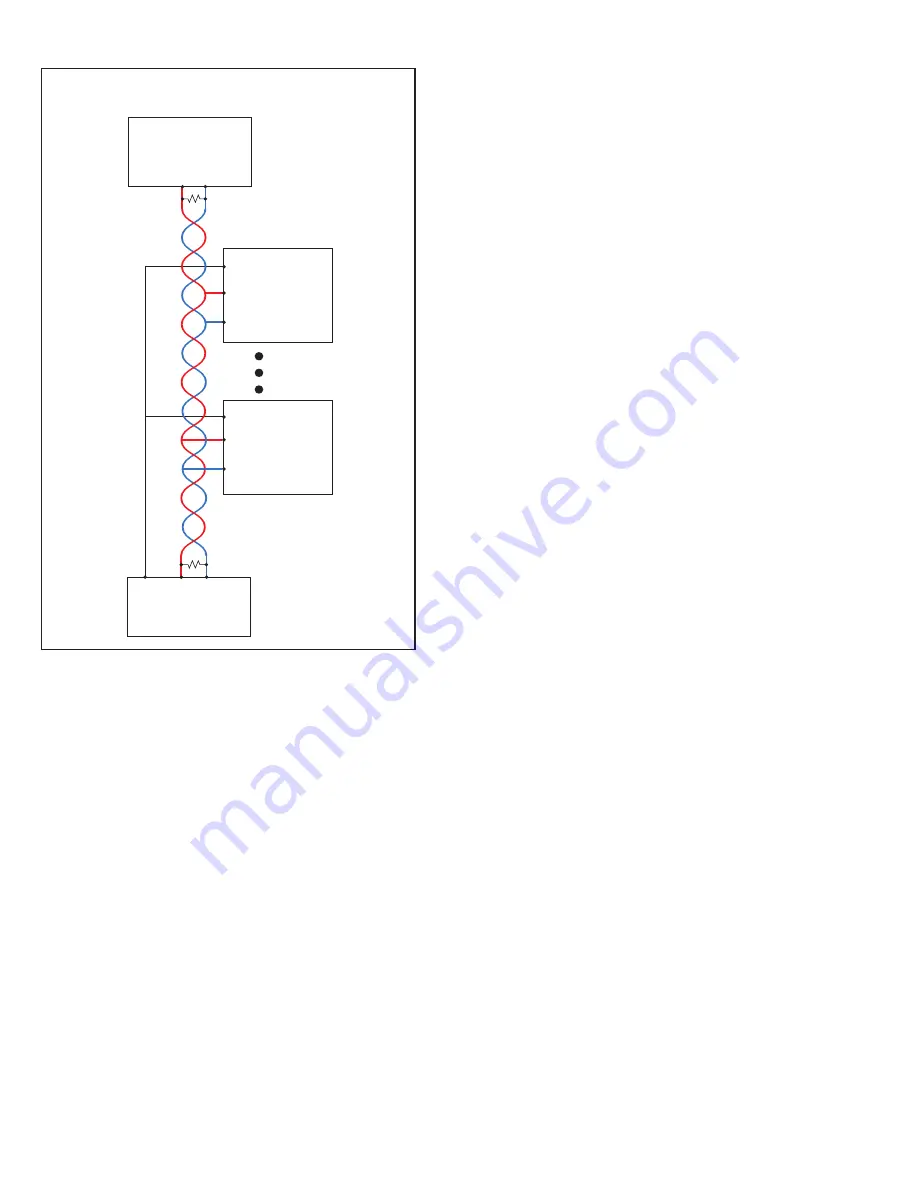
Page 6
– Bulletin 100-50-5.2
Recommended Network Configuration:
Daisy Chain, a
single continuous transmission line from one end to the other.
Other configurations involving triple-lug connections, such as
star, are not recommended. See Figure 3.
Addr
-
The address of the controller on the MODBUS net-
work. See Section 3 - Setpoint Menu Operation to change it.
Noise Reduction:
Termination resistance (
R
T
in Figure 4)
is recommended to reduce reflections and noise on the data
transmission lines. Place the resistance at the extreme
ends of
the cable with the resistance value matching the characteristic
impedance of the transmission line (typically 120 ohms for
twisted pair cables).
Shielding prevents noise from EMI sources. If the cable is
shielded, connect the shield to earth ground at one end only.
Do not connect shield to RS485 GND.
Keep RS485 wiring away from high voltage AC lines to
reduce noise and data errors on communication lines. RS485
communication cable should be perpendicular to AC lines at
any intersection.
Grounding:
Connect a third conductor to RS485 GND (pin 13)
to prevent ground potentials from node to node. This conduc-
tor should be included in the shield of the twisted pair cable to
prevent noise. Do not connect RS485 GND to earth ground.
Figure 4 - Modbus Wiring
Controller 1
GND
R
T
R
T
Communication
Master
A B
B
Controller n
R
T
-
Termination
resistor
B
A
Controller n-1
GND
B
A
A
GND
Third Party Controllers:
To avoid nuisance “network errors”,
the use of third party controllers on the same RS485 network
with Sporlan controllers and master is not recommended. If
necessary, use a separate communication board on the master
to connect separate third-party controllers.
See Appendix K - MODBUS Memory Map, page 17. Also,
refer to the documentation supplied with the communication
master for additional RS485 network requirements.
6. PID Tuning
The Sporlan Subcool Control is factory programmed with de-
fault Proportional–Integral–Derivative (PID) settings that will
provide efficient control. It may be necessary, however, to fine
tune the PID settings in applications where systems experi-
ence rapid transient conditions (such as frequent “impulse”
changes in loading or mass flow rates).
The controller offers PID adjustments for both Subcooled
liquid temperature and Superheat control. In most instances,
adjustments to the PI set-points are adequate. If tuning is
needed, see Section 3 - Setpoint Menu Operation to enter
the PID setpoint menu. The following guidelines should be
followed:
•
Lp
(Liquid Proportional Coefficient) – Increase value to in-
crease valve response to Subcooled liquid out temperature.
•
Li
(Liquid Integral Coefficient) – Increase value to
decrease valve response to Subcooled liquid out tempera-
ture over a given time period.
•
Ld
(Liquid Derivative Coefficient) – Increase value to
increase valve response to rate of change in Subcooled
liquid out temperature.
•
Sp
(Superheat Proportional Coefficient) – Increase value
to increase valve response to Superheat.
•
Si
(Superheat Integral Coefficient) – Increase value to
decrease valve response to Superheat over a given time
period.
•
Sd
(Superheat Derivative Coefficient) – Increase value to
increase valve response to rate of change in Superheat.
• LSHi
(Low Superheat Integral Coefficient) – Increase
value to decrease valve response to superheat over a given
time period (Only in low Superheat conditions).
If PID adjustments are made, allow adequate time for the sys-
tem to respond to the changes.
Large oscillations in Subcooled liquid or Superheat may require
adjustments to the respective PID values. If Subcooled liquid
and Superheat are equally unstable, adjust the Superheat PID
values first, followed by the liquid PID values.
•
When the Superheat is oscillating to extremes, the Propor-
tional value may be too high and/or the Integral value may
be too low.
•
If the Superheat is not oscillating to extremes, but the
Liquid control is very inconsistent around setpoint, then the
Proportional value may need to be reduced or the Integral
value increased.