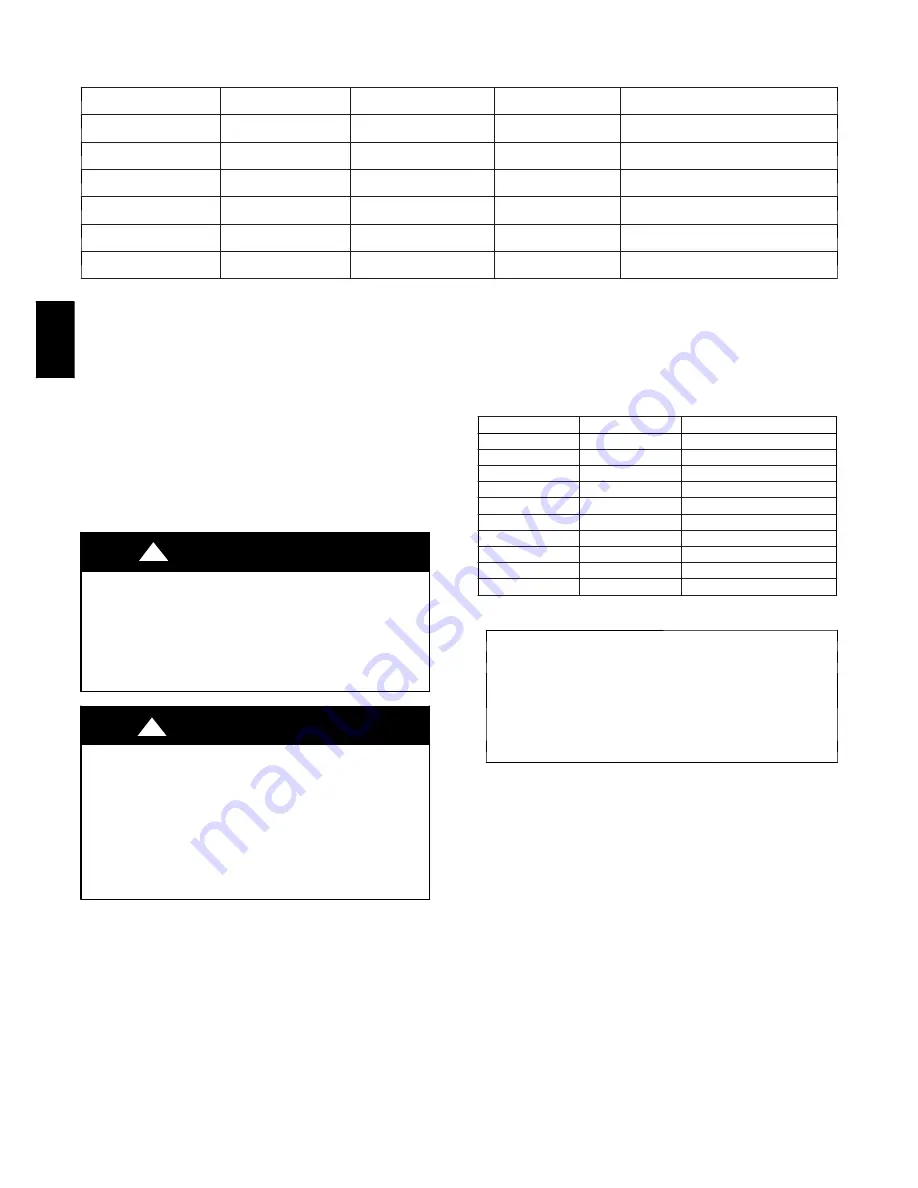
34
CAUTION!! FOR THE FOLLOWING APPLICATIONS, USE THE MINIMUM VERTICAL VENT HEIGHTS AS SPECIFIED
BELOW.
FOR ALL OTHER APPLICATIONS, FOLLOW EXCLUSIVELY THE NATIONAL FUEL GAS CODE.
FURNACE
ORIENTATION
VENT
ORIENTATION
FURNACE
INPUT(BTUH/HR)
MINIMUM VENT
DIAMETER (IN.)*
MINIMUM VERTICAL VENT
HEIGHT (FT.)**
Downflow
Vent elbow left, then
up Fig. 36
154,000 132,000
110,000(036/---12 only)
5
12
Horizontal Left
Vent elbow right,
then up Fig. 39
154,000 132,000
5
7
Horizontal Left
Vent Elbow up Fig.
