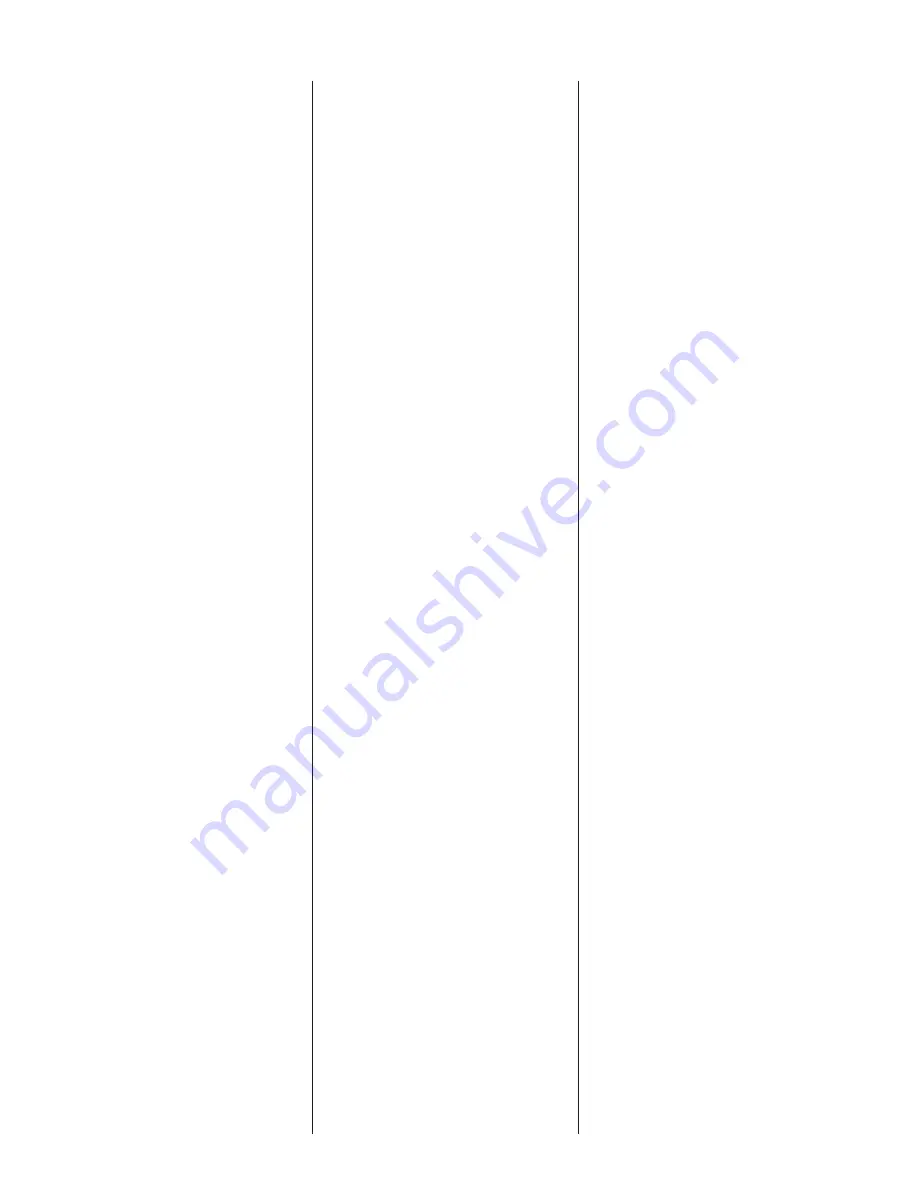
4
Pump Installations
Installing Pump in Sump:
Before installing pump in sump, lay
it on side and turn impeller manually.
Impeller may be slightly stuck due to
factory test water, so if stuck, then
it must be broken loose with small
bar or screwdriver in edge of vanes.
The impeller should turn freely.
Clean all trash and sticks from sump
and connect pump to piping.
