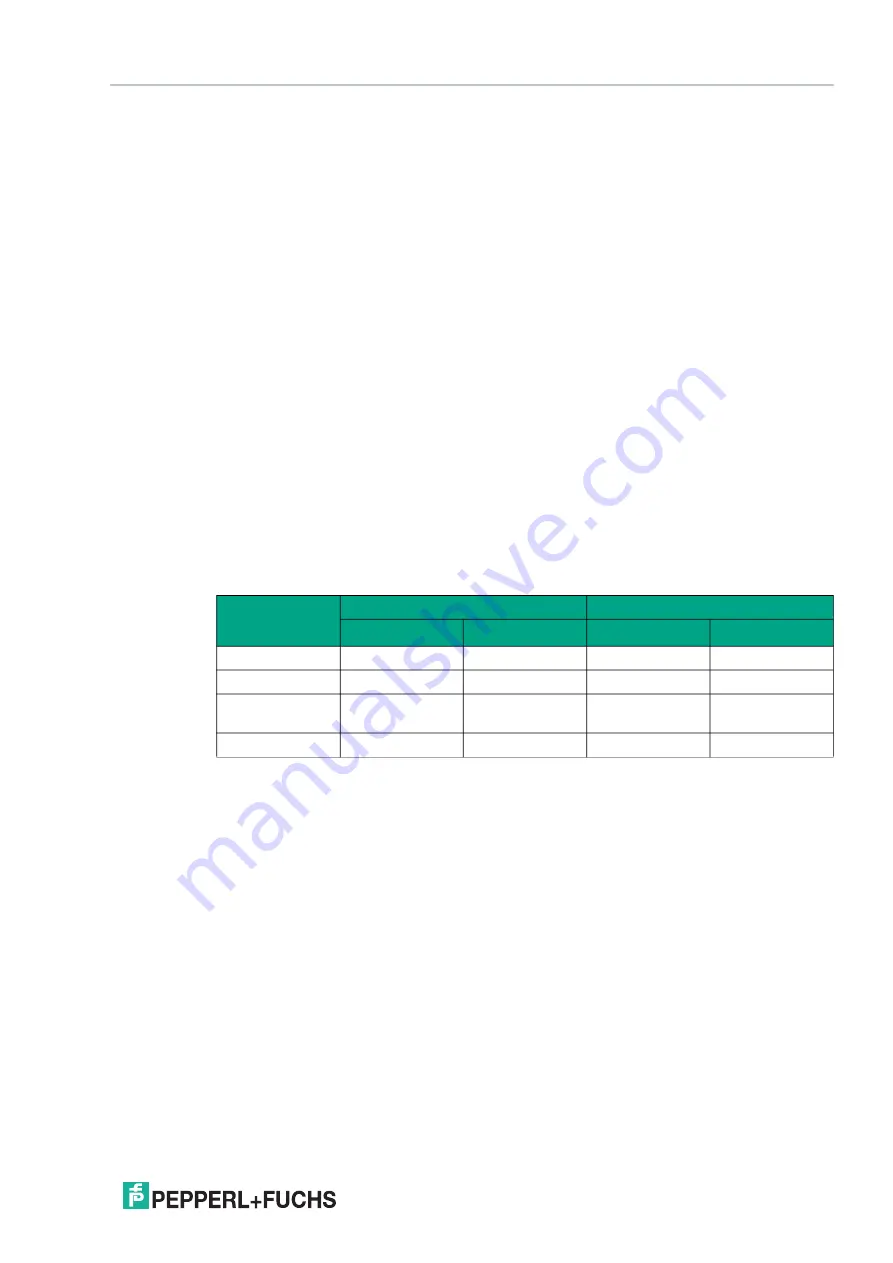
Functional Safety K-LB-*.*, F*-LB-I, P-LB-*.*.*
Planning
20
21
-0
9
11
3.2
Assumptions
The following assumptions have been made during the FMEDA:
•
The stress levels are average for an industrial environment and the environment is similar
to IEC/EN 60654-1 Class C (sheltered location) with temperature limits in the range
of the manufacturer's specifications and an average temperature of 40
º
C over a long
period. The humidity level is within manufacturer's rating.
•
The listed failure rates are valid for operating stress conditions typical of an industrial field
environment similar to IEC/EN 60654-1 Class C with an average temperature over a long
period of time of 40
º
C. For a higher average temperature of 60
º
C, the failure rates must
be multiplied by a factor of 2.5 based on experience. A similar factor must be used
if frequent temperature fluctuations are expected.
•
Failure rate based on the Siemens standard SN 29500.
•
The control loop has a hardware fault tolerance of
0
and it is a type
A
device.
A SFF value for this device is not given, since this value has to be calculated
in conjunction with the connected field device, as described in the following section.
Application Information
The surge protection barrier and the connected device (field device, isolator or actuator) have
to be considered together. The PFD
avg
/PFH budget of the device categories in the entire
safety loop is, see Figure 5.1:
•
Actuator (valve) 40 %
•
Transmitter (sensor) 25 %
•
Isolator 10 %
As an overview for SIL 2/SIL 3 safety loop this means:
SIL 2
SIL 3
PFH
PFD
avg
PFH
PFD
avg
Total
10
-6
10
-2
10
-7
10
-3
Actuator (40 %) 4 x 10
-7
4 x 10
-3
4 x 10
-8
4 x 10
-4
Transmitter
(25 %)
2.5 x 10
-7
2.5 x 10
-3
2.5 x 10
-8
2.5 x 10
-4
Isolator (10 %)
10
-7
10
-3
10
-8
10
-4
Table 3.1 Overview PFD
avg
/PFH budget