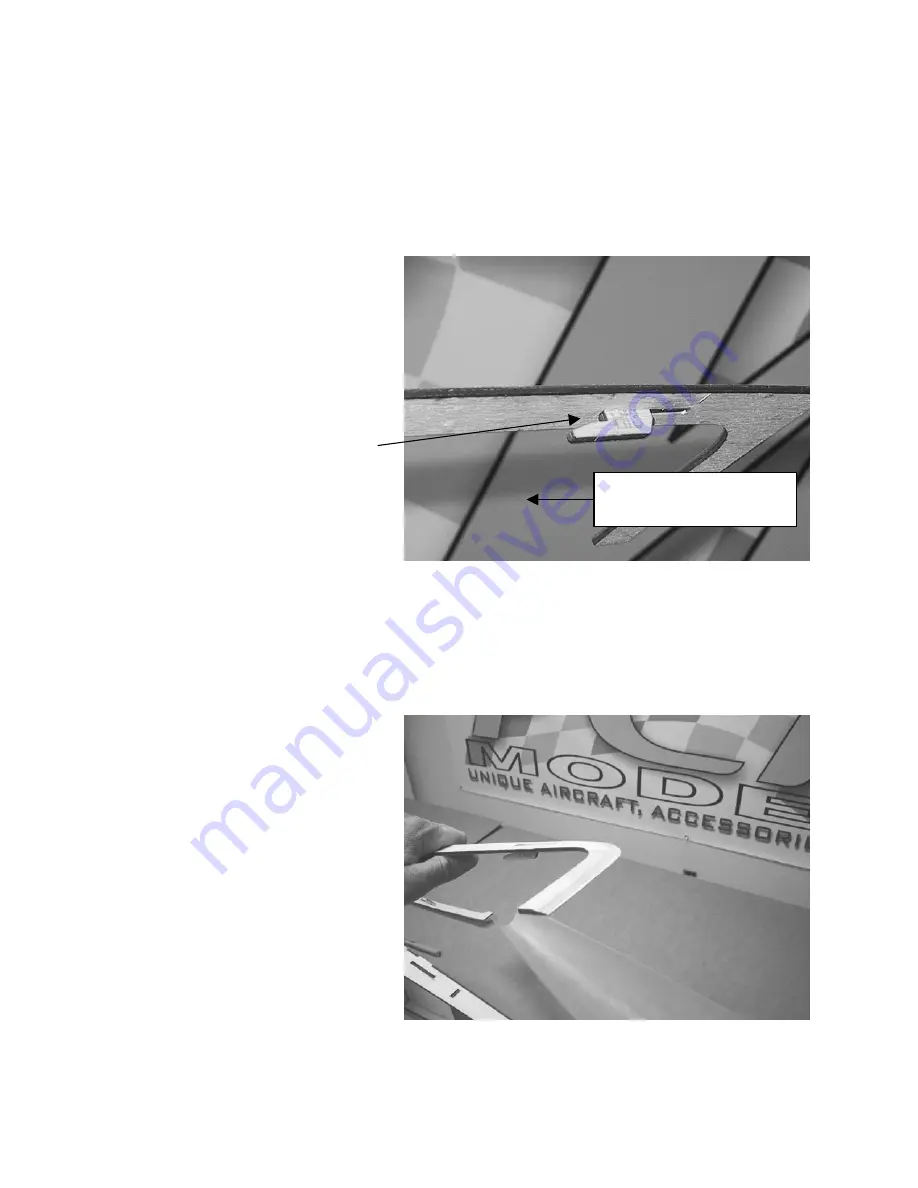
Installing the Canopy Hatch
The hatch, when completed, slides into place by utilizing six hook like fixtures on the
bottom of the canopy structure. Familiarize your self with the shape and location of these
fixtures to get a good idea as to the orientation of all parts involved.
Begin by locating the six HF6
formers and the two HF2 formers.
Use a piece of scrap ply of the
same thickness as the fuselage
sides as a gage to place one of the
HF6 formers into a slot in former
HF2. You will want HF6 to be
glued into position such that the
gage is a tight fit between the gap
of the HF6 and HF2. Use thin or
medium CA to glue the pieces
together.
Repeat for the other five HF6s and
make sure of the orientation, they
should all point forward.
Canopy Hooks should
face forward.
Once completed you will have two separate sections of the hatch, each with three hooks
for securing the hatch to the body of the model. Try placing each of the sections into
position and the sliding it forward. It should slide forward 5/8ths of an inch and be fairly
tight the first time or two that you try.
When you slide both sections into
position they should line up
equally at the ends and just touch
at the three positions across the
model. This is what you are aiming
for. If one section is too tight, try
to find the suspect hook that is
holding back and
slightly
file some
material off of the
top
of the hook.
When both sections meet the
above criteria, you may now place
the fiberglass canopy hatch over
the structure and take note of any
areas where the ply structure needs
to be sanded to allow for a good fit.
18