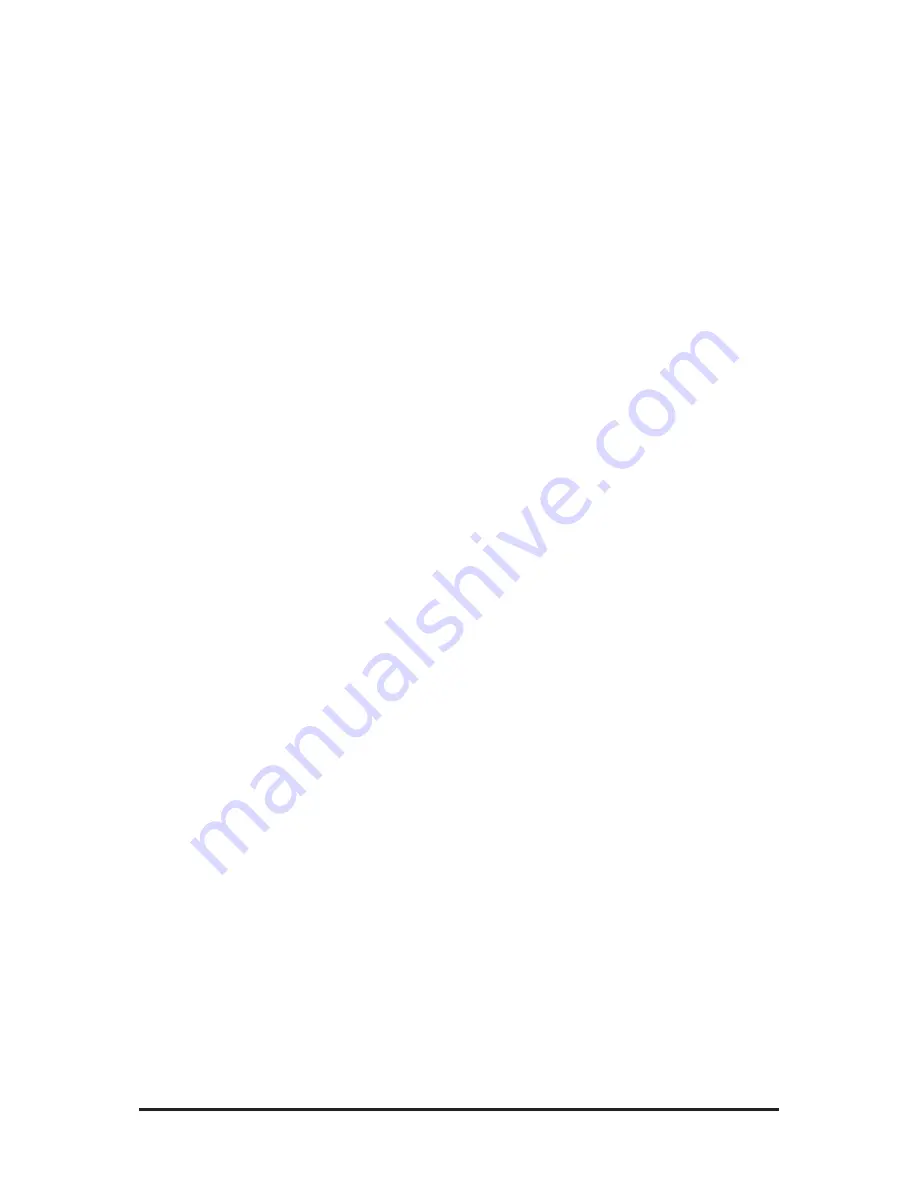
1/01 E Service Instructions
18
Cutting System
Maintenance
It should be ensured that the knife
beam guideways are lubricated at the
top and bottom positions of the
knife beam. Refer to "Lubrication" in
the Operating Instructions manual.
A lubrication chart is provided on
the back of the machine.
Never use knives other than those
assigned to the respective ma-chine
models and sizes.
For PERFECTA guillotines of the
same models and sizes, the knives
are interchangeable.
When changing the knife, ensure,
under any circumstances, that the
tapped holes in the knife are clean
and the knife bolts are undamaged.
Cutting Table
All PERFECTA guillotines are
supplied with standard cutting ta-
bles and the associated side ta-
bles with ground surfaces and of
special-quality cast iron. In the
factory, the tables are provided
with temporary corrosion protec-
tive before being shipped. When
the machine is installed at the
user's, this corrosion preventive
must be removed with white spirit.
Never use any caustic agents.
The clean table is susceptible to
corrosion, particularly in the han-
dling area.
PERFECTA offers corrosion-pro-
tective wax which inhibits corro-
sion and improves the sliding prop-
erties.
Due to the abrasion caused by the
cutting stock, the treatment must
be repeated from time to time.
If small deposits of rust should
have built up as a result of insuf-
ficient care or negligence, remove
them immediately. Never use
abrasive cloth or sand paper. Ti-
tanium fleece or a conventional
household fibre scouring pad has
proven useful for this purpose.
When treating the table always
work in the grinding direction.
PERFECTA offers optional cut-
ting and side tables with upgraded,
i. e. corrosion-resistant surfaces.
Backgauge
Drive System
All PERFECTA guillotines have a
controlled backgauge drive sys-
tem.The advantage of this drive
system is a gentle approaching to
and a soft, precise positioning of
the cut measurement. The opti-
mum backgauge speed is auto-
matically determined from the dis-
tance between the cut marks.
For most of the applications, the
guillotines are factory-set to opti-
mum. Via the "Speed" (TV)/"Set-
tings" (UC) menu, the backgauge
speeds as well as the start and
stop ramps can be adapted to the
stock to be processed and to
other requirements.
For manual positioning, cutting or
programming according to the
print,
PERFECTA
guillotines have
a so-called "electronic hand-
wheel" with nine different forward
and reverse speeds each. Refer
to "Backgauge" in the Operating
Instructions manual.
Содержание 115 TV
Страница 5: ...1 01 E Service Instructions 5 Fig 2 ...