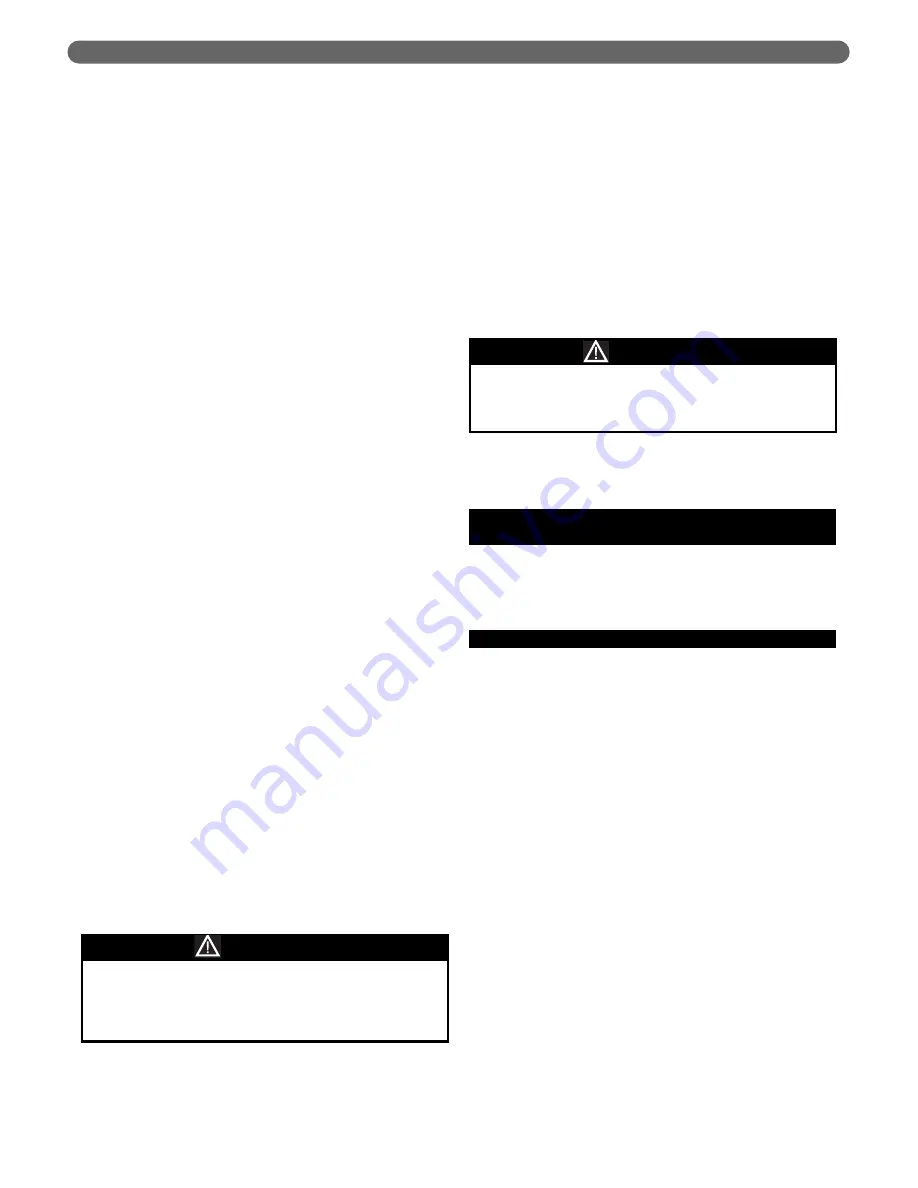
51
MAINTENANCE
b. Disconnect the condensate piping from the outside
connections (not from the Series PBC™ side) so
the flow can be observed.
c. Disconnect compression nut on gas valve inlet
and disconnect the gas valve electrical connector.
d. Remove the four 10 mm nuts from the burner
plate assembly. Disconnect wire leads to the spark
igniter and flame sensor. Disconnect two Molex
plugs from blower motor.
e. Pull the entire burner plate towards you to access
the heat exchanger coils.
f.
Significant deposits may be caused by the
recirculation of exhaust gasses, poor fuel quality or
contamination of the air supply. Review Section 3,
Venting & Air Inlet Piping, if deposits are evident.
