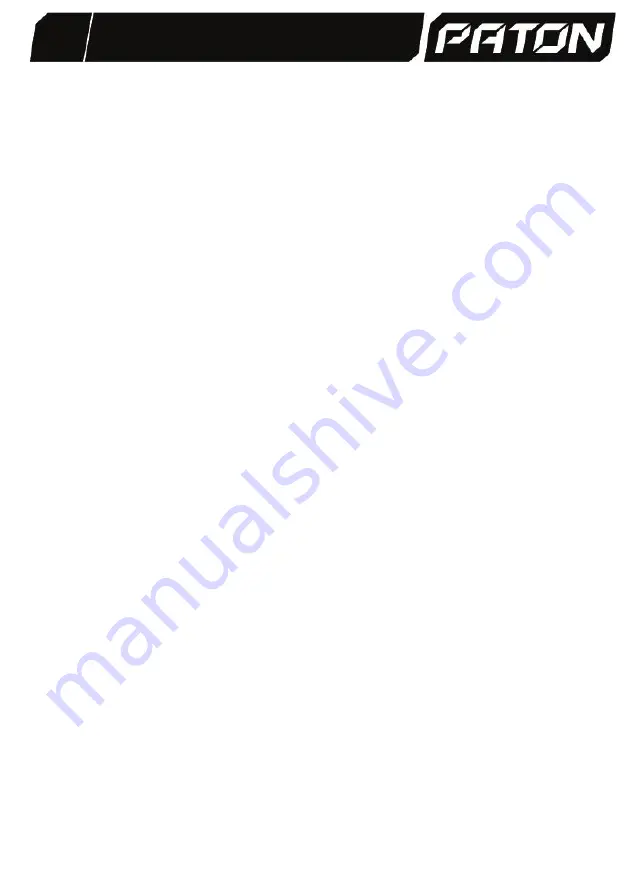
- 85 -
PATON
StandardMIG
DC MMA/TIG/MIG/MAG
Preparation for welding with
solid
wire:
- Plug the "ground" cable into the source
B "-"
socket;
- Connect the "ground" cable to the piece;
- Connect the power plug
13
of the wire feeder to the source
A "+"
socket;
- Connect and screw the semi-automatic welding torch to the socket
12
on the wire feeder
until it
stops
;
-
Install the reducer on the gas cylinder with safety gas "СО2", "Ar+CO2"
or "Ar";
- Connect the gas hose to the gas cylinder reducer and socket
16
on the rear panel of the
wire feeder;
- Open gas cylinder tap, check tightness;
- Connect power supply mains cable to the power supply;
- Turn the power switch
14
on the rear panel of the source to the "ON" position;
- Use button
6
to set the welding mode MIG/MAG. The modes are switched in a circle;
- If the digital wire feed speed display
8
does not come on, check fuse
15
(4A rating) on the
rear panel;
- Set the required welding voltage with the button
1
;
- Set the wire coil of the required diameter;
- Lift up the beam on the pressure roller;
- Lead the loose end of the wire through the input channel into the welding torch;
- Lower and clamp the welding wire between the rollers. The tension of the rollers is written
on the plastic handle. If there is no experience, then initially set to the middle position
(about 3);
- Use buttons
7
to set the required wire feed speed;
- Use button
6
to feed the wire through the whole channel and adjust the final tension of
the rollers according to the recommendations for semi-automatic welding, paying
special attention to the tension of the coil brake. The coil must be MINIMALLY clamped
and easily rotated, but spontaneous unrolling must not be observed. WARNING: If the
coil brake mechanism is not assembled correctly, it may "self-tighten" when the coil
rotates, which after a short time will lead to complete blockage of the wire and disrupt
the welding process. So please double-check this point before the first filling of the wire;
- If necessary, it is possible to adjust additional welding process functions on the welding
source and wire feeder. See section 6.1.
Do not forget about the safety gas supply. To check its availability in the channel of
the torch, there is a button
10
. When you press it, the wire is not fed. If you are a beginner
and have no experience in setting the optimal pressure for welding a particular product,
then at the first moment the gas pressure can be set higher than the optimal value of ~0.2
MPa. This will have little effect on the process, only the consumption of safety gas will
increase. However, to save money in the future, follow the general recommendations for
welding works with semi-automatic machines. Just start with the average wire feed speed
(~4.0 ... 6.0 m/min) and the average voltage at the source (~19V) at any diameter of the
installed wire
(Ф0.6…1.2 mm). It may not be optimal, but the unit s
hould already be
welding. To get the best result, you need to adjust the voltage of the source with buttons
1
and the wire feed speed with buttons
7
on the feeder according to the general
Содержание StandardMIG-160
Страница 1: ......
Страница 2: ......
Страница 100: ... 99 PATON StandardMIG DC MMA TIG MIG MAG PATON StandardMIG 270 400V 350 400V DC MMA TIG MIG MAG source circuit diagram ...