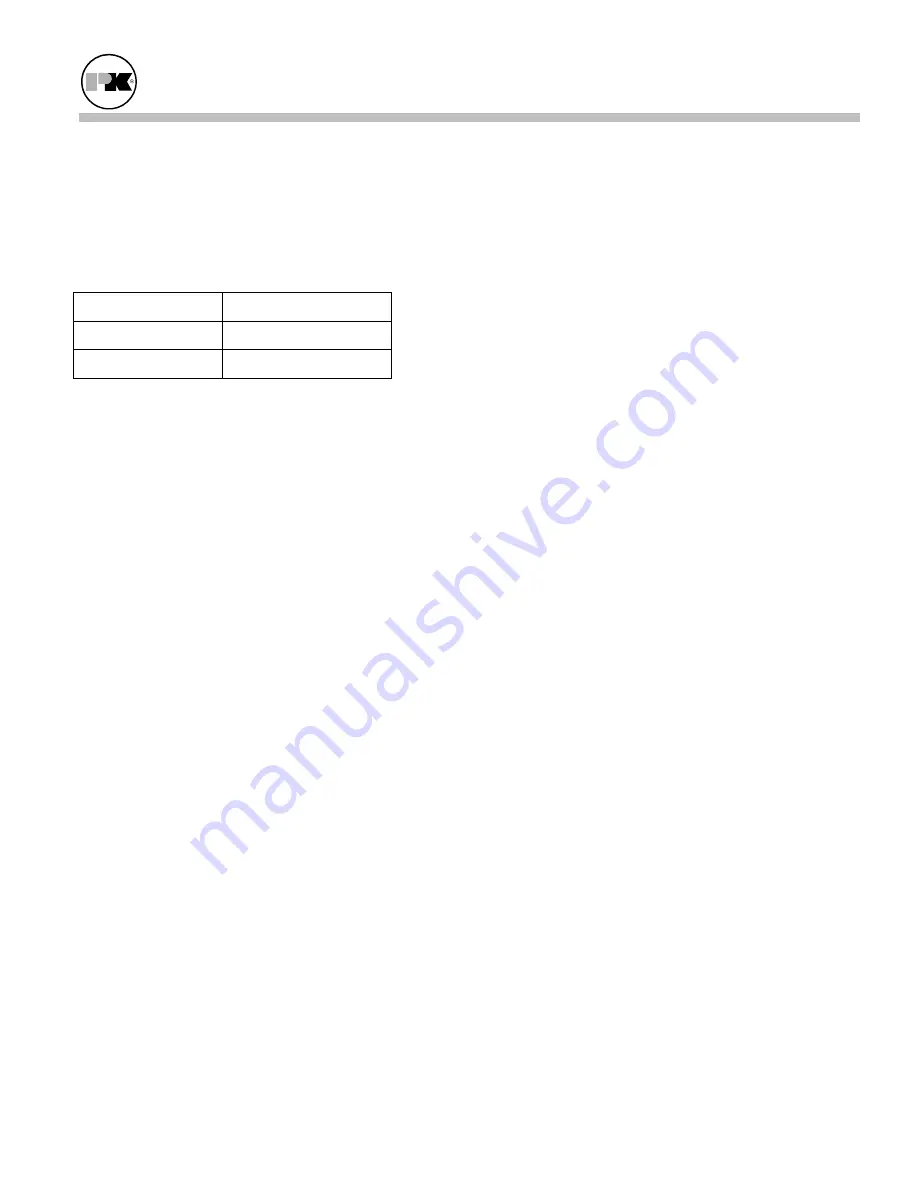
MACH® Series
Gas-Fired Boiler
Installation
Page 12
3.6.8 Intake Duct Materials and Sizes:
Material: PVC, CPVC, single wall galvanized steel, or
other suitable materials.
The intake duct must be sized for a pressure drop as
indicated in paragraph 3.6.7 and for the SCFM as
specified below.
Boiler Size
Required SCFM
1500 350
2000 467
The installation of a bird screen on the intake
termination is recommended. Ensure that the screen
does not become blocked with snow, ice, etc.
3.6.9 Sealing the Intake Duct
Proper sealing of the intake ductwork is necessary to
prevent infiltration of air from conditioned space.
Joints in PVC or CPVC must be cemented. For
galvanized duct, wrap each joint and seam with
adhesive aluminum tape.
3.6.10 Intake Duct Connection to Boiler
Connect the air supply duct to the 10” OD collar on
the top of the boiler. Fasten the duct to the collar with
sheet metal screws at 90º angles. Seal the joint.
3.6.11 Venting for Multiple Boilers
The venting instructions in this manual apply to a
single
boiler.
Venting systems for multiple boilers must be
designed by qualified professionals and verified by
the stack manufacturer. The venting system must
prevent backflow of exhaust gas through idle
boilers which are not operating.
3.6.12 Removing an Existing Boiler
(from a common venting system)
When an existing boiler is removed from a common
venting system, the common venting system is likely
to be too large for proper venting of the appliances
remaining connected to it.
At the time of removal of an existing boiler, while the
other appliances remaining connected to the common
venting system are not in operation, the following
steps should be followed with each appliance
remaining connected to the common venting system
placed in operation:
1. Seal any unused openings in the common venting
system.
2. Visually inspect the venting system for proper
size and horizontal pitch and determine that there
is no blockage or restriction, leakage, corrosion
or other deficiency which could cause an unsafe
condition.
3. Insofar as is practical, close all building doors
and windows and all doors between the space in
which the appliances remaining connected to the
common venting system are located and other
spaces of the building. Turn on clothes dryers
and any appliances not connected to the common
venting system. Turn on any exhaust fans, such
as range hoods and bathroom exhausts, so they
will operate at maximum speed. Do not operate a
summer exhaust fan. Close fireplace dampers.
4. Place the appliance being inspected in operation.
Follow the lighting instructions. Adjust the
thermostat so that the appliance will operate
continuously.
5. Test for spillage at the draft hood relief opening
after 5 minutes of main burner operation. Use the
flame of a match or candle or smoke from a
cigarette, cigar or pipe.
6. After it has been determined that each appliance
remaining connected to the common venting
system properly vents when tested as outlined
above, return doors, windows, exhaust fans,
fireplace dampers and any other gas-burning
appliance to their previous conditions of use.
Any improper operation of the common venting
system should be corrected so the installation
conforms with the National Fuel Gas Code, ANSI
Z223.1 and CSA B149 Installation Code. When
resizing any portion of the common venting system,
the common vent system should be resized to
approach the minimum size as determined using the
appropriate tables.
Содержание MACH C1500
Страница 2: ...MACH Series Gas Fired Boiler Table of Contents...
Страница 49: ...MACH Series Gas Fired Boiler Limited Warranty Page 45...
Страница 50: ...MACH Series Gas Fired Boiler Appendix Page 46...
Страница 51: ...MACH Series Gas Fired Boiler Appendix Page 47 8 0 APPENDIX Date Hi Low Fire O2 CO CO2 Stack Temp pH Action By...