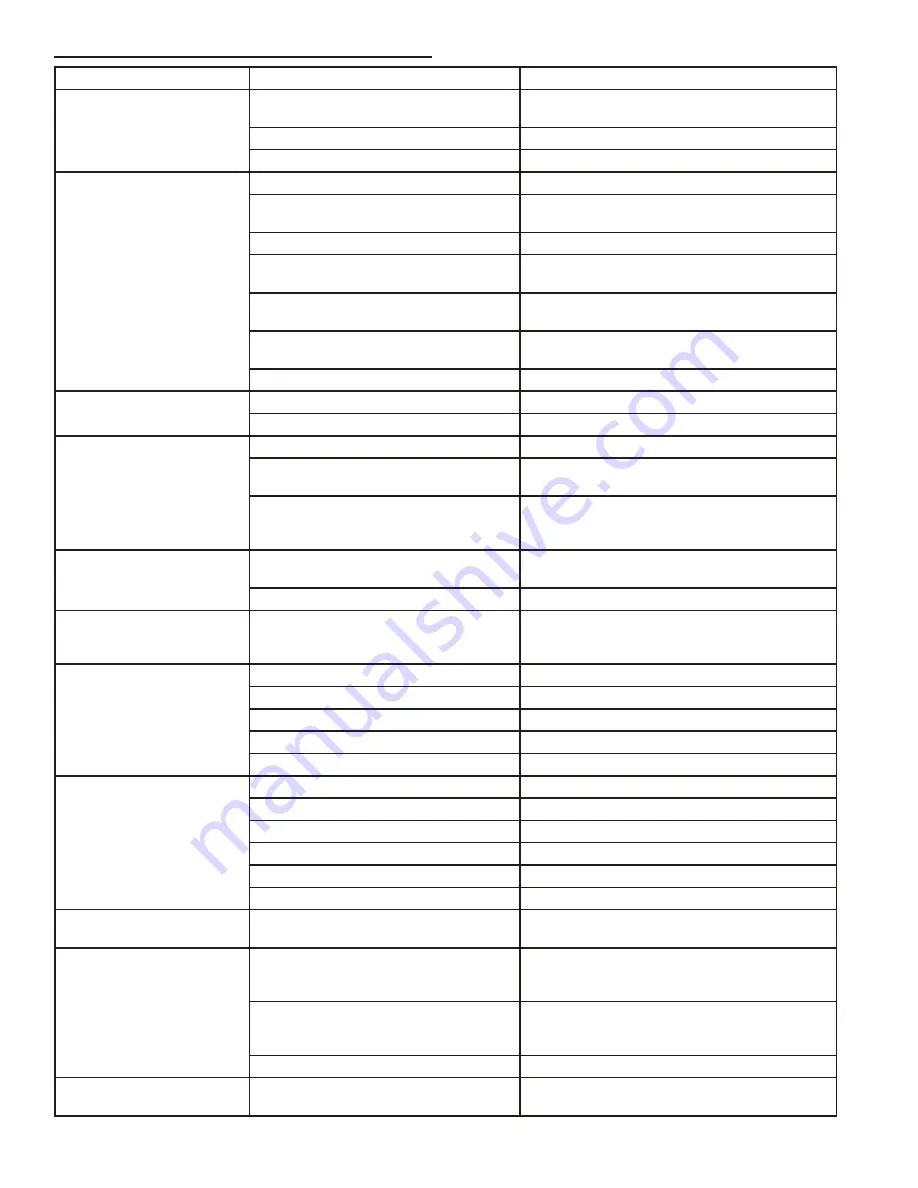
Problem
Cause
Correction
Water conditioner fails to
regenerate.
Electrical service to unit has been
interrupted
Assure permanent electrical service (check fuse,
plug, pull chain, or switch).
Timer is defective.
Replace timer.
Power failure.
Reset time of day.
Hard water.
By-pass valve is open.
Close by-pass valve.
No salt is in brine tank.
Add salt to brine tank and maintain salt level above
water level.
Injector screen plugged.
Clean injector screen.
Insufficient water flowing into brine tank.
Check brine tank fill time and clean brine line flow
control if plugged.
Hot water tank hardness.
Repeated flushings of the hot water tank is
required.
Leak at distributor tube.
Make sure distributor tube is not cracked. Check
O-ring and tube pilot.
Internal valve leak.
Replace seals and spacers and/or piston.
Unit used too much salt.
Improper salt setting.
Check salt usage and salt setting.
Excessive water in brine tank.
See "Excessive water in brine tank".
Loss of water pressure.
Iron buildup in line to water conditioner.
Clean line to water conditioner.
Iron buildup in water conditioner.
Clean control and add mineral cleaner to mineral
bed. Increase frequency of regeneration.
Inlet of control plugged due to foreign
material broken loose from pipes by recent
work done on plumbing system.
Remove piston and clean control.
Loss of mineral through drain
line.
Air in water system.
Assure that well system has proper air eliminator
control. Check for dry well condition.
Improperly sized drain line flow control.
Check for proper drain rate.
Iron in conditioned water.
Fouled mineral bed.
Check backwash, brine draw, and brine tank fill.
Increase frequency of regeneration. Increase
backwash time.
Excessive water in brine tank.
Plugged drain line flow control.
Clean flow control.
Plugged injector system.
Clean injector and screen.
Timer not cycling.
Replace timer.
Foreign material in brine valve.
Replace brine valve seat and clean valve.
Foreign material in brine line flow control.
Clean brine line flow control.
Softener fails to draw brine.
Drain line flow control is plugged.
Clean drain line flow control.
Injector is plugged.
Clean injector.
Injector screen plugged.
Clean screen.
Line pressure is too low.
Increase line pressure to 20 psi (1.3 bar).
Internal control leak
Change seals, spacers, and piston assembly.
Service adapter did not cycle.
Check drive motor and switches.
Control cycles continuously.
Misadjusted, broken, or shorted switch.
Determine if switch or timer is faulty and replace
it, or replace complete power head.
Drain flows continuously.
Valve is not programming correctly.
Check timer program and positioning of control.
Replace power head assembly if not positioning
properly.
Foreign material in control.
Remove power head assembly and inspect bore.
Remove foreign material and check control in
various regeneration positions.
Internal control leak.
Replace seals and piston assembly.
No hard water bypass
solenoid not operating
Incorrect power transformer.
Replace with 40VA transformer (P/N 61920-0X).
TROUBLESHOOTING
continued
22 •
FLECK
7000 NXT Service Manual
Содержание Fleck 7000 NXT
Страница 1: ...FLECK 7000 NXT SERVICE MANUAL...
Страница 28: ...DIMENSIONAL DRAWINGS 61500 7000XTR LNE Rev A 28 FLECK 7000 NXT Service Manual...
Страница 29: ...METER FLOW DATA TR18753 Softener TR18688 Filter 41140 02 Rev A 7000NXT VALVE FLECK 7000 NXT Service Manual 29...
Страница 30: ...INJECTOR FLOW DATA TR18755 Rev B 30 FLECK 7000 NXT Service Manual...