40
154,000 132,000
5
7
Horizontal Left
Vent elbow right Fig.
41
154,000
5
7
Downflow
Vent elbow up then
left Fig. 34
110,000 (036/---12 only)
5
10
Downflow
Vent elbow up, then
right Fig. 37
110,000 (036/---12 only)
5
10
* 4 in. inside casing or vent guard
** Including 4 in. vent section (s)
NOTE:
All vent configurations must also meet National Fuel Gas Code venting requirements NFGC
8.
Secure vent connector to furnace elbow with (2) corrosion--res-
istant sheet metal screws, spaced approximately 180
°
apart.
9.
Secure all other single wall vent connector joints with (3) corro-
sion resistant screws spaced approximately 120
°
apart. Secure
Type--B vent connectors per vent connector manufacturer’s re-
commendations.
10.
The total height of the vent and connector shall be at least seven
ft. for the 154,000 Btuh gas input rate model when installed in a
downflow application with furnace elbow turned to left side with
the connector elbow outside furnace casing pointing upward.
(See Fig. 36.)
Step 3
—
Adjustments
FIRE HAZARD
Failure to follow this warning could result in injury, death
and/or property damage.
DO NOT bottom out gas valve regulator adjusting screw.
This can result in unregulated manifold pressure and result
in excess overfire and heat exchanger failures.
!
WARNING
FURNACE DAMAGE HAZARD
Failure to follow this caution may result in reduced furnace
life.
DO NOT redrill orifices. Improper drilling (burrs, out--of
round holes, etc.) can cause excessive burner noise and
misdirection of burner flames. This can result in flame
impingement of heat exchangers, causing failures. (See Fig.
48.)
CAUTION
!
Furnace gas input rate on rating plate is for installations at
altitudes up to 2000 ft. Furnace input rate must be /--2
percent of furnace rating plate input.
1. Determine the correct gas input rate.
In the U.S.A.:
The input rating for altitudes above 2,000 ft. must be redu-
ced by 4 percent for each 1,000 ft. above sea level. For
installations below 2000 ft., refer to the unit rating plate.
For installations above 2000 ft., multiply the input on the
rating plate by the derate multiplier in Table 8 for the cor-
rect input rate.
In Canada:
The input rating must be derated by 10 percent for alti-
tudes of 2,000 ft. to 4,500 ft. above sea level by an autho-
rized Gas Conversion Station or Dealer. To determine cor-
rect input rate for altitude, see example 1 and use 0.90 as
derate multiplier factor.
TABLE 8—ALTITUDE DERATE MULTIPLIER FOR
U.S.A.
ALTITUDE
PERCENT
DERATE MULTIPLIER
(FT.)
OF DERATE
FACTOR*
0–2000
0
1.00
2001–3000
8–12
0.90
3001–4000
12–16
0.86
4001–5000
16–20
0.82
5001–6000
20–24
0.78
6001–7000
24–28
0.74
7001–8000
28–32
0.70
8001–9000
32–36
0.66
9001–10,000
36–40
0.62
* Derate multiplier factors are based on midpoint altitude for altitude
range.
EXAMPLE 1:
88,000 BTUH INPUT FURNACE INSTALLED AT 4300 FT.
Furnace Input
Rate at Sea Level
X Derate Multiplier
Factor
=
Furnace Input
Rate at
Installation
Altitude
88,000
X
0.90
=
79,200
2. Determine the correct orifice and manifold pressure adjust-
ment. There are two different orifice and manifold adjust-
ment tables. All models in all positions, except Low NOx
models in downflow or horizontal positions, use Table 12
(22,000 Btuh/Burner).
Low NOx models in the downflow or horizontal positions
must use Table 13 (21,000 Btuh/Burner). See input listed
on rating plate.
a. Obtain average yearly gas heat value (at installed alti-
tude) from local gas supplier.
b. Obtain average yearly gas specific gravity from local
gas supplier.
c. Find installation altitude in Table 12 or 13.
d. Find closest natural gas heat value and specific gravity
in Table 12 or 13.
e. Follow heat value and specific gravity lines to point of
intersection to find orifice size and manifold pressure
settings for proper operation.
f. Check and verify burner orifice size in furnace.
NEVER ASSUME ORIFICE SIZE. ALWAYS
CHECK AND VERIFY.
PG
8J
/M
Содержание PG8J
Страница 36: ...36 A08411 Fig 46 Wiring Diagram PG8J M ...