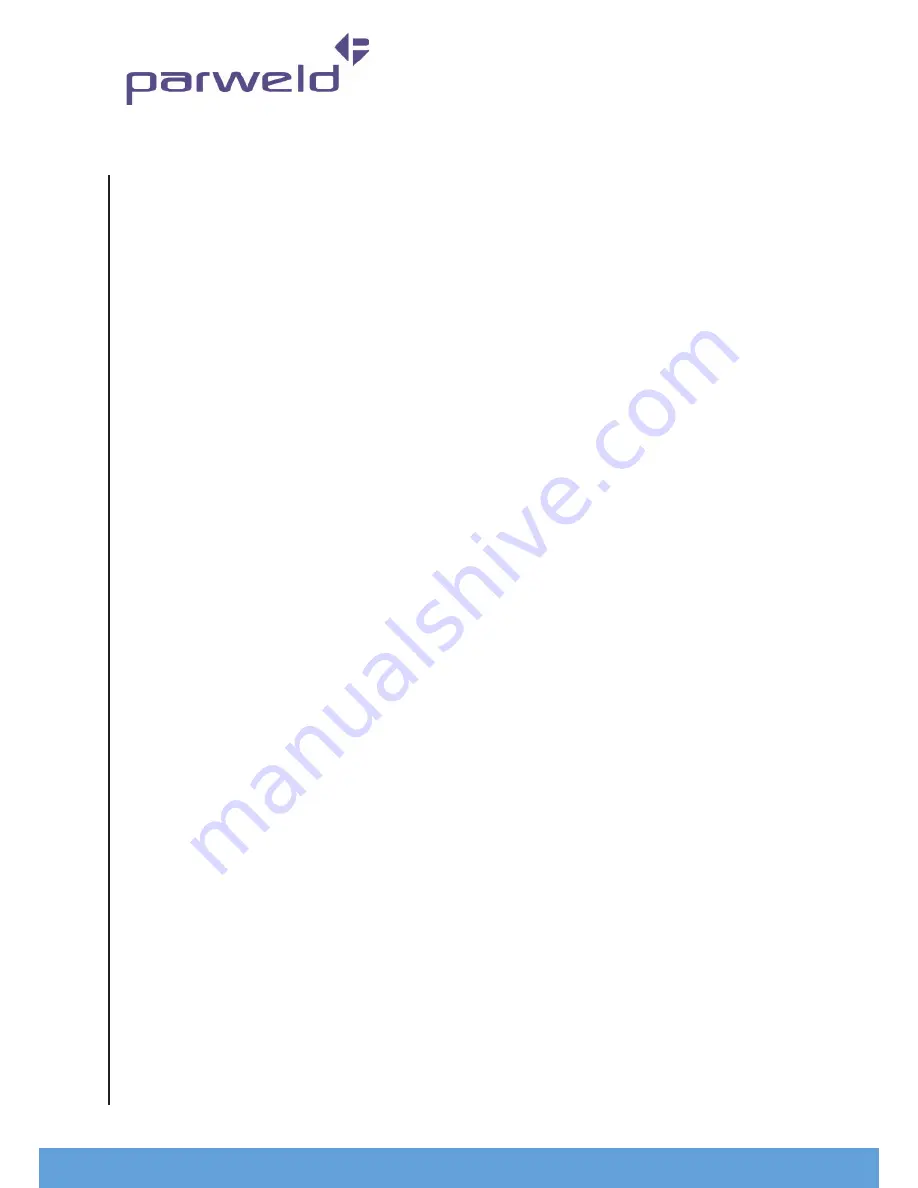
www.parweld.com
10
CONTR
OLS
6. Trim the electrode wire to within 5mm of the
face of the nozzle, this will facilitate jolt free arc
initiation.
7. Press the gas purge button and check the gas flow
is adequate for your application.
8. An inexpensive flow meter is available from
Parweld reference 806001.
