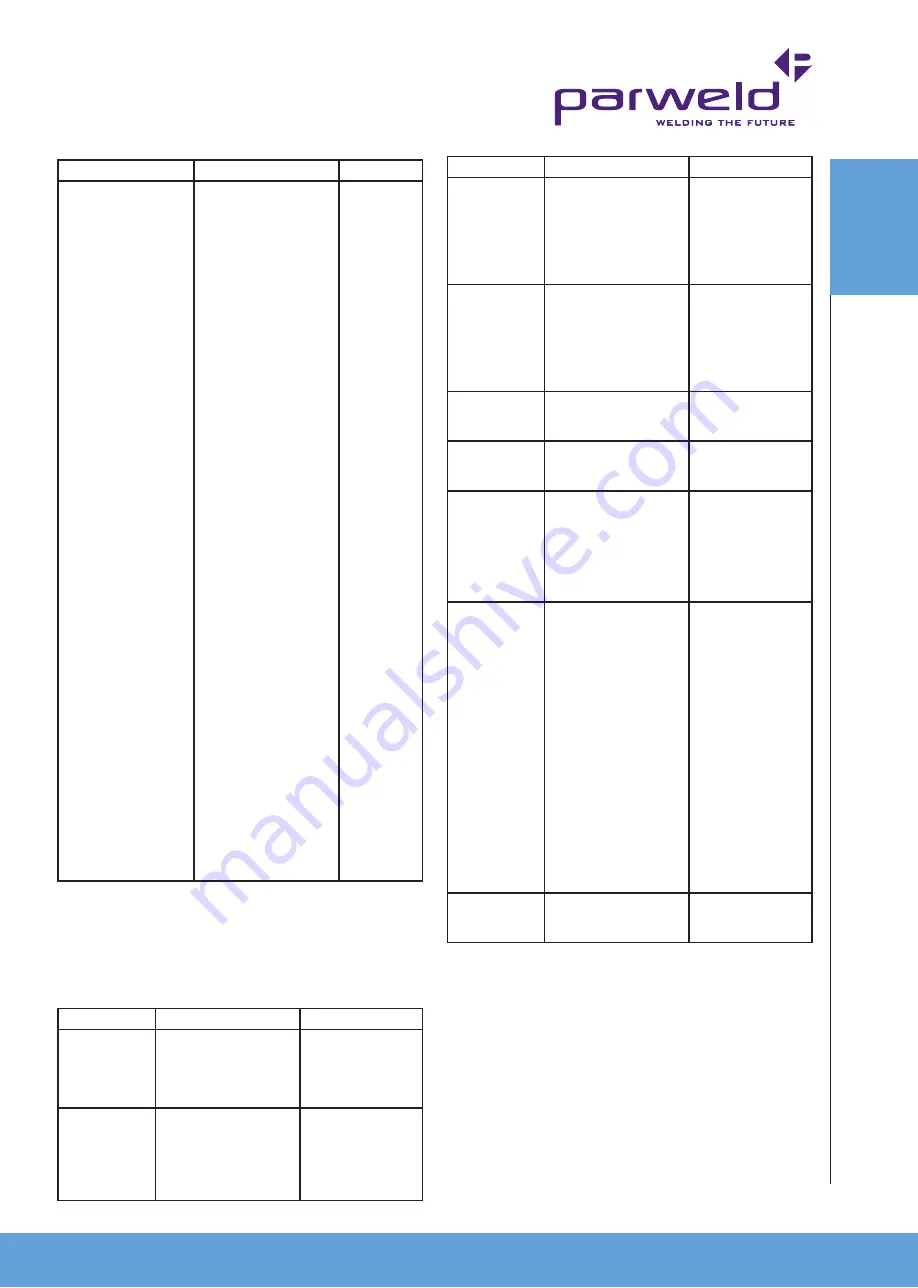
www.parweld.co.uk
www.parweld.co.uk
9
Description
Possible cause
Remedy
Nonmetallic particles
are trapped in the weld
metal (slag inclusion).
(a) Nonmetallic particles
may be trapped in
undercut from previous
run
(b) Joint preparation too
restricted
(c) Irregular deposits
allow slag to be trapped.
(d) Lack of penetration
with slag trapped
beneath weld bead.
(e) Rust or mill scale is
preventing full fusion.
(f) Wrong electrode for
position in which welding
is done.
(a) If bad
undercut
is present,
clean slag
out and
cover with
a run from
a smaller
diameter
electrode.
(b) Allow for
adequate
penetration
and room for
cleaning out
the slag
(c) If very
bad, chip
or grind out
Irregularities
(d) Use
smaller
electrode
with sufficient
current
to give
adequate
penetration.
adequate
penetration.
Use suitable
tools to
remove all
slag from
corners
(f) Use
electrodes
designed
for position
in which
welding
is done,
otherwise
proper
control
of slag is
difficult.
TIG welding problems
Weld quality is dependent on the selection of the correct
consumable, maintenance of equipment and proper welding
technique.
Description
Possible Cause
Remedy
Excessive bead
build up or poor
penetration or
poor fusion at
edges of weld
Welding current is too
low
Increase weld
current and/or faulty
joint preparation
Weld bead too
wide and flat
or undercut at
edges of weld
or excessive
burn through
Welding current is too
high
Decrease weld
current
Description
Possible Cause
Remedy
Weld bead
too small or
insufficient
penetration or
ripples in bead
are widely
spaced apart
Travel speed too fast
Reduce travel speed
Weld bead
too wide or
excessive
bead build up
or excessive
penetration in
butt joint
Travel speed too slow
Increase travel
speed
Uneven leg
length in fillet
joint
Wrong placement of
filler rod
Re-position filler rod
Electrode melts
when arc is
struck
Electrode is connected
to the ‘+’ terminal
Connect the
electrode to the ‘-‘
terminal
Dirty weld pool (a) Electrode
contaminated through
contact with work piece
or filler rod material
(b) Gas contaminated
with air
(a) Clean the elec-
trode by grinding off
the contaminates
(b) Check gas lines
for cuts and loose
fitting or change gas
cylinder
Electrode melts
or oxidizes
when an arc is
struck
(a) No gas flowing to
welding region
(b) Torch is clogged with
dust
(c) Gas hose is cut
(d) Gas passage
contains impurities
(e) Gas regulator is
turned off
(f) Torch valve is turned
off
(g) The electrode is too
small for the welding
current
(a) Check the gas
lines for kinks or
breaks and gas
cylinder contents
(b) Clean torch
(c) Replace gas
hose
(d) Disconnect gas
hose from torch
then raise gas
pressure to blow
out impurities.
(e) Turn on
(f) Turn on
(g) Increase
electrode diameter
or reduce the
welding current
Poor weld finish
Inadequate shielding
gas
Increase gas flow or
check gas line for
gas flow problems
FAUL
T
FINDING
Содержание XTS 163
Страница 1: ...OPERATOR MANUAL ISSUE 4 XTS 163 XTS 163 DV...