2. Using a spray bottle filled with the recommended
product “Rydlyme” or “CLR”, spray liberally on the
coils, making sure the solution penetrates and funnels
down through the condensate hose. If the condensate
hose is blocked, let the chemical penetrate for at least
15 minutes or until it drains.
3. Use the nylon or brass brush (do not use steel) and
scrub coils to remove any buildup, then vacuum the
debris from the coils.
4. Spray coils with clear water, making sure to confine
the spray to the area being cleaned (try to avoid
wetting the back ceramic wall of the unit). Flush the
combustion chamber with fresh water. At this point,
the Series PBC™ should be ready to power back up.
5. Reinstall the burner plate assembly using the
following steps:
a. Inspect the inside of the heat exchanger for dirt
and debris.
b. Install the burner plate assembly and replace the
four 10 mm nuts.
c. Reconnect the wire leads to the spark igniter,
flame sensor and gas valve. (Be sure that the
spark igniter is connected to the lead with the
large insulated connection boot.) Reconnect two
Molex plugs on blower motor.
d. Connect the compression nut on the gas valve
inlet and reattach the gas valve electrical
connector.
e. Reset thermostats.
(IMPORTANT: BE SURE
THAT THE VENT CONNECTION IS NOT
BLOCKED.)
f.
Turn the power to the Series PBC™ on. Observe
the display module to assure proper operation.
g. Initiate a call for heat** and observe the
condensate flow.
h. Reconnect the condensate piping to the drain
connection.
**NOTE: When firing the boiler the first few
times you may experience some fluttering
of the gas burner that may result in a flame
lockout. This is normal and will require you
to recycle the unit until this clears up. This
is caused by water still present in the
combustion chamber.
6. Inspect exhaust vent and air intake vents for proper
support and joint integrity. Repair as necessary. Refer
to Section 3, Venting & Air Inlet Piping.
7. Inspect exhaust vent and air intake vent terminations
for obstructions or corrosion. Corrosion is an
indication of exhaust gas recirculation.
F.
HEAT EXCHANGER GASKET
REPLACEMENT
If at any point the silicon burner door gasket shows signs
of damage or after two years of operation it needs to be
replaced. Inspection during annual cleaning is the best
time to check and replace this gasket.
G. FLOW RESTRICTOR MAINTENANCE
The Series PBC™ has a 4.75 GPM flow restrictor installed
inside the CHB block that contains a screen filter. This
filter protects the plate heat exchanger from sediment
infiltration that would be large enough to become stuck
inside the plate heat exchanger passages. This filter should
be checked and flushed clean on an annual basis. More
frequent cleaning might be required in poor water areas.
The following steps can be taken to clean or replace the
flow regulator:
1. Power off the boiler.
2. Isolate the unit from the main domestic water supply
of the dwelling and remove pressure on the Domestic
side of the unit.
3. The flow regulator is located below the flow sensor on
the right half of the CHB unit, immediately left of the
pump. Insert a small screw driver into the rounded
tab or use a pair of pliers to turn the regulator
housing counter-clockwise.
4. When the locking tab are in line with the openings in
the main housing, pull the flow regulator housing out
of the CHB body.
5. The flow regulator is the small white cartridge inside
of the housing. It can be removed by pushing it out of
the housing.
It is extremely important to check for leaks when
reconnecting the gas valve. Failure to do so may
result in severe personal injury, death or major
property damage.
WARNING
Leaks in the vent system will cause products of
combustion to enter structure (vent system operates
under positive pressure).
WARNING
Содержание PBC-34
Страница 1: ...PBC Gas Boilers PBC 34 PBC 40 PBC 52 Combination Installation Operation Maintenance Manual Series...
Страница 22: ...20 WATER PIPING AND CONTROLS Figure 4 6 Recommended Central Heat Piping...
Страница 23: ...21 Figure 4 7 Recommended Domestic Hot Water Piping WATER PIPING AND CONTROLS...
Страница 31: ...29 Figure 7 2 Wiring Schematic and Connection ELECTRICAL CONNECTIONS...
Страница 45: ...E LIGHTING OPERATING PROCEDURES 43 START UP PROCEDURE...
Страница 57: ...THIS PAGE INTENTIONALLY LEFT BLANK...
Страница 60: ...58 REPAIR PARTS Figure 13 2 PBC 34 Combustion Components...
Страница 62: ...60 REPAIR PARTS Figure 13 3 PBC 40 and PBC 52 Combustion Components...