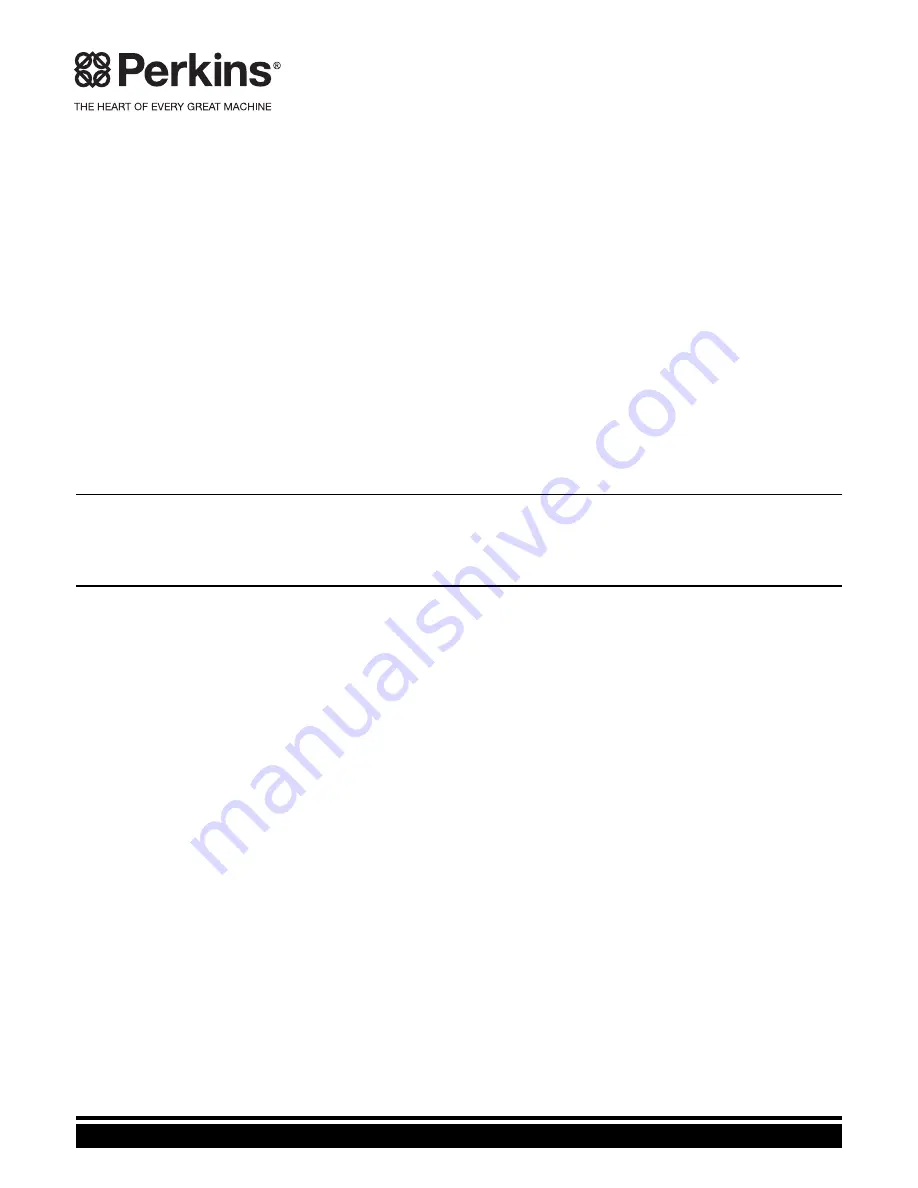
Systems Operation
Testing and Adjusting
1106A-70T, 1106A-70TA, 1106C-70TA
and 1106D-70TA Industrial Engines
PP
(Engine)
PR
(Engine)
PT
(Engine)
PU
(Engine)
UENR0617-01
April 2014
This document has been printed from SPI2. NOT FOR RESALE.