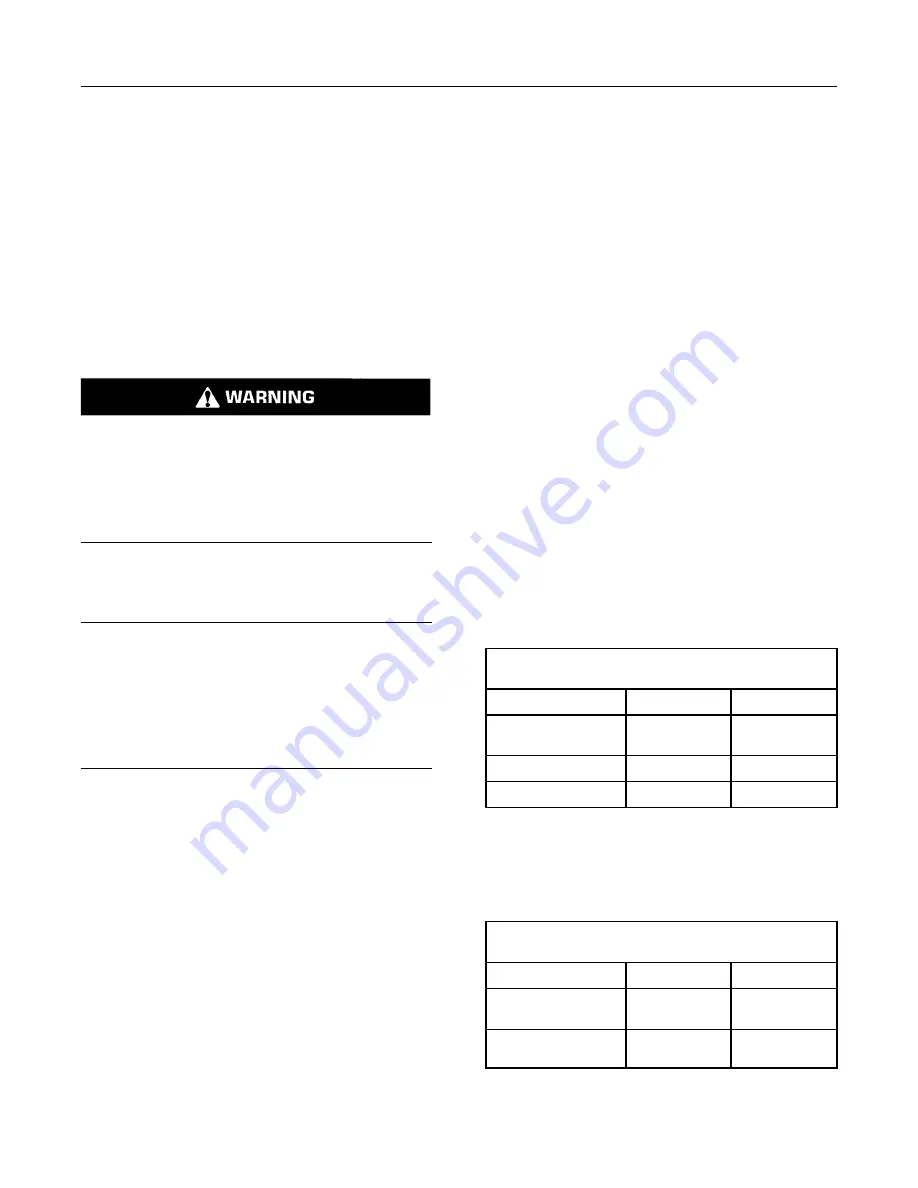
• The ambient temperature
• The speed of the engine
Refer to the Fault Conditions And Possible Causes
in Table 12 .
i01899136
Battery - Test
Most of the tests of the electrical system can be done
on the engine. The wiring insulation must be in good
condition. The wire and cable connections must be
clean, and both components must be tight.
Never disconnect any charging unit circuit or bat-
tery circuit cable from the battery when the charg-
ing unit is operated. A spark can cause an
explosion from the flammable vapor mixture of
hydrogen and oxygen that is released from the
electrolyte through the battery outlets. Injury to
personnel can be the result.
The battery circuit is an electrical load on the
charging unit. The load is variable because of the
condition of the charge in the battery.
NOTICE
The charging unit will be damaged if the connections
between the battery and the charging unit are broken
while the battery is being charged. Damage occurs
because the load from the battery is lost and because
there is an increase in charging voltage. High voltage
will damage the charging unit, the regulator, and other
electrical components.
The correct procedures to test the battery can be
found in the manual that is supplied by the OEM.
i01945632
Electric
Starting
System
-
Test
General Information
All electrical starting systems have four elements:
• Ignition switch
• Start relay
• Starting motor solenoid
• Starting motor
Start switches have a capacity of 5 to 20 amperes.
The coil of a start relay draws about 1 ampere
between test points. The switch contacts of the start
relay for the starting motor are rated between 100 and
300 amperes. The start relay can easily switch the
load of 5 to 50 amperes for the starting motor
solenoid.
The starting motor solenoid is a switch with a capacity
of about 1000 amperes. The starting motor solenoid
supplies power to the starter drive. The starting motor
solenoid also engages the pinion to the flywheel.
The starting motor solenoid has two coils. The pull-in
coil draws about 40 amperes. The hold-in coil
requires about 5 amperes.
When the magnetic force increases in both coils, the
pinion gear moves toward the ring gear of the
flywheel. Then, the solenoid contacts close in order to
provide power to the starting motor. When the
solenoid contacts close, the ground is temporarily
removed from the pull-in coil. Battery voltage is
supplied on both ends of the pull-in coil while the
starting motor cranks. During this period, the pull-in
coil is out of the circuit.
Cranking of the engine continues until current to the
solenoid is stopped by releasing the ignition switch.
Power which is available during cranking varies
according to the temperature and condition of the
batteries. The following chart shows the voltages
which are expected from a battery at the various
temperature ranges.
Table 13
Typical Voltage Of Electrical System During Cranking At Vari-
ous Ambient Temperatures
Temperature
12 Volt System
24 Volt System
−23 to −7°C
(−10 to 20°F)
6 to 8 volts
12 to 16 volts
−7 to 10°C (20 to 50°F)
7 to 9 volts
14 to 18 volts
10 to 27°C (50 to 80°F)
8 to 10 volts
16 to 24 volts
The following table shows the maximum acceptable
loss of voltage in the battery circuit. The battery circuit
supplies high current to the starting motor. The values
in the table are for engines which have service of
2000 hours or more.
Table 14
Maximum Acceptable Voltage Drop In The Starting Motor Cir-
cuit During Cranking
Circuit
12 Volt System
24 Volt System
Battery post
“
-
”
to the
starting motor terminal
“
-
”
0.7 volts
1.4 volts
Drop across the discon-
nect switch
0.5 volts
1.0 volts
(continued)
UENR0617
51
This document has been printed from SPI2. NOT FOR RESALE.