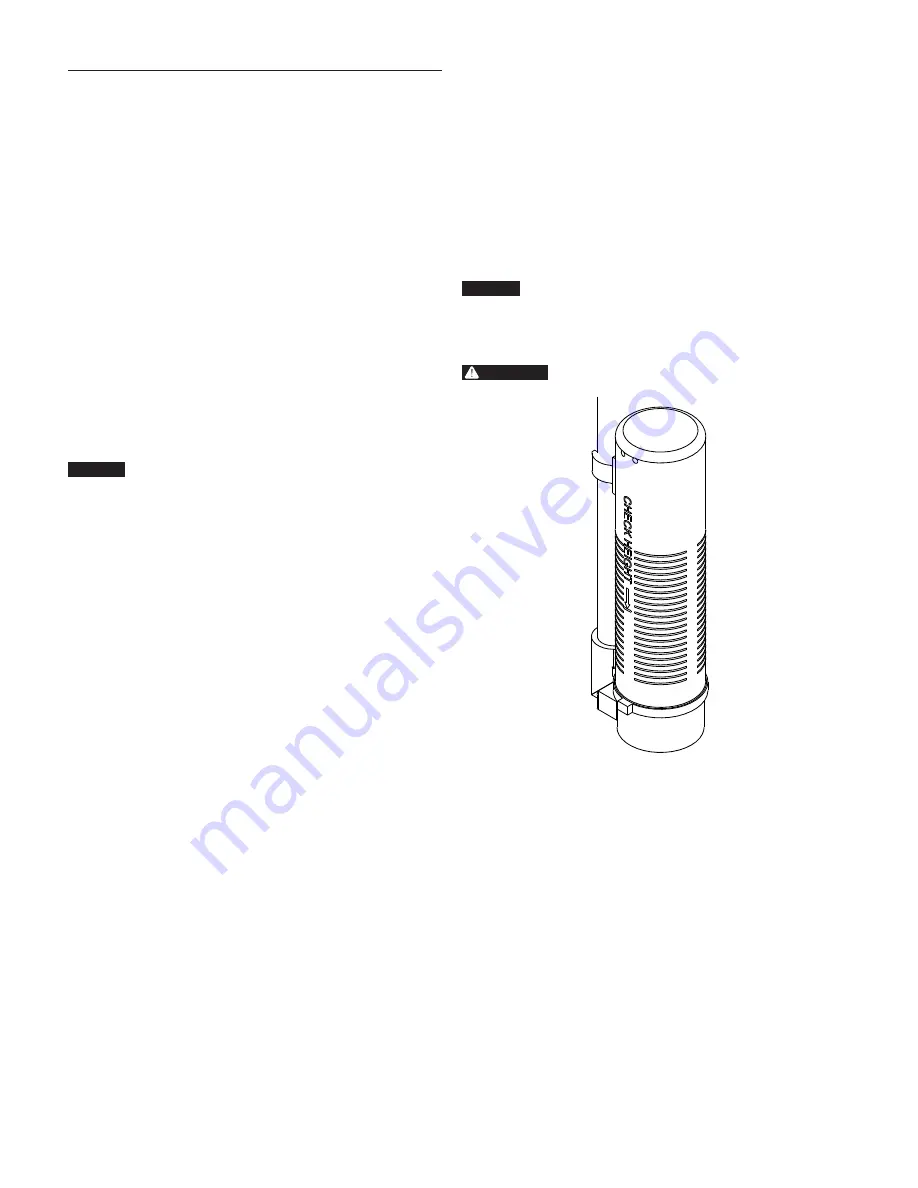
4
•
FLECK
Model ProFloSXT Downflow Service Manual
INSTALLATION INSTRUCTIONS
Water Pressure
A minimum of 20 psi (1.4 bar) of water pressure is required for
regeneration valve to operate effectively.
Electrical Facilities
An uninterrupted alternating current (A/C) supply is required.
NOTE:
Other voltages are available. Please make sure your
voltage supply is compatible with your unit
before installation.
Existing Plumbing
Condition of existing plumbing should be free from lime and
iron buildup. Piping that is built up heavily with lime and/or iron
should be replaced. If piping is clogged with iron, a separate iron
filter unit should be installed ahead of the water softener.
Location Of Softener And Drain
The softener should be located close to a drain to prevent air
breaks and back flow.
By-Pass Valves
Always provide for the installation of a by-pass valve if unit is
not equipped with one.
CAUTION
Water pressure is not to exceed 125 psi (8.6 bar),
water temperature is not to exceed 110°F (43°C), and
the unit cannot be subjected to freezing conditions.
Installation Instructions
1. Place the softener tank where you want to install the unit
making sure the unit is level and on a firm base.
2. During cold weather, the installer should warm the valve to
room temperature before operating.
3. All plumbing should be done in accordance with local
plumbing codes. The pipe size for residential drain line
should be a minimum of 1/2 inch (13 mm). Backwash
flow rates in excess of 7 gpm (26.5 Lpm) or length in
excess of 20 feet (6 m) require 3/4 inch (19 mm) drain line.
Commercial drain lines should be the same size as the
drain line flow control.
4. Refer to the dimensional drawing for cutting height of the
distributor tube. If there is no dimensional drawing, cut the
distributor tube flush with the top of the tank.
5. Lubricate the distributor o-ring seal and tank o-ring seal.
Place the main control valve on tank.
NOTE:
Only use silicone lubricant.
6. Solder joints near the drain must be done prior to
connecting the Drain Line Flow Control fitting (DLFC). Leave
at least 6 inches (15 cm) between the DLFC and solder
joints when soldering pipes that are connected on the DLFC.
Failure to do this could cause interior damage to the DLFC.
7. Plumber tape is the only sealant to be used on the drain
fitting. The drain from twin tank units may be run through a
common line.
8. Make sure that the floor is clean beneath the salt storage
tank and that it is level.
9. Place approximately 1 inch (25 mm) of water above the grid
plate. If a grid is not utilized, fill to the top of the air check
(Figure 1) in the salt tank. Do not add salt to the brine tank
at this time.
10. On units with a by-pass, place in by-pass position. Turn on
the main water supply. Open a cold soft water tap nearby
and let run a few minutes or until the system is free from
foreign material (usually solder) that may have resulted
from the installation. Once clean, close the water tap.
11. Slowly place the by-pass in service position and let water
flow into the mineral tank. When water flow stops, slowly
open a cold water tap nearby and let run until the air is
purged from the unit.
12. Plug unit into an electrical outlet.
NOTE:
All electrical connections must be connected
according to local codes. Be certain the outlet
is uninterrupted.
CAUTION
• Do not exceed 125 psi water pressure
• Do not exceed 110°F (43°C) water temperature
• Do not subject unit to freezing conditions
WARNING:
The system MUST be depressurized before
removing any connections for servicing.
Figure 1 Residential Air Check Valve
Содержание FLECK PROFLOSXT DOWNFLOW
Страница 1: ...www pentairaqua com FLECK MODEL PROFLOSXT DOWNFLOW SERVICE MANUAL...
Страница 14: ...14 FLECK Model ProFloSXT Downflow Service Manual CONTROL VALVE ASSEMBLY...
Страница 24: ...24 FLECK Model ProFloSXT Downflow Service Manual FLOW DATA INJECTOR DRAW SLOW RINSE RATES...
Страница 25: ...FLECK Model ProFloSXT Downflow Service Manual 25 DIMENSIONAL DRAWING...
Страница 31: ...FLECK Model ProFloSXT Downflow Service Manual 31...