9. If you are setting a water-cooled torch ensure you
have the recommended water flow rate.
Note;- It is essential to ensure adequate flow of clean,
cool water to prevent irreparable torch failure, a
minimum of 1.2 l/min is recommended.
Parweld recommend the use of its XTS water
recirculation system designed specifically for use with
all water cooled MIG, TIG and Plasma welding torches.
The Parweld XTS recirculation equipment can be fitted
with a fail-safe flow protection device to prevent
overheating or meltdown.
Note. Water flows into the torch through the blue
hose. The blue hose delivers cold water directly
to the prime source of heat, the swan neck and
consumables. The re circulated water is then passed
through the torch power cable to cool the power cable
as it is returned to the cooler through the red water
return lead.
Ensure all air is removed from the water cooling circuit
before welding.
5.9 Work return lead connection
Insert the work return lead connector into the
receptacle on the front panel of the machine and twist
it clockwise until tightly secured.
Connect the earth clamp to the work piece as close as
possible to the point to be welded and ensure that a
good electrical connection is created to bare metal.
Note the XTM403S has 2 work return lead sockets
providing different inductance settings refer to the
Operating instructions for your perfered setting.
5.10 Shielding gas connection
1.
Connect gas hose to the output connection of a
gas regulator capable of supplying the correct gas
flow for the welding operation.
Note if the gas cylinder is to be stored on the back of
the machine ensure it is secured using the retention
chain provided
6.0 Operation
1. Switch on the machine using the switch no the
front panel, this lights the Green LED on the front
panel.
2. Turn the “VOLTAGE SELECTOR” switches Set
voltage midway between high/low voltages.
NOTE: Check that drive rolls, and torch parts are
correct for the wire size and type being used.
3. The optimum idle roll pressure varies with
type of wire, wire diameter, surface conditions,
lubrication, and hardness. As a general rule, hard
wires may require greater pressure, and soft, or
aluminium wire, may require less pressure than
the factory setting. The optimum idle roll setting
can be determined as follows:
4. Press end of gun against a solid object that is
electrically isolated from the welder output and
press the gun trigger for several seconds.
5. If the wire “bird nests”, jams or breaks at the
drive roll, the idle roll pressure is too great. Back
the adjustment knob out 1/2 turn, run new wire.
If the only result was drive roll slippage, loosen
the Hand nut on the central connector and pull
the gun forward about 6” (15cm) away from the
power source. There should be a slight waviness
in the exposed wire. If there is no waviness, the
pressure is too low. Tighten the adjustment knob
1/4 turn, reinstall the gun cable and repeat the
above steps.
6.1 Feeding wire electrode
Note when triggering, the electrode and drive
mechanism are electrically “LIVE” relative to work and
ground and remain “LIVE” several seconds after the
gun trigger is released.
WARNING
When using an open arc process, it is necessary to use
correct eye, head, and body protection.
1. Position wire over joint. The end of the wire may
be lightly touching the work.
2. Lower welding helmet, operate gun trigger, and
begin welding. Hold the gun so the contact tip to
work distance is about 3/8” (10 mm).
3. To stop welding, release the gun trigger and then
pull the gun away from the work after the arc goes
out.
4. When no more welding is to be done, close valve
on gas cylinder (if used), momentarily operate gun
trigger to release gas pressure and turn off the
machine.
6.2 Optimising weld parameters
NOTE These settings are guidelines only. Material and
wire type, joint design, fit up, position, shielding gas,
etc. affect settings. Produce test welds to be sure they
comply to specifications.
Material thickness determines weld parameters.
1. Convert Material Thickness to Amperage (A)
(0.25mm= 1 Amp) 3.2mm = 125 A
2. Select Wire Size
Amperage Range
Wire Size
40 - 145 A
0.8 mm
50 - 180 A
1.0 mm
75 - 250 A
1.2 mm
3. Select Wire Speed (Amperage)
Wire Size
Feed speed