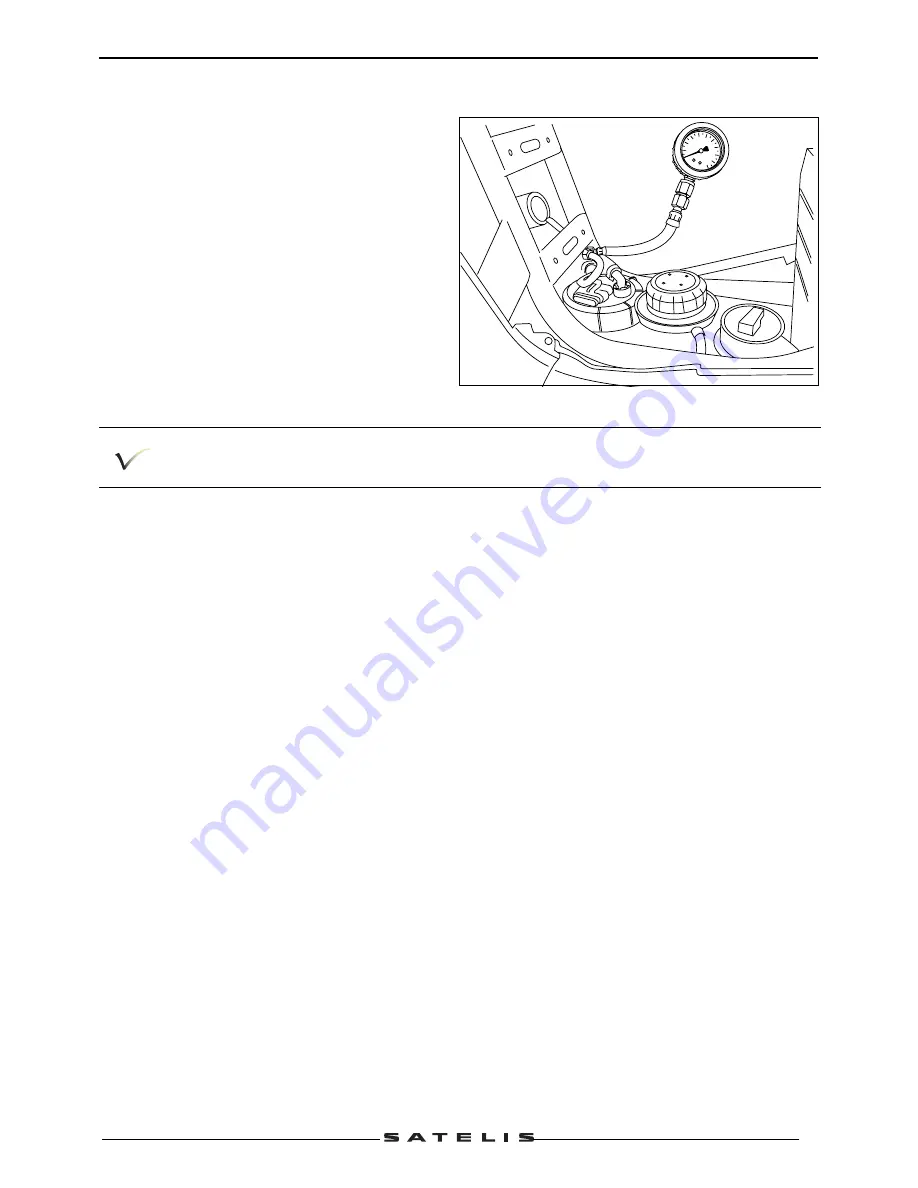
MISCELLANEOUS OPERATIONS
65
Reproduction or translation, even partial, is forbidden without the written consent of Peugeot Motocycles
Checking fuel pressure
- Carry out the procedure for lowering the
pressure in the fuel system. See:
Gamme 10. Page: 64.
- Disconnect the fuel supply hose.
- Insert the pressure gauge P/N 757877
between the gauge well and the supply hose
- Always use hose clamps that are in good
condition.
- Turn the ignition on 3 times to bleed the fuel
system.
- With the engine stopped, check the fuel
pressure which must be 2.5 bars when
switching on the fuel pump.
Before disconnecting the pressure gauges, lower the fuel pressure in the fuel system.
Always reinstall the hoses with new hose clamps.
0
6
8
10
2
4
bar