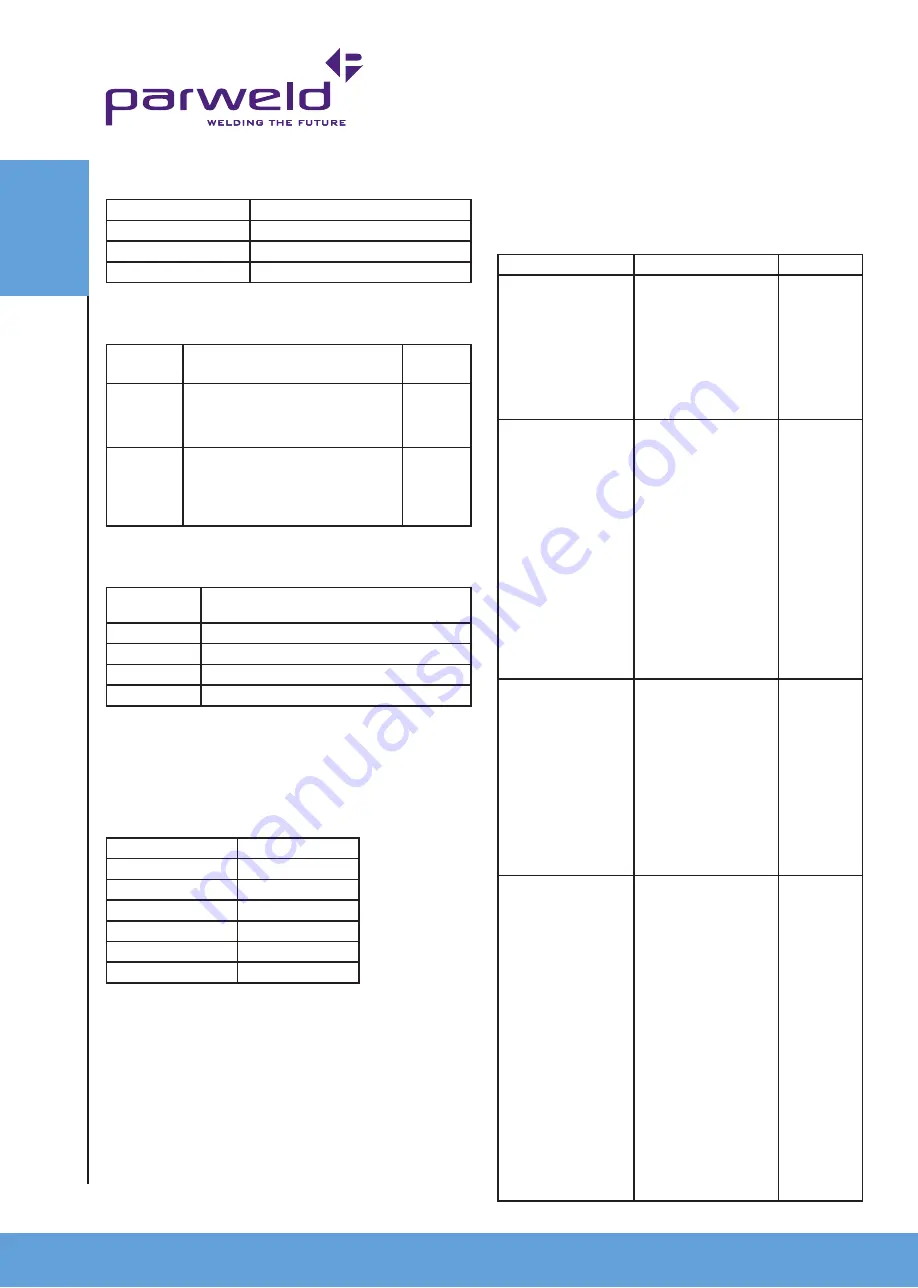
www.parweld.co.uk
www.parweld.co.uk
8
7.0 Fault Finding
MMA welding problem
Description
Possible cause
Remedy
Gas pockets or voids
in weld metal (porosity)
(a) Electrodes are damp
(b) Welding current is
too high.
(c) Surface impurities
such as oil, grease,
paint, etc
(a) Dry
electrodes
before use
(b) Reduce
welding
current
(c) Clean
joint before
welding
Crack occurring in
weld metal soon after
solidification.
(a) Rigidity of joint.
(b) Insufficient throat
thickness.
(c) Cooling rate is too
high.
(a) Redesign
to relieve
weld joint
of severe
stresses or
use crack
resistance
electrodes.
(b) Travel
slightly
slower to
allow greater
build up in
throat.
(c) Preheat
plate and
cool slowly.
A gap is left by failure
of the weld metal to fill
the root of the weld
(a) Welding current is
too low.
(b) Electrode too large
for joint.
(c) Insufficient gap
(d) Incorrect sequence
(a) Increase
welding
current
(b) Use
smaller
diameter
electrode.
(c) Allow
wider gap
(d) Use
correct build-
up sequence
Portions of the weld
run do not fuse to the
surface of the metal or
edge of the joint.
(a) Small electrodes
used on heavy cold plate
(b) Welding current is
too low
(c) Wrong electrode
angle
(d) Travel speed of
electrode is too high
(e) Scale or dirt on joint
surface
(a) Use
larger
electrodes
and preheat
the plate
(b) Increase
welding
current
(c) Adjust
angle so the
welding arc
is directed
more into the
base metal
(d) Reduce
travel speed
of electrode
(e) Clean
surface
before
welding.
TIG welding guide
Electrode diameter
DC current (amps)
0.040” (1.0mm)
30 – 60
1/16” (1.6mm)
60 – 115
3/32” (2.4mm)
100 – 165
Tungsten electrode types
Electrode
type
Welding application
Colour
code
Thoriated
2%
DC welding of mild steel, stainless
steel and copper. Excellent arc
starting, long life, high current carrying
capacity.
RED
Ceriated
2%
DC welding of mild steel, stainless
steel, copper, aluminium, their alloys
longer life, more stable arc, easier
starting, wider current range, narrower
more concentrated arc
GREY
Guide for selecting filler wire diameter
Filler wire
diameter
DC current range
1/16” (1.6 mm)
20 - 90
3/32” (2.4 mm)
65 - 115
1/8” (3.2 mm)
100 - 165
3/16” (4.8 mm)
200-350
The filler wire diameter specified is a guide only, other diameter
wires may be used according to the welding application
.
Shielding gas selection
Alloy
Shielding gas
Aluminium & alloys
Pure Argon
Carbon steel
Pure Argon
Stainless steel
Pure Argon
Nickel alloy
Pure Argon
Copper
Pure Argon
Titanium
Pure Argon
FAUL
T
FINDING
Содержание XTS 163
Страница 1: ...OPERATOR MANUAL ISSUE 4 XTS 163 XTS 163 DV...