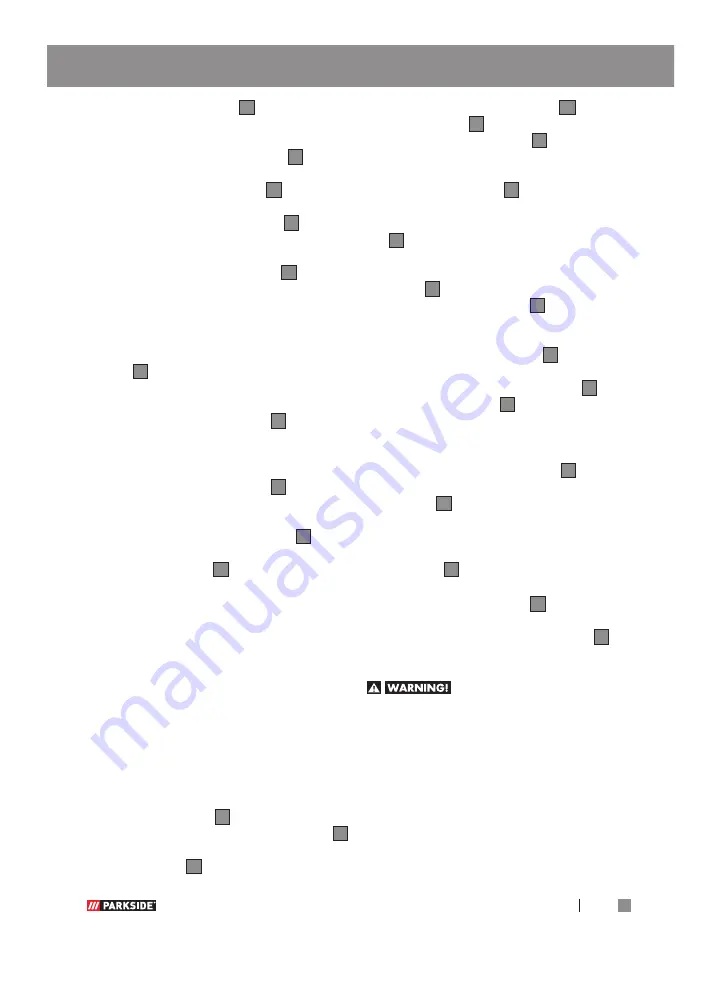
49
GB/IE
Place the roll mount
34
back on and
lock it by pressing and turning it
anti-clockwise (see Figure H).
Undo the adjustment screw
31
and
swing it forwards (see Figure I).
Turn the thrust roller unit
32
to the
side (see Figure J).
Loosen the feed roll holder
33
by
turning it anti-clockwise and pull it
forwards and off (see Figure K).
On the top of the feed roll
19
,
check whether the appropriate wire
thickness is indicated. If necessary,
the feed roll has to be turned over or
replaced. The supplied welding wire
(Ø 0.8 mm) must be used in the feed
roll
19
with t
he specified wire thick-
ness of Ø 0.8 mm. The wire must be
positioned in the front groove!
Erect the feed roll holder
33
again
and screw clockwise direction.
Make sure that the feed roll holder is
properly aligned (see Figures I, J).
Remove the torch nozzle
37
by
pulling and turning it anti-clockwise
(see Figure L).
Unscrew the welding nozzle
16
(see Figure L).
Guide the torch
7
away from
the welding device as straight as
possible (place it on the floor).
Take the wire end out of the edge of
the spool (see Figure M).
Trim the wire end with wire scissors
or a diagonal cutter in order to
remove the damaged, bent ends of
the wire (see Figure M).
Note:
The wire must be kept under ten-
sion the entire time in order to avoid
a releasing and a roll out! Therefore it
is recommended to carry out the work
with an additional person.
Push the flux-cored wire through the
wire feed guide
35
(see Figure N).
Guide the wire along the feed roll
19
and then push it into the flux-cored
wire holder
36
(see Figure O).
Swivel the thrust roller unit
32
towards
the feed roll
19
(see Figure P).
Mount the adjustment
31
screw
(see Figure P).
Set the counter pressure with the
adjustment screw
31
. The welding
wire must be firmly positioned
between the thrust roller and feed roll
19
in the front groove without being
crushed (see Figure P).
Switch on the welding device on the
main
12
switch (see Figure A).
Press the torch button
8
.
Now the wire feed system pushes
the welding wire through the cable
assembly and the torch
7
.
As soon as 1 – 2 cm of the wire
protrudes from the torch neck
38
,
release the torch
8
button again
(see Figure Q).
Switch off the welding device on the
main switch.
Screw the welding nozzle
16
back
on. Make sure that the welding
nozzle
16
matches the diameter of
the welding wire used (see Figure R).
When using the delivered welding
wire (Ø 0.8 mm), the welding nozzle
with the
16
labelling 0.8 mm must be
used.
Push the torch nozzle
37
back
on to the torch neck by turning it
anti-clockwise at the same time
38
(see Figure S).
Always unplug the mains
plug from the socket prior to each
maintenance task or preparatory work
in order to prevent the risk of an electric
shock, injury or damage.
Welding with flux-cored wire
Содержание PSGS 120 A1
Страница 11: ...A B C D 15 16 17 19 20 21 18 E 22 23 24 25 5 1 2 6 4 3 11 12 7 8 29 30 14 13 28 27 9 10 14 14 14 26 26...
Страница 12: ......
Страница 41: ...32 DE AT CH...
Страница 117: ...108 NL BE...
Страница 145: ...136 PL...