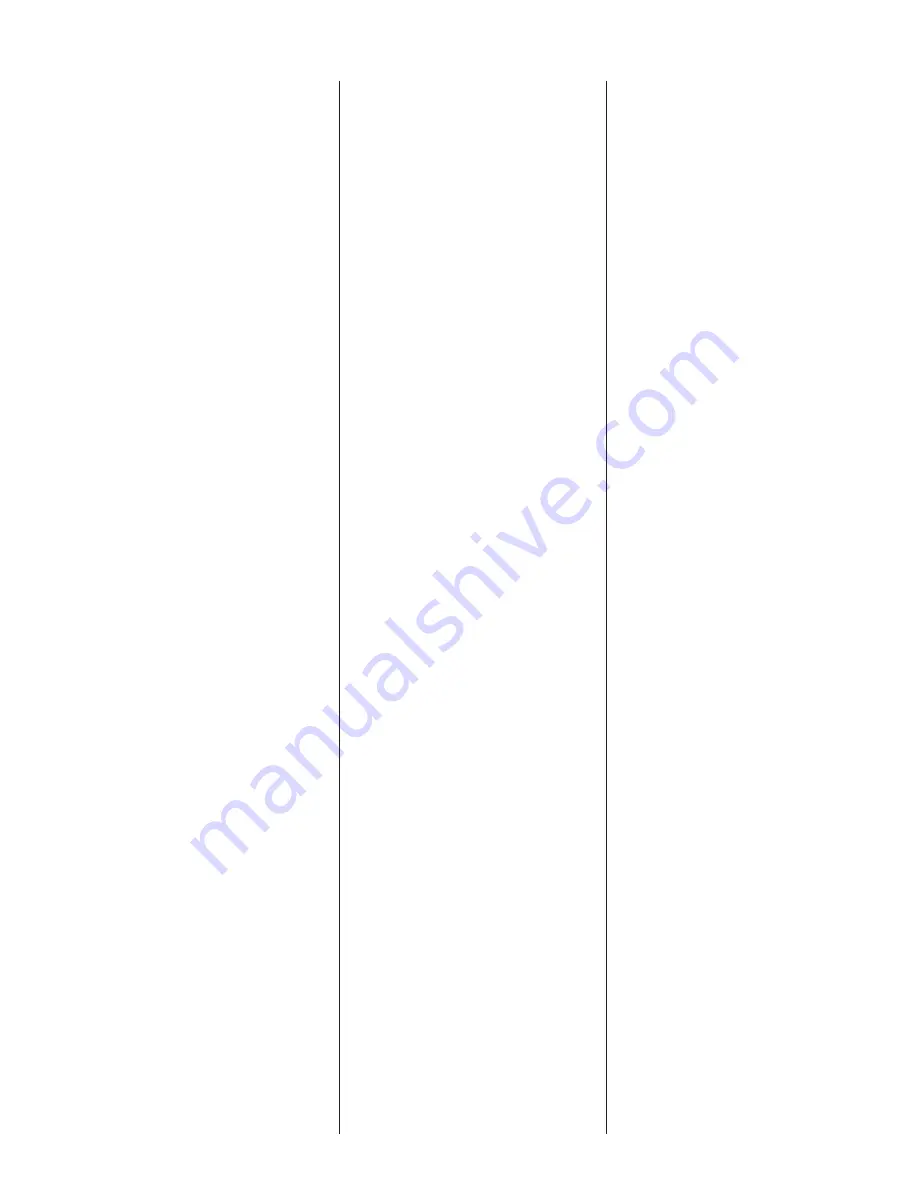
5
replacing bearings push only
on inner face. If a press is
not available, bearings can be
tapped on, using a sleeve that
bears only on the inner face.
Note: Never pound on the outer
face of the bearing. This will
cause bearing damage.
10.Push the new rotor shaft and
ball bearing assembly into the
seal plate. (Note that the
replacement rotor must be of
the same manufacture as the
existing stator, or vice versa.)
Reassemble the motor (20)
to the seal plate (13) with the
four long cap screws. Be sure
to tighten down the bolts
evenly and firmly to prevent
cocking of the stator. An
uneven assembly can cause the
rotor to rub the motor causing
the motor to short.
11. Press the new ceramic seal
(11) in place with the rubber
ring facing the impeller. This
should have a thin oil
(dielectric, same as in motor
housing) coating.
Note: Ceramic must be kept
clean. Any dirt will cause
seal failure.
12.Start the impeller (12) on the
shaft one to two turns; then,
add a drop of Loctite #277 to
the impeller threads and screw
the impeller hand tight. The
impeller will force the ceramic
seal into position. The shaft
should be free of dirt, grease,
etc., or the Loctite will not
hold as designed. On three
phase models only, replace
impeller washer (30) and
impeller screw (31) to the
shaft.
Note: Loctite overrun onto the
seal or bearing will result in
shaft seizure.
13.Remove the old seal ring (18)
and stretch on new ring with
O-ring lube.
Do not roll the ring onto seal
plate or water leakage into the
motor housing will result.
14.Fasten the ground wire (22)
inside the motor housing and
tuck wires up into the housing
to prevent rubbing on the rotor;
then assemble housing (21) to
volute (14) with bolts (6).
15.Check for seal leaks by
pressurizing the pump to 7 to 9
pounds of air pressure. Air
bubbles should appear at first
then stop. If air bubbles
continue, recheck seals.
Hydromatic pumps have a
small air vent hole in the
impeller cavity to let out
trapped air. If this hole
becomes plugged, pump may
air lock. To break the air
lock, use a small screwdriver
to clear hole in the impeller
cavity.
As a secondary precaution in
installations of this type, 1 ⁄ 16"
hole should be drilled in the
discharge pipe below the check
valve. The check valve should
be 12 to 18 inches above pump
discharge. Do not put check
valve directly into pump
discharge opening.
NOTE: In sumps where the
pump is operating daily, air
locking rarely occurs.
16.
Oil fill.
After air test is
satisfactory, remove unit from
water and wipe or blow off any
excess water.
Do not put oil in motor
with any water present in
motor cavity.
Fill oil to 1 ⁄ 8" over windings
in motor housing through
opening (11). Use oil fill tube
that will go into holes so that
air can escape. Replace plug
(3) and pump is ready for
operation. Use only high grade
transformer oil.
17.
Manual pumps.
All general
instructions for automatic
pumps apply to manual pumps
except the level switch is not
used and the power cord does
not have a vent tube.
Manual models have the
plug (3) in switch cap for
installing a fitting to air test
the pump for leaks. Replace
all plugs with Permatex on
threads. The switch housing
seat is tapped and plugged
with pipe plug.