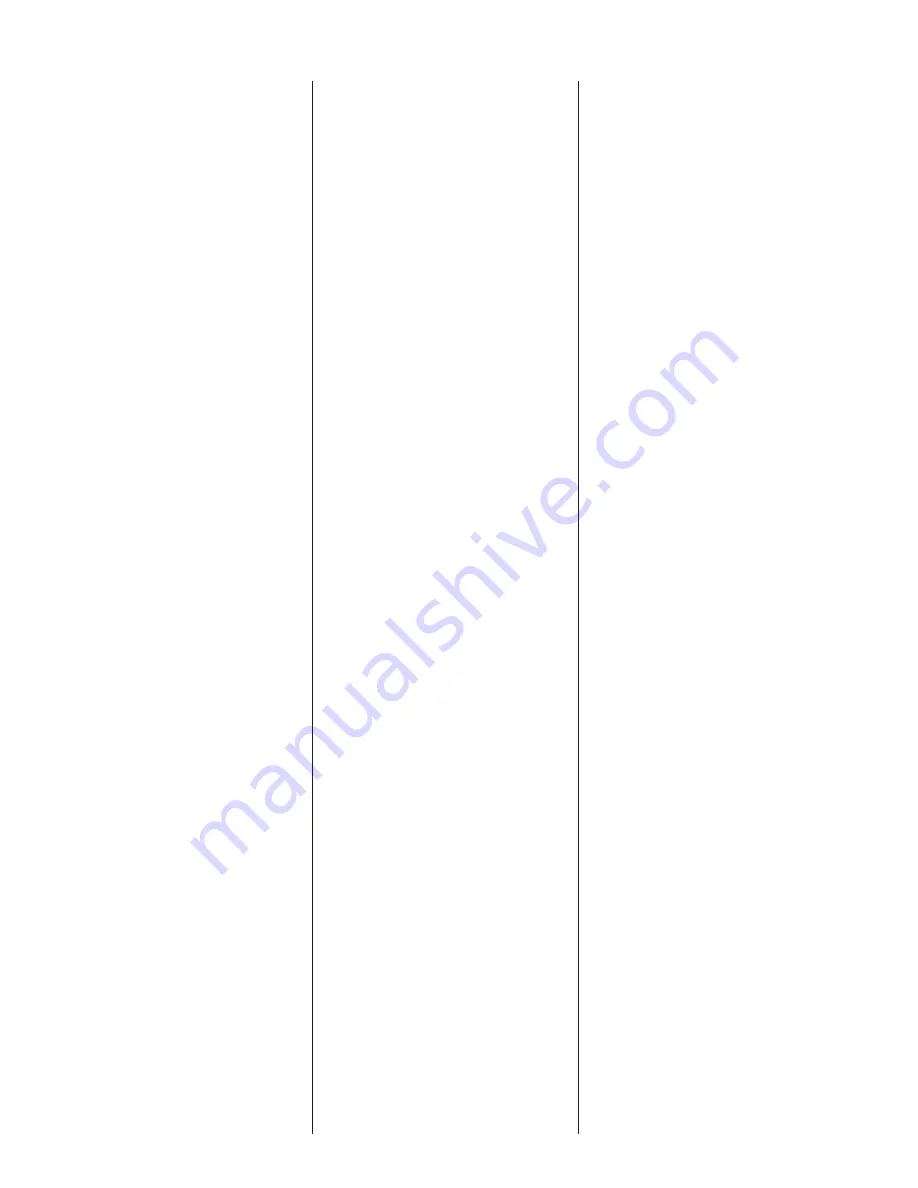
8
Pump
Troubleshooting
Below is a list of common problems
and the probable causes:
Pump will not start:
1. No power to the motor.
Check for blown fuse or open
circuit break er.
2. Selector switch may be in the
Off position.
3. Control circuit transformer
fuse may be blown.
4. Overload heater on starter
may be tripped. Push to reset.
Pump will not start and overload
heaters trip:
1. Turn off power and check
motor leads with Megger or
ohmmeter for possible ground.
2. Check resistance of motor
wind ings. All 3 phases should
show the same reading.
3. If no grounds exist and the
motor windings check OK,
remove pump from sump
and check for clogged or
blocked impeller.
Pump operates with selector
switch in Hand position but will
not operate in Auto position:
1. This indicates trouble in
the float level control or the
alternator relay.
2. Check the control panel.
Pump runs but will not shut off:
1. Pump may be air locked. Turn
pump off and let set for several
minutes, then restart.
2. Lower float control may be
hung-up in the closed position.
Check in sump to be sure con-
trol is free.
3. Selector switch may be in the
Hand position.
Pump does not deliver proper
capacity:
1. Discharge gate valve may
be partially closed or
partially clogged.
2. Check valve may be partially
clogged. Raise level up and
down to clear.
3. Pump may be running in wrong
direction. Low speed pumps
can operate in reverse di-
rec tion with out much noise
or vibration.
4. Discharge head may be
too high. Check total head
with gauge when pump is
operating. Total head is
dis charge gauge pressure
converted to feet plus vertical
height from water level in
sump to center line of pressure
gauge in discharge line. Gauge
should be installed on pump
side of all valves. Multiply
gauge pressure in pounds by
2.31 to get head in feet.
5. If pump has been in service for
some time and capacity falls
off, remove pump and check
for wear or clogged impeller.
Motor stops and then restarts
after short period but overload
heaters in starter do not trip:
1. This indicates heat sensors in
the motor are tripping due to
ex ces sive heat. Impeller may
be par tial ly clogged giving a
sustained overload but not
high enough to trip overload
heat er switch.
2. Motor may be operating out
of liquid due to a failed level
control. All Hydromatic
®
S3R sub mers ible motors
can operate for extended
periods out of water without
burning up the winding, but
the heat sensors give motor
prolonged life by controlling
winding temperature.
3. Pump may be operating on a
short cycle due to sump being
too small or from water
re turn ing to sump due to a
leaking check valve.
Содержание S3R
Страница 9: ...9 Wiring Diagrams...