5 mm)
91-150 890-03/002(
X
= 5 mm)
11-108 174-25
11-330 958-15
91-154 921-91
91-262 250-91
91-262 377-91
99-137 192-05
99-137 191-05
99-137 193-05
99-137 194-05
99-137 187-15 (2x)
99-137 190-05 (3x)
99-137 188-15
99-137 186-05
99-137 189-15 (2x)
91-262 437-05
Содержание 3511-2/01
Страница 102: ...102 Circuit diagrams Version 22 05 06 91 191 500 95 Part1...
Страница 103: ...103 91 191 500 95 Part 2 Version 22 05 06 Circuit diagrams...
Страница 104: ...104 Circuit diagrams Version 22 05 06 91 191 500 95 Part 3...
Страница 105: ...105 91 191 500 95 Part 4 Version 22 05 06 Circuit diagrams...