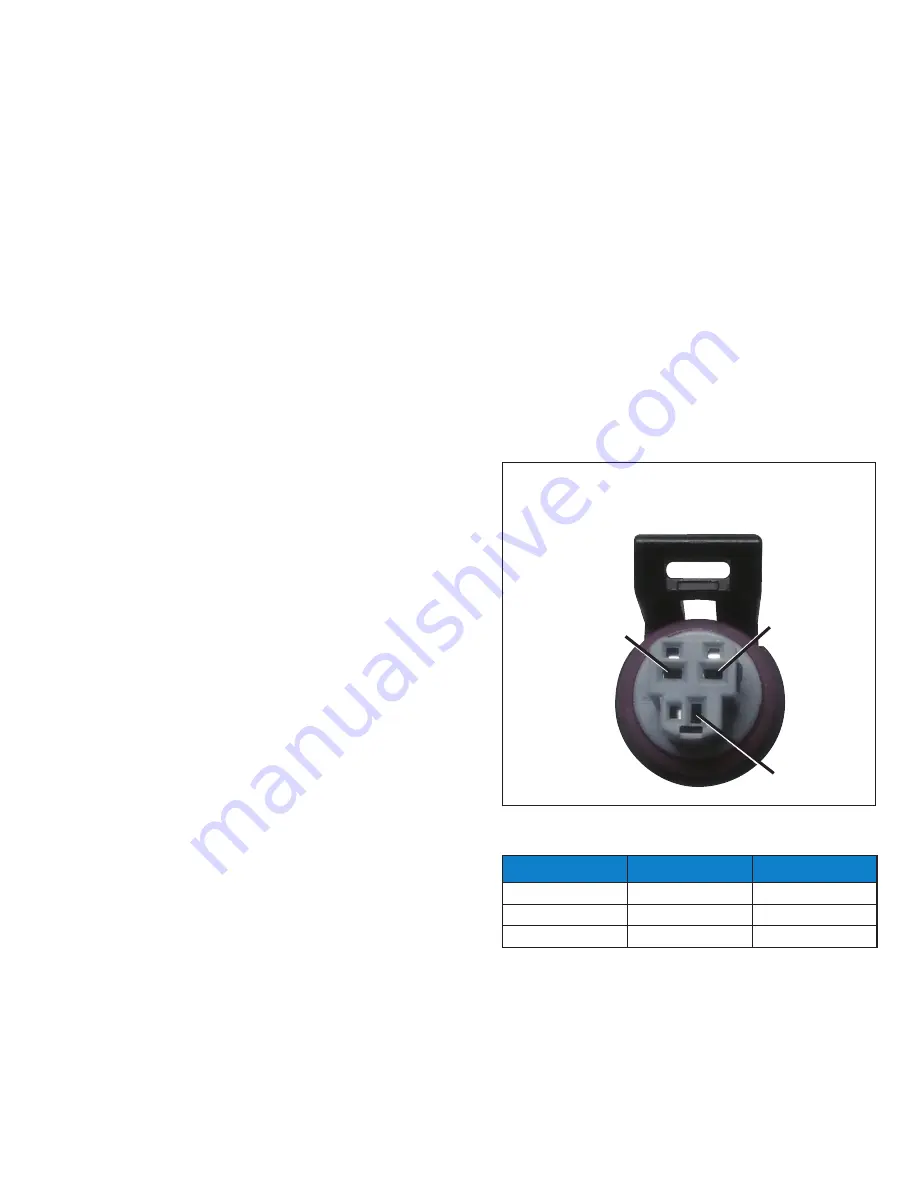
Bulletin 100-50-5.2 –
Page 7
These actions are inversely proportional in nature. If the sub-
cooled liquid temperature or Superheat are slow to react to a
transient system change, then the Proportional may be too low
and or the Integral value may be too high in value.
Note: Not all refrigeration systems are designed alike. Use
caution when tuning PID setpoints.
7. Troubleshooting
Recommendations
As with any refrigeration component troubleshooting, actual
system conditions should be verified with a gauge set and
calibrated temperature sensor (i.e verify actual superheat,
subcooling and refrigerant condition). This system infor-
mation is valuable in determining whether it is component
related or system related.
For systems or applications that experience light loads on the
Subcool control circuit, it is important that the Heat exchanger
and refrigerant lines are sized correctly. This will ensure
proper oil return and will minimize the effects of oil logging
in the Heat exchanger. Many Heat exchanger manufacturers
recommend a hot gas bypass for loads below 50%. Refer to
the heat exchanger manufacturer’s installation instructions.
Sensors
Failed sensors will trigger an alarm. An alarm code will show
which sensor is mis-wired, disconnected, or faulty. (See Ap-
pendix G - Alarms and Failsafes
, page 14.) The alarm will
persist until the problem is corrected.
Failed temperature sensors
will generally read extremely
low or infinite resistance when tested with an ohmmeter.
Readings should be taken with the sensor disconnected from
the Subcool Control. A missing or disconnected temperature
sensor will read
-60
on the controller.
Temperature sensor output can be checked by measuring the
DC voltage across the sensor wire using the tables in Appen-
dix L
, page 19 and Appendix M, page 20.
Since the liquid and suction temperature sensors are identical,
no alarm will be triggered if the sensors are switched (i.e. liq-
uid sensor on the suction line).
Severe system damage may
occur if these two sensor locations are interchanged.
Pressure transducers
must be installed tight enough to de-
press the valve stem in the fitting. Failure to do so will result
in erroneous pressure readings and possibly leaks.
Pressure transducers should be tested while connected to
the controller and powered. Test at the controller terminals.
Voltage between terminals 34 and 35 should be 4.8 - 5.2 volts
DC. Voltage between 33 and 34 should be between 0.5 and
4.5 volts DC. See Table 1 - Pressure Transducer Wire Colors,
page 4.
To test the accuracy of the transducer, use a gauge set to
obtain the actual system pressure. For volts-to-pressure
conversion, measure the voltage between terminals 33 and
34. Identify the pressure transducer used and find the correct
range
Prng
in Table 3.
Substitute the measured voltage (
v
) in the formula in the PSI
column. The result should be within 3 psi of the actual system
pressure shown on the gauge set. If not, check transducer for
proper installation, correct schrader valve, and verify the pres-
sure range identified on the transducer.
To test the transducer cable, disconnect the cable from the
transducer and check for 4.8 - 5.2 volts between terminals
+
and
–
. See Figure 5 - Pressure Sensor Cable.
Table 3 - Pressure Transducer Specifications
LABEL COLOR
Prng
PSI
Green
150
(v-.5) x 37.5
None / Silver
300
(v-.5) x 75
Yellow
500
(v-.5) x 125
Figure 5 - Pressure Sensor Cable
S
–
+
+ Black
- Green
S White