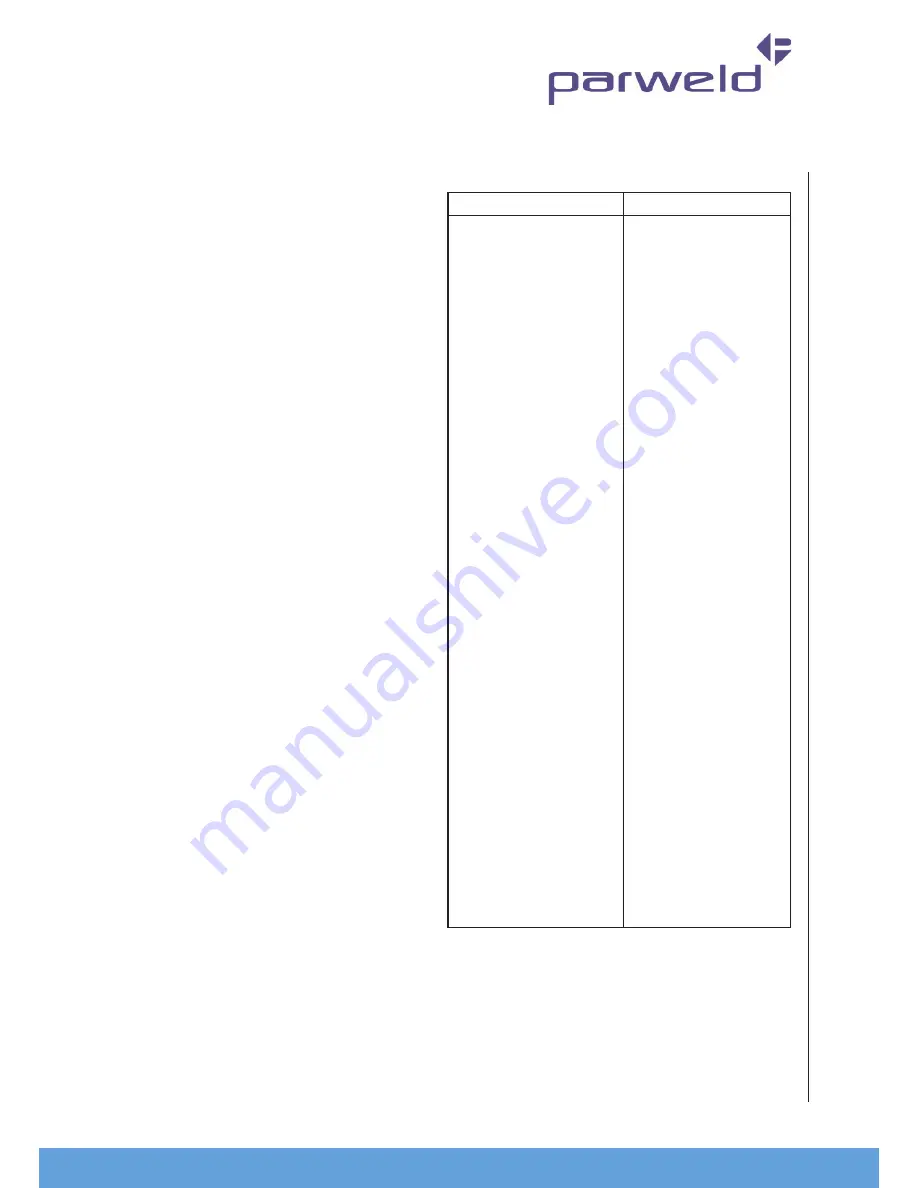
www.parweld.com
11
0.8 mm
0.05m/min per Amp
1.0 mm
0.04m/min per Amp
1.2 mm
0.025m/min per Amp
So based on 3.2 mm material thickness amperage
should be 125A if using 1.0mm wire then the wire
feed speed should be
0.04 X 125= 5m/min
Wire speed (amperage) controls weld penetration
4. Select Voltage. Voltage controls height and width
of weld bead.
Low Voltage: wire stubs into work
High Voltage: arc is unstable (spatter)
Set voltage midway between high/low voltages.
And then fine tune accordingly
NOTE These settings are guidelines only. Material and
wire type, joint design, fit up, position, shielding gas,
etc. affect settings. Produce test welds to be sure they
comply to specifications.
6.3 Additional welding controls
Burn back adjustment. when welding at high
amperages the wire can often burn back onto or close
to the contact tip to prevent this happening you can
increase the burn back control (18) located inside the
wire spool cover.
Soft Start. The soft start control slows the acceleration
of the wire feed motor as the act starts and so reduces
wire snubing and spatter at the weld start. This control
should be adjusted to give a smoother start to the
weld. (17).
Inductance setting XTM403S only. This allows 2 levels
of inductance to give the desired arc characteristics
typically for low amperage with dip transfer you
should use the low inductance setting as this speeds
the burn off of the wire in dip transfer mode. For
higher amperages and spray transfer the higher
inductance setting is preferable.
7.0 Fault finding
Problem
Cause/Corrective Action
Porosity - small cavities or
holes
Resulting from gas
pockets in weld metal.
Inadequate shielding
gas coverage. Check for
proper gas flow rate.
Remove spatter from
gun nozzle.
Check gas hoses for
leaks.
Eliminate drafts near
welding arc.
Place nozzle 6-13 mm
from work piece Hold
gun near bead at end of
weld until molten metal
solidifies.
Wrong gas. Use welding
grade shielding gas;
change to different gas.
Dirty welding wire. Use
clean, dry welding wire.
Eliminate pickup of oil
or lubricant on welding
wire from feeder or
liner.
Work piece dirty.
Remove all grease, oil,
moisture, rust, paint,
coatings, and dirt from
work surface before
welding. Use a more
highly deoxidizing
welding wire (contact
supplier).
Welding wire extends
too far out of nozzle.
Be sure welding wire
extends not more than
13 mm beyond nozzle.