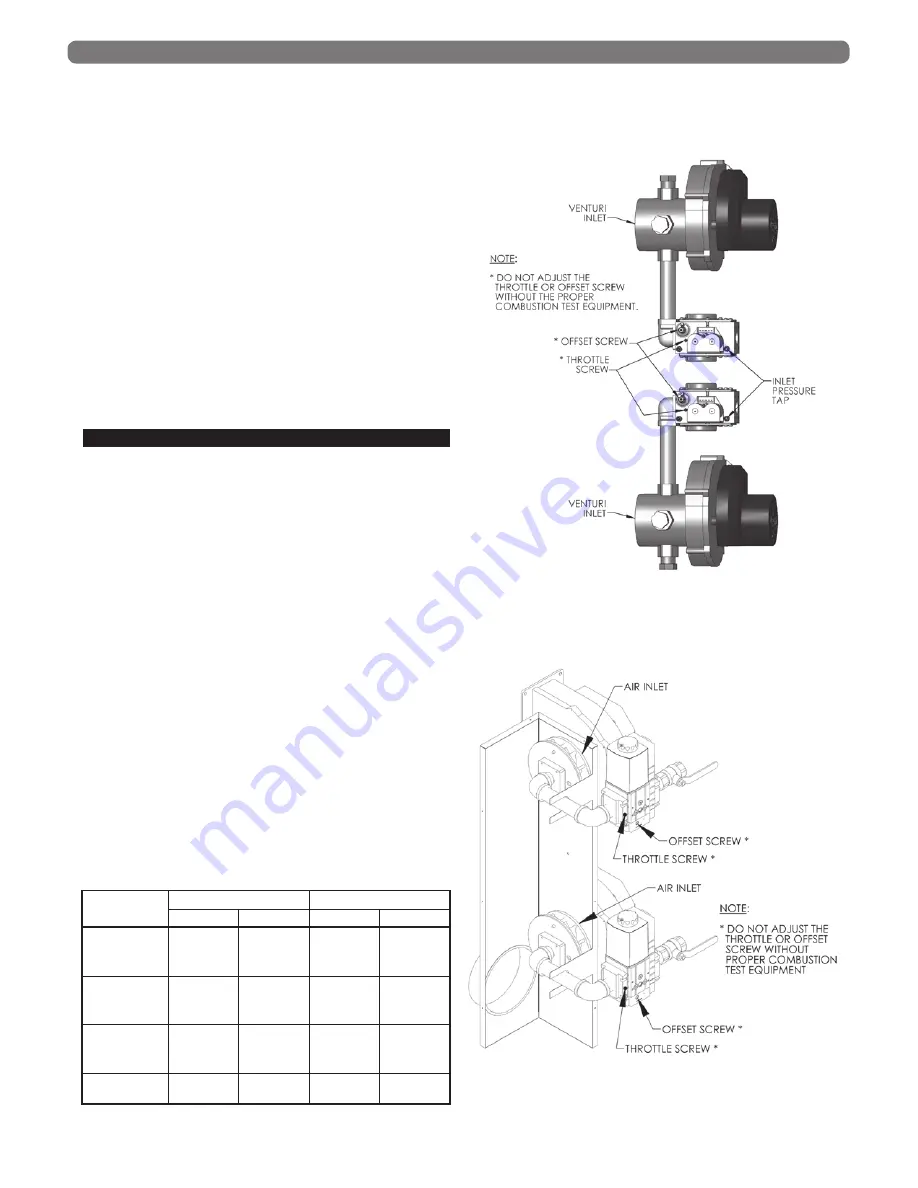
27
l. Turn on the gas shutoff valve and the boiler
service switch.
m. Start the boiler and check for fuel gas odor around
the gas valve. If an odor is evident, check to make
sure that the pressure tap fitting is closed.
n. Repeat this procedure on the second gas valve.
4. All gas piping must be leak tested prior to placing the
boiler in operation.
a. If the required leak test pressure is higher than 26
in. w.c., the boiler must be isolated from the gas
supply piping by closing the service valve.
b. If the gas valve is exposed to pressure exceeding
26 in. w.c., the gas valve must be replaced.
