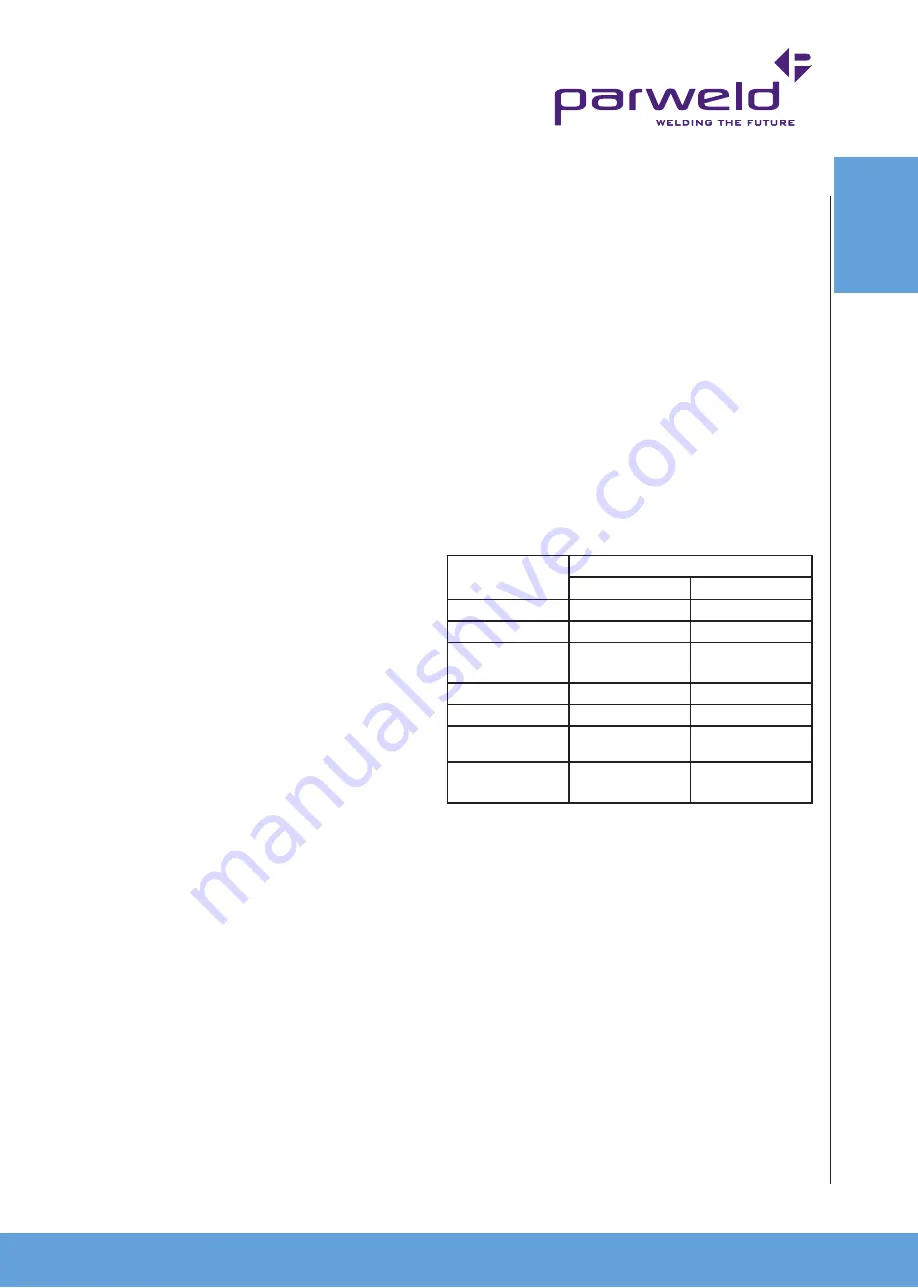
www.parweld.co.uk
www.parweld.co.uk
5
Watch for fire, and keep a fire extinguisher nearby. Be aware that
welding on a ceiling, floor, bulkhead, or partition can cause fire on
the hidden side.
Do not weld on closed containers such as tanks, drums, or pipes,
unless they are properly prepared according to local regulations
Connect work cable to the work as close to the welding area as
practical to prevent welding current from travelling along possibly
unknown paths and causing electric shock, sparks, and fire hazards.
Wear oil-free protective garments such as leather gloves, heavy
shirt, cuffless trousers, high shoes, and a cap. Remove any
combustibles, such as a butane lighter or matches from your person
before doing any welding.
FLYING METAL can injure eyes.
Welding, chipping, wire brushing, and grinding cause sparks and
flying metal. As welds cool they can throw off slag. Wear approved
safety glasses with side shields even under your welding helmet.
BUILD UP OF GAS can injure or kill.
Shut off shielding gas supply when not in use. Always ventilate
confined spaces or use approved air-supplied respirator.
HOT PARTS can cause severe burns.
Do not touch hot parts with bare hands.
Allow cooling period before working on gun or torch.
To handle hot parts, use proper tools and/or wear heavy, insulated
welding gloves and clothing to prevent burns.
MAGNETIC FIELDS can affect pacemakers.
Pacemaker wearers keep away.
Wearers should consult their doctor before going near arc welding,
gouging, or spot welding operations.
NOISE can damage hearing.
Noise from some processes or equipment can damage hearing.
Wear approved ear protection if noise level is high.
Shielding gas cylinders contain gas under high pressure.
CYLINDERS can explode if damaged.
Protect compressed gas cylinders from excessive heat, mechanical
shocks, physical damage, slag, open flames, sparks, and arcs.
Install cylinders in an upright position by securing to a stationary
support or cylinder rack to prevent falling or tipping. Keep cylinders
away from any welding or other electrical circuits. Never drape a
welding torch over a gas cylinder. Never allow a welding electrode to
touch any cylinder. Never weld on a pressurized cylinder - explosion
will result. Use only correct shielding gas cylinders, regulators,
hoses, and fittings designed for the specific application; maintain
them and associated parts in good condition.
Turn face away from valve outlet when opening cylinder valve.
Use the right equipment, correct procedures and sufficient number of
persons to lift and move cylinders.
Read and follow instructions on compressed gas cylinders,
associated equipment and Compressed Gas Association (CGA)
recommendations.
2.0 Product Description
This welding machine is manufactured using advanced inverter
technology. The input voltage is rectified to DC and then inverted
to high frequency AC voltage. before being converted back to DC for
the output .This allows the use of a much smaller transformer and so
allowing weight saving and improved power efficiency.
3.0 Technical
Specifications
Machine Model
XTS 163
XTS 163 DV
Input voltage
230V +/- 10%
230/110V +/- 10%
Frequency
50/60Hz
50/60Hz
Input current
31.7A max
15.9 eff
31/44A max
15.5/17 eff
Fuse rating
16A
16/32A
Output OCV
60
60
Output load
voltage
20.2-26.4
20.2-26.4
Output Current
5-160A DC
5-160A DC (230V)
5-140A DC (110V)
SAFETY
Содержание XTS 163
Страница 1: ...OPERATOR MANUAL ISSUE 4 XTS 163 XTS 163 DV...