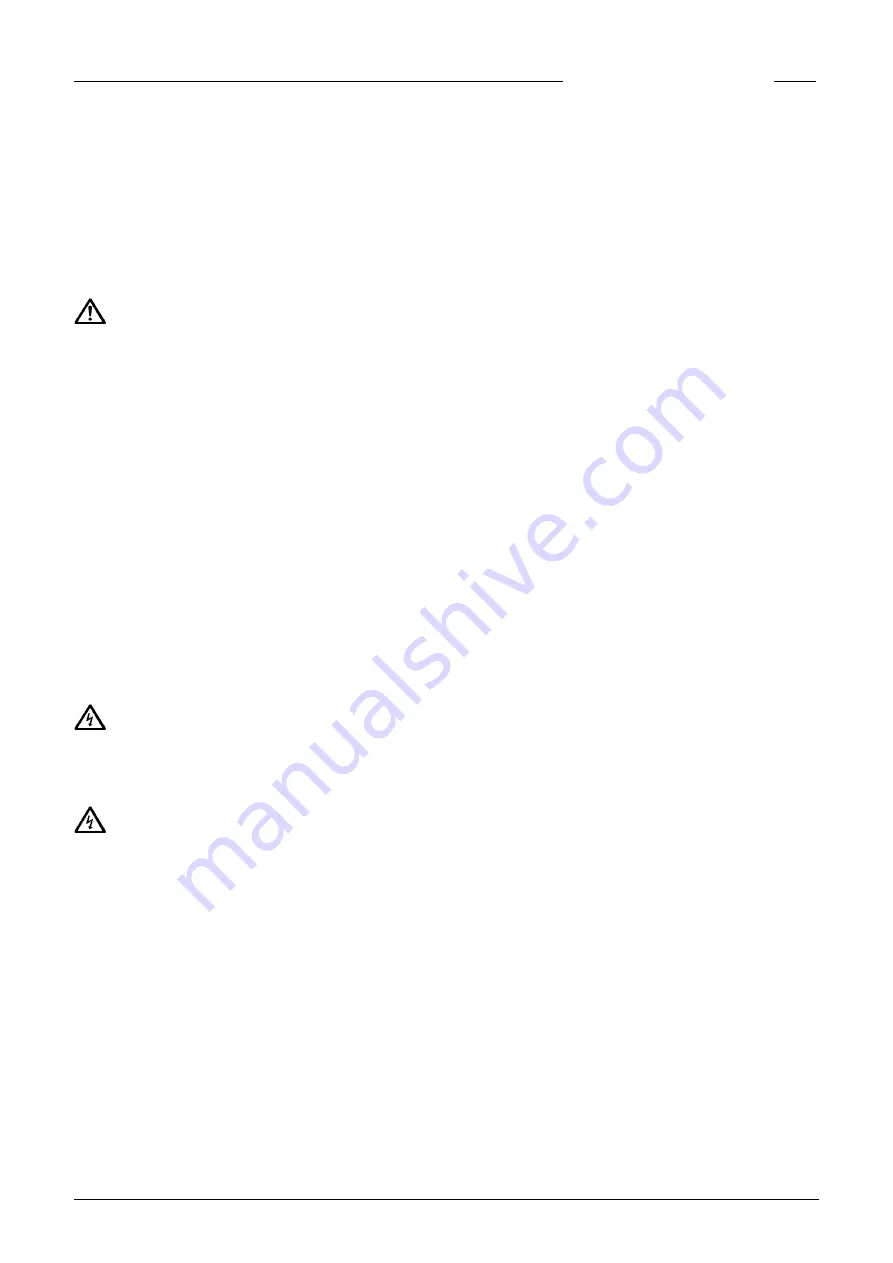
13
ENGLISH
Manual operation
Set the rocker switch to “Hand”. The pump will now operate in
continuous mode independently of the wastewater level. The
pumping out operation should therefore be observed through
the maintenance opening.
Shutting down
Set the rocker switch to “0”. This shuts down the pump. The
alarm system is still ready for use.
DANGER!
Do not use position “0” of the selector switch for repair and
maintenance work on the control unit and pump, but rather al-
ways unplug them from the mains or turn them off at the main
switch.
Inspection
To maintain operational reliability, carry out a visual inspection
of the lifting station, including the pipe connections, once a
month.
MAINTENANCE
Maintenance and inspection of this product must be carried
out in accordance with EN 12056-4.
To ensure continued reliability of service, we recommend that
you take out a service contract.