A check valve must be installed on
each pump. A gate or plug valve in
each pump discharge line is also
recommended. This valve should
be installed on the discharge side
of the check valve so the line
pressure can be cut off if necessary
to service the check valve. Single
pump systems are sometimes
installed without a check valve
where it is de sir able to self-drain the
dis charge line to prevent freezing.
This can be done only with short
dis charge lines. Otherwise water will
return to the sump and cause short
cycling of the pump.
NEMA 4 Junction Box (Optional):
A NEMA 4 junction box should be
used to make power and control
con nec tions if electrical con trol
panel is to be set remote from the
pump sump. The Hydromatic NEMA
4 junc tion box is provided with
com pres sion con nec tors for sealing
all wires. No sealing compound is
need ed to make con nec tions wa ter
proof.
Wiring diagrams are provided with
panel for making connections. An
extra set of diagrams is included
so that one set can be used in the
sump when making connections.
The size wire to use from panel to
sump de pends on motor size and
distance in feet.
Be sure each wire is checked so
that a wrong connection will not be
made. An ohm me ter or Megger can
be used to check wire continuity.
Installing Switch Controls:
The controls are supported by a
mount ing bracket that is attached
to sump wall, cover or to the NEMA 4
junction box.
Cord snubbers are used to hold the
cord in place. Control level can be
changed at any time by loosening
the snubber and readjusting
cord length.
In either a simplex or duplex system,
the lower or turn-off control is set
just above the top of volute, so that
the volute will always be submerged
during the pumping cycle. The
second, or turn-on control, is set
about 24 inches above the lower
turnoff con trol.
More distance between turn-on and
turn-off controls can be used, but
sew age may become septic, and
excessive solids may collect for the
pump to handle. A frequent pumping
cycle is recommended for best
op er a tion.
If an alarm system is used, this
con trol is usually set about 6 inches
above the override control.
Some engineers, as described
pre vi ous ly, prefer to have the
alarm control set below the
override control.
Making Electrical
Connections:
All electrical wiring must be in ac-
cor dance with local codes, and only
competent electricians should make
the installations. Complete wiring
diagrams are glued to the inside
cover of the panel, and an additional
set of prints is included for use in
making the installation. All wires
should be checked for grounds
with an ohm me ter or Megger after
the connections are made. This is
important, as one grounded wire
can cause considerable trou ble.
IMPORTANT: If equipment is not
properly wired and pro tect ed as
recommended, the warranty is void.
Caution: The 230 volt 3 phase pump
has a dual marked nameplate.
Voltage may be rewired by the
manufacturer or a Class I Div 1
equipment qualified electrician.
Once the voltage is changed, the
factory cord tag indicating 230 volt
3 phase must be removed.
For record keeping purposes,
we suggest the pump be marked
externally with the new voltage and
qualified personnel that performed
the change. Pumps shipped from
the factory as 460 volt 3 phase
cannot be rewired to any other
voltage.
To Re-wire the pump from
230V to 460V 3 phase:
Only a 230V pump from the factory
is considered dual voltage, a cord
label clearly states the factory
wound voltage.
Remove bolts securing cord
assembly then raise the cord cap
assembly enough to slip a prying
instrument on opposite sides
between the cord cap casting and
the junction box. Take care to not
damage the o-ring or the machined
surfaces of the castings. Doing so
could void FM agency certifications.
While prying evenly on both sides;
separate the cord cap casting from
the motor housing, the assembly
is airtight and will have a vacuum
effect when disassembling. Once
separated, the cord cap can be
inverted and rotated to the outside
of the pump assembly, and a bolt
can be re-used to secure the upside
down cord cap to the motor housing
for ease of rewiring.
Refer to the wiring diagram within
this manual for wiring details.
Once all electrical connections
are finished and secure (a crimped
electrical connector is best to
prevent issues due to vibration if
Содержание S3R
Страница 9: ...9 Wiring Diagrams...