5. Install the boiler such that the gas ignition system
components are protected from water (dropping,
spraying, rain, etc.) during operation and service
(circulator replacement, condensate collector and
neutralizer clean out, control replacement, etc.).
E. MAIN GAS VALVES - OPERATION
1. Figure 5.2 is an illustration of the main gas valve,
venturi and blower assembly for the
P
ure
F
ire
®
boiler.
2. Do not make adjustments to the gas valve without
instrumentation to measure carbon dioxide (CO
2
) and
carbon monoxide (CO) emissions in the exhaust vent
pipe.
3. Turning the throttle screw clockwise will decrease
the gas flow (decreasing CO
2
) and turning it
counterclockwise will increase the gas flow rate
(increasing CO
2
). Markings adjacent to the throttle
screw show + and – indicating this operation.
a. Throttle adjustments should be made only at full
input rate with the other burner off.
b. The exhaust emissions should be checked with
both burners in operation to assure correct
operation.
c. See Section 9, Start-Up Procedure for specific
information about commissioning and adjusting
the boiler.
4. The recommended CO2 settings are given in table
5.5. In no case should the boiler be allowed to
operate with CO emissions higher than 200 ppm.
5. Refer to Section 3, Venting and Air Inlet Piping for
information on obtaining exhaust vent samples from
this boiler.
FUEL PIPING
Figure 5.2: Gas Valve, Venturi, Blower Assembly –
PFC-850/1000
Figure 5.3: Gas Valve, Venturi, Blower Assembly –
PFC-1500
Natural Gas
Propane (LP)
Low Fire
High Fire
Low Fire
High Fire
Carbon
Monoxide
(CO)
< 50 ppm < 200 ppm < 50 ppm < 200 ppm
Carbon
Dioxide
(CO
2
)
8.8% to
10.0%
8.5% to
9.5%
9.8% to
11.0%
9.5% to
10.5%
Excess
Oxygen
(O
2
)
3.4% to
5.4%
4.2% to
6.0%
4.2% to
6.0%
4.9% to
6.5%
Excess Air
17.3% to
31.0%
22.4% to
35.8%
22.4% to
35.8%
27.3% to
40.1%
Table 5.5: Combustion Settings
Содержание PUREFIRE PFC-1000
Страница 1: ...PUREFIRE Boilers PFC 850 PFC 1000 PFC 1500 Gas Installation Operation Maintenance Manual ...
Страница 23: ...21 WATER PIPING CONTROLS Figure 4 4 Recommended Piping One Boiler with Multiple CH Zones One DHW Tank ...
Страница 24: ...22 WATER PIPING CONTROLS Figure 4 5 Recommended Piping Multiple Boilers with Multiple CH Zones One DHW Tank ...
Страница 62: ...60 START UP PROCEDURE J LIGHTING OPERATING INSTRUCTIONS Figure 9 1 Lighting Operating Instructions ...
Страница 80: ...78 REPAIR PARTS Figure 13 3a Jacket Assembly PFC 850 1000 Figure 13 3b Jacket Assembly PFC 1500 ...
Страница 82: ...80 Figure 13 4 Control System REPAIR PARTS ...
Страница 84: ...82 Figure 13 5 Condensate System REPAIR PARTS ...
Страница 89: ...87 APPENDIX B BURNER LCD STATUS SCREENS CH Burn Cycle DHW Burn Cycle Special Functions DHW Tank Warm Hold ...
Страница 90: ...88 APPENDIX C USER MENU APPENDIX C USER MENU Figure C 1 User Menu Managing Burner ...
Страница 91: ...89 APPENDIX C USER MENU Figure C 1 User Menu Dependent Burner ...
Страница 92: ...90 APPENDIX D INSTALLER MENU STRUCTURE APPENDIX D INSTALLER MENU STRUCTURE ...
Страница 93: ...91 APPENDIX D INSTALLER MENU STRUCTURE ...
Страница 95: ...93 SERVICE LOG SERVICE LOG Date Serviced By Description of Service Serial Number ...
Страница 96: ...94 NOTES ...
Страница 97: ...95 NOTES ...