NOTICE!
Servicing and maintenance of the sewage lifting sta-
tion as well as repair work must be carried out by a qualified
technician at intervals of 3 months in industrial plants or 6
months in blocks of flats.
WARNING!
Before carrying out any work, unplug the lifting station from the
mains power supply or turn it off at the main switch and ensure
that the power supply to the lifting station cannot be switched
on again by anyone else.
WARNING!
Check the plug and the mains cable for signs of mechanical
and chemical damage. Damaged or kinked cables must be re-
placed.
We recommend that the following work is included in the ser-
vice:
1. Check the connection points for watertightness by inspect-
ing the areas surrounding the lifting station and the fittings.
2. Operate the sluice valves and check that they move easily.
Adjust and grease them if necessary.
3. Open and clean the swing-type check valve; check the seat
and ball (valve).
4. Clean the pump and the pipes where they connect to the
lifting station; check the impeller and the bearings.
5. Oil check. If necessary top up or carry out an oil change.
6. Clean the inside of the tank (as necessary, or if especially
required); remove any grease, for example.
7. Check the condition of the collecting tank.
8. Flush the system through with water once every 2 years.
9. Inspect the electrical section of the lifting station. The con-
trol unit itself is maintenance-free, but if a rechargeable
battery is fitted, then it should be checked regularly to en
-
sure that it is in good working order. To do so, unplug the
lifting station from the mains and lift the float of the level
controller slowly by hand and hold it there until a high-water
alarm is triggered. In addition, clean the float if necessary.
When all the maintenance tasks have been performed, carry
out a test run and then put the lifting station back into opera-
tion. The service must be documented, giving details of the
important data and of all the tasks carried out.
Oil check
First of all loosen the hexagon screws or Allen screws around
the pump and lift the pump off the duckfoot bend. The filling
and draining port of the oil reservoir is sealed off with a screw-
on drain plug labelled “Oil”. In order to check the mechanical
seal, the oil, including any residue, must be drained from the
oil reservoir and collected in a clean measuring container.
• If the oil is contaminated with water (milky), an oil change
must be carried out. Check again after a further 300 operating
hours, but at the very latest after 6 months!
• However, if the oil is contaminated with both water and pol-
lutants, then not only the oil must be replaced, but the me-
chanical seal as well. For monitoring the oil reservoir, it is also
possible to retrofit the electrode of our “DKG” seal leak control
device in place of the “DKG” screw plug.
Oil change
To ensure operational reliability, the first oil change should be
carried out after 300 operating hours, with further oil changes
carried out after every 1000 operating hours. If the number of
operating hours is very low, an oil change should still be carried
out at least once a year.
If wastewater with strongly abrasive constituents is being
pumped, oil changes should be carried out at correspondingly
shorter intervals.
Use HLP hydraulic mineral oil, viscosity class 22 to 46, e.g.
Nuto from ESSO or DTE 22, DTE 24, or DTE 25 from Mobil, to
replace the oil in the oil reservoir.
The quantity of oil required is 1000 cm³ for ...C1 pumps and
1700 cm³ for ...B5, ...B6 and ...C5 pumps.
NOTICE!
The oil reservoir must be filled with the specified
quantity of oil only. Overfilling will result in the pump being ren
-
dered inoperable.
QUICK TIPS FOR REMEDYING FAULTS
The lifting station does not work
•
Check the mains voltage, the fuse and the FI circuit breaker.
Replace defective fuses only with fuses with the same nomi-
nal value. If the fuse triggers again, call a qualified electri
-
cian or our service engineers.
•
The internal 2 A glass tube time delay fuse for the 230/12V
control transformer, the motor contactor and the 230V AC
power supply are faulty. Replace defective fuses only with
fuses of the same type and nominal value!
•
If the mains cable is damaged, it must be replaced by the
manufacturer only.
•
If the float switch is obstructed, close the inlet sluice valve,
open the maintenance cover and clear the blockage.
Содержание COMPLI 15100/2 B5
Страница 2: ...2 ...
Страница 43: ...43 compli 1500 ...
Страница 44: ...44 compli 2500 ...
Страница 45: ...45 ...
Страница 46: ...46 ...
Страница 50: ...50 BS 1016 PD BS 1620 PD ...
Страница 51: ...51 BS 1016 PD BS 1620 PD ...
Страница 52: ...52 Main switch BS 2532 PD ...
Страница 53: ...53 pot free contact optional YE YE GN YE GN GN RD RD BS 2532